Improving OEE in High-Tech Manufacturing by Monitoring Vacuum Chamber Performance
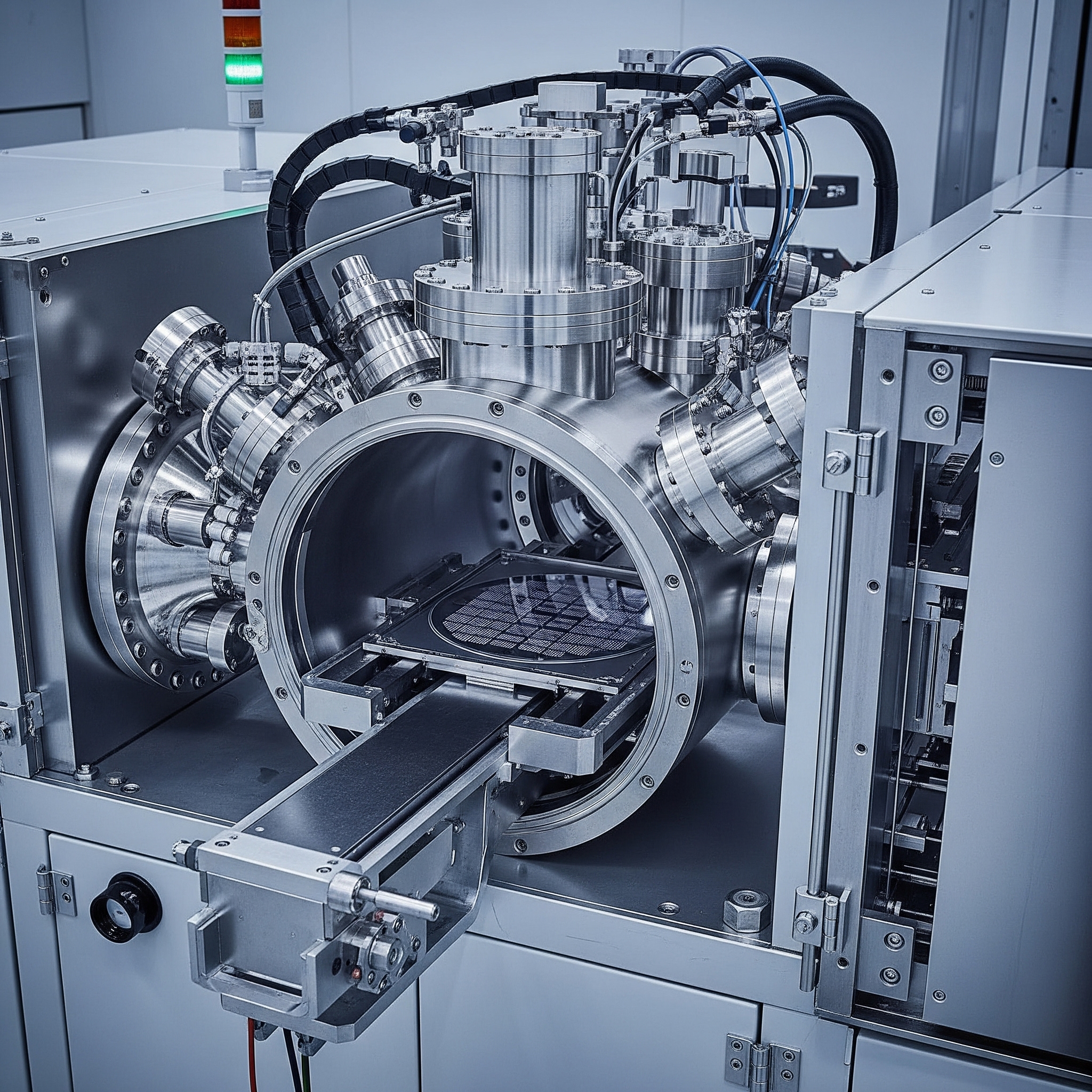
Situation
In the discrete manufacturing of high-tech components for the semiconductor industry, certain production steps must occur in vacuum chambers to avoid particle contamination. These vacuum processes demand tight environmental control to meet extreme purity and quality standards.
