A Practical Guide to Manufacturing Process Optimization
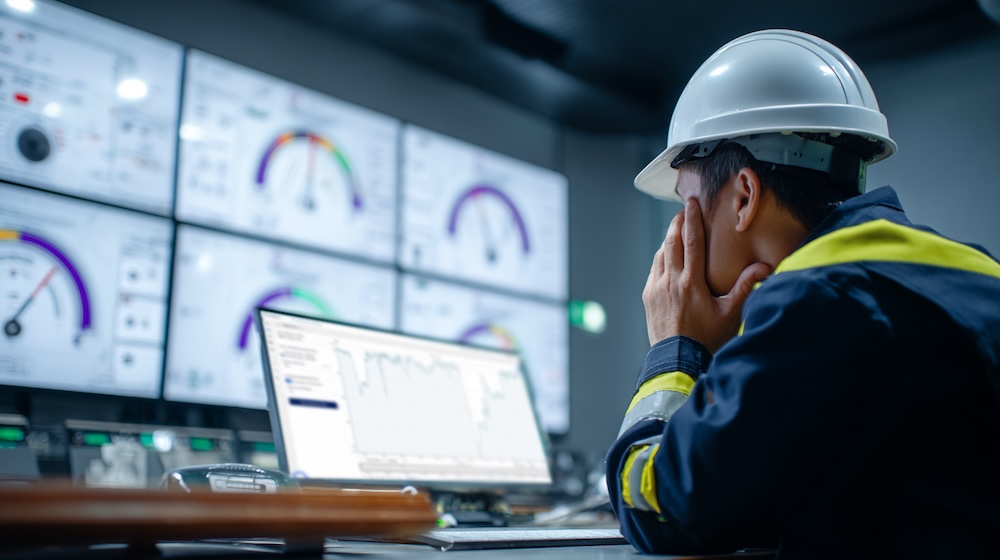
Table of Contents
The Persistent Challenge of Operational Inefficiency
Every hour of production generates vast amounts of data. It also, unfortunately, generates waste—in the form of off-spec products, lost time, and underutilized resources. This is the hidden cost of inefficiency, paid every time a process deviation goes unnoticed, a machine runs below its optimal capacity, or an engineer spends hours exporting data into spreadsheets to find the root cause of a problem.
For engineers and plant managers, the goal is clear: build a more resilient, predictable, and profitable operation. The path to achieving this is through manufacturing process optimization. This isn’t about one-off fixes; it's the systematic redesign of workflows to make them faster, more reliable, and less costly.
This guide provides a practical roadmap for achieving that operational excellence. We'll explore foundational techniques, examine the role of modern digital tools, and look at industry-specific manufacturing process optimization examples to help you turn your production floor into a more significant competitive advantage.
The Business Case for Process Optimization
Investing in process optimization is a strategic move that delivers tangible returns. While the specific KPIs may differ between a chemical plant and a pharmaceutical facility, the core drivers are universal.
First, there's cost reduction and improved consistency. These are immediate effects of reducing process variability. By analyzing historical data, engineers can minimize waste, reduce off-spec products, and standardize operations for higher quality. For example, synthetic rubber producer Arlanxeo used self-service analytics to identify the ideal operational fingerprint for a "golden batch" of a complex product, a task that was too slow with previous tools. This allowed them to standardize production to their best-performing runs, significantly improving product consistency Read the use case. At its core, optimization directly impacts the bottom line by improving resource efficiency and quality.
Next is increased throughput. Optimization allows you to produce more with your existing assets. It means shorter cycle times, higher output, and the ability to meet growing customer demand without requiring massive capital expenditure. For instance, global chemical company Clariant reduced batch cycle times by 10%—the equivalent of one extra production cycle per day—by using self-service analytics to identify and resolve bottlenecks Read the case study.