One critical phase is the evacuation time—the duration it takes for a vacuum chamber to reach the target pressure after the chamber door is closed. This period directly impacts Overall Equipment Effectiveness (OEE). Prolonged evacuation times slow down cycle throughput and may indicate equipment wear or failure, such as degraded seals or faulty vacuum pumps.
Problem
The manufacturer lacked a way to:
- Monitor vacuum evacuation time in real time
- Detect deviations from expected values
- Trigger alerts when vacuum performance degraded
Without this visibility, issues like seal degradation or vacuum pump failure remained unnoticed until quality or throughput problems emerged. This led to reduced equipment availability, longer cycle times, and ultimately, lower OEE.
Solution
Automated monitoring and alerting was implemented to track vacuum chamber evacuation times.
- Evacuation time is now calculated automatically by measuring the time between when the chamber door closes and when the target vacuum pressure is reached.
- Value-based search and notification logic was configured: if the evacuation time exceeds a predefined threshold, an email alert is sent, and a context item is created for documentation and analysis.
- This enables operators and engineers to quickly respond to anomalies and maintain optimal chamber performance.
Results
- Automated deviation detection: Immediate alerts when evacuation time exceeds acceptable limits
- Faster root cause analysis: Helps identify worn seals, vacuum leaks, or pump inefficiencies
- Improved preventive maintenance: Issues can be addressed before they cause downtime
- Higher OEE: Optimized process cycle times and reduced unplanned stoppages
Value
- Enhanced process visibility and control
- Improved yield and equipment availability
- Early detection of equipment degradation
- Stronger foundation for predictive maintenance strategies
Situation
In the discrete manufacturing of high-tech components for the semiconductor industry, certain production steps must occur in vacuum chambers to avoid particle contamination. These vacuum processes demand tight environmental control to meet extreme purity and quality standards.
One critical phase is the evacuation time—the duration it takes for a vacuum chamber to reach the target pressure after the chamber door is closed. This period directly impacts Overall Equipment Effectiveness (OEE). Prolonged evacuation times slow down cycle throughput and may indicate equipment wear or failure, such as degraded seals or faulty vacuum pumps.
Problem
The manufacturer lacked a way to:
- Monitor vacuum evacuation time in real time
- Detect deviations from expected values
- Trigger alerts when vacuum performance degraded
Without this visibility, issues like seal degradation or vacuum pump failure remained unnoticed until quality or throughput problems emerged. This led to reduced equipment availability, longer cycle times, and ultimately, lower OEE.
Solution
Automated monitoring and alerting was implemented to track vacuum chamber evacuation times.
- Evacuation time is now calculated automatically by measuring the time between when the chamber door closes and when the target vacuum pressure is reached.
- Value-based search and notification logic was configured: if the evacuation time exceeds a predefined threshold, an email alert is sent, and a context item is created for documentation and analysis.
- This enables operators and engineers to quickly respond to anomalies and maintain optimal chamber performance.
Results
- Automated deviation detection: Immediate alerts when evacuation time exceeds acceptable limits
- Faster root cause analysis: Helps identify worn seals, vacuum leaks, or pump inefficiencies
- Improved preventive maintenance: Issues can be addressed before they cause downtime
- Higher OEE: Optimized process cycle times and reduced unplanned stoppages
Value
- Enhanced process visibility and control
- Improved yield and equipment availability
- Early detection of equipment degradation
- Stronger foundation for predictive maintenance strategies
Download now
Subscribe to our newsletter
Stay up to date with our latest news and updates.
Other Webinars on Demand
Press Play on Operational Improvement
Other Resources
Explore Our Newest Content to Maximize Your Operational Efficiency