Finally, optimization drives improved product quality and safety. Standardized, well-monitored processes reduce both human error and process variability. The result is a more consistent, high-quality product and fewer costly recalls. A well-understood and streamlined process is also inherently safer, reducing hazards and helping ensure you meet regulatory standards for compliance.
Foundational vs. Modern Approaches to Optimization
Effective optimization blends proven methodologies with modern technology. Understanding both is key to building a robust strategy.
Timeless Methodologies: Lean, Six Sigma, and TOC
These foundational production optimization techniques have been the bedrock of operational excellence for decades.
- Lean Manufacturing and Process Optimization: The core principle of Lean is the elimination of "Muda," or waste—any activity that consumes resources but adds no value. Lean provides a toolkit for identifying and removing this waste, including Value Stream Mapping to visualize workflows and Kaizen for continuous, incremental improvements.
- Six Sigma: Where Lean focuses on waste, Six Sigma targets quality. Its primary goal is to reduce process variation and eliminate defects. Using a statistical framework (DMAIC: Define, Measure, Analyze, Improve, Control), a Six Sigma operation aims for near-perfection.
- Theory of Constraints (TOC): TOC works on the principle that every system has at least one constraint (a bottleneck) that limits its performance. This technique focuses all improvement efforts on identifying and resolving that single biggest constraint before moving to the next one.
The Digital Shift: From Data Collection to Self-Service Analytics
While these methodologies provide the "what," modern digital tools provide the "how." Today’s plants are driven by data, but that data is often locked in separate systems. An engineer might need to pull time-series data from a historian, quality data from a LIMS system, and maintenance records from a CMMS. This complexity makes timely analysis difficult.
The real shift isn't just about collecting more data; it's about making it accessible. The move is toward process optimization software that enables self-service analytics. This empowers the process experts—the engineers on the floor—to analyze data directly without needing to wait for a central data science team. This democratization of data is what truly accelerates improvement.
The Right Tools for Modern Process Optimization
To effectively implement data-driven manufacturing, you need tools that can handle the complexity and scale of industrial operations.
Core Systems: MES, ERP, and Historians
- Manufacturing Execution Systems (MES): These are the digital command centers, providing real-time data on machine uptime, cycle times, and quality control.
- Enterprise Resource Planning (ERP): ERP software integrates manufacturing data with other business functions like inventory and supply chain for a holistic view.
- Historians: These databases are the primary repositories for vast amounts of time-series process data (e.g., temperature, pressure, flow rates) and are fundamental for historical analysis.
The Power of Self-Service Analytics Platforms
While the systems above are crucial for data storage, a dedicated self-service analytics platform sits on top of them to unlock insights. This type of process optimization software connects to your various data sources—historians, LIMS, maintenance logs—and provides a unified interface for analysis. Instead of manually exporting and combining data, engineers can use pattern recognition and search capabilities to instantly investigate process behavior across years of historical data.
Data-Driven Optimization in Practice
With the right tools, engineers can move from theory to application, tackling real-world production challenges.
Uncovering Insights with Root Cause Analysis
When a batch goes off-spec or a machine trips, the immediate question is "why?" A crucial capability of modern analytics is performing rapid root cause analysis. By using pattern-based search on historical time-series data, an engineer can quickly find previous instances of a similar deviation. Engineers at OCI Nitrogen, for instance, used this approach to finally find the root cause for carbon dioxide peaks in their washing column—a problem previous analysis projects failed to solve—achieving a first-year saving of $2.4 million Read the case study. This analytical power turns a multi-day investigation using spreadsheets into a task that can take minutes.
From Reactive to Proactive with Predictive Maintenance
Data-driven manufacturing is not just about understanding past events; it's about anticipating future ones. By analyzing historical performance data from assets like pumps, compressors, and heat exchangers, it's possible to identify patterns that precede failures. This enables predictive maintenance, allowing teams to service equipment before it breaks down, converting costly unplanned downtime into scheduled, efficient maintenance. This approach is central to improving asset reliability, a key component of Asset Performance Management (APM).
Manufacturing Process Optimization Examples
- Process Optimization in Pharmaceutical Manufacturing: The stakes in pharmaceutical production are incredibly high. For process optimization in pharmaceutical manufacturing, consistency and compliance are paramount. Companies use analytics to ensure batch uniformity and optimize yield. For example, by empowering its engineers with self-service analytics, specialty materials company Ashland was able to solve previously unsolvable production issues, increasing its on-target production of GMP products from 70% to 95% Read the case study.
- Production Optimization in Oil and Gas: In production optimization in oil and gas, asset reliability and safety are the top priorities. Preventing unplanned downtime of critical equipment is essential. Chrysaor, a North Sea oil and gas producer, used TrendMiner to monitor equipment performance and identify potential issues early, helping them achieve a 3% reduction in unscheduled production deferment and prevent costly shutdowns on their offshore platforms Read the case study.
A 5-Step Framework to Get Started
You don't need a massive budget to begin. Follow this simple framework.
- Map the Process: Choose one process you want to improve. Visually map every step, from raw material input to the finished product.
- Identify Bottlenecks & Waste: Use your map and data to find weak points. Where do materials pile up? Where are the longest cycle times? What steps add no value?
- Implement a Change: Apply a relevant technique. Start small. It could be adjusting a temperature setpoint or modifying a start-up procedure.
- Measure the Impact: Track the key performance indicators (KPIs) you want to improve. Did the cycle time decrease? Did the defect rate drop? Use data to judge success.
- Repeat & Refine: Optimization is a continuous culture, not a one-time project. Take what you learned, apply it to the next bottleneck, and empower your team to embrace continuous improvement.
Conclusion: Making Optimization a Continuous Practice
Manufacturing process optimization is an ongoing journey. It requires a combination of proven methodologies, the right digital tools, and a culture that is empowered to make data-driven decisions. By providing engineers and operational experts with direct access to process data and intuitive analytical tools, companies can unlock significant value, improving efficiency, quality, and profitability across the board.
Ready to see how a self-service analytics platform can accelerate your process optimization efforts?
Frequently Asked questions (FAQ)
Q: What are the most common process optimization techniques?
A: The most widely used techniques are Lean Manufacturing (focused on waste reduction), Six Sigma (focused on quality and defect reduction), and the Theory of Constraints (focused on eliminating bottlenecks).
Q: What is a simple example of manufacturing process optimization?
A: A classic example is using historical data to refine the start-up procedure for a reactor. By analyzing past start-ups, engineers can identify the optimal sequence and timing of valve openings and temperature ramps to reduce cycle time and ensure the first batch is on-spec, minimizing waste.
Q: How does software help optimize manufacturing?
A: Software like MES and historians collects critical data. Advanced analytics software, like TrendMiner, then connects to these sources, allowing engineers to visualize, search, and analyze years of data to quickly find root causes, monitor asset performance in real-time, and predict future issues before they occur.
Q: How important is employee buy-in for successful process optimization?
A: It is critical. Successful optimization is as much about creating a data-centric culture as it is about technology. When engineers, operators, and other process experts are empowered with accessible tools and training, they become the primary drivers of continuous improvement. The most effective initiatives foster collaboration and use the deep process knowledge of the on-site team to guide data analysis.
Q: How do I know where to start optimizing for the best return on investment (ROI)?
A: Start with the most significant and recurring pain points. This could be the process with the highest rate of quality defects, the asset that causes the most frequent downtime, or the production line with the most raw material waste. Using data to quantify the financial impact of these issues helps prioritize projects with the fastest and largest ROI. Analytics platforms can help quickly identify and validate these high-value opportunities.
This content was generated using AI. While TrendMiner strives for accuracy, we encourage readers to verify important information. We use AI-generated content to increase efficiencies and provide certain insights, but it may not reflect human expertise or opinions
Unlock Your Industrial Potential
Discover how our analytics solutions can transform your process industry operations today.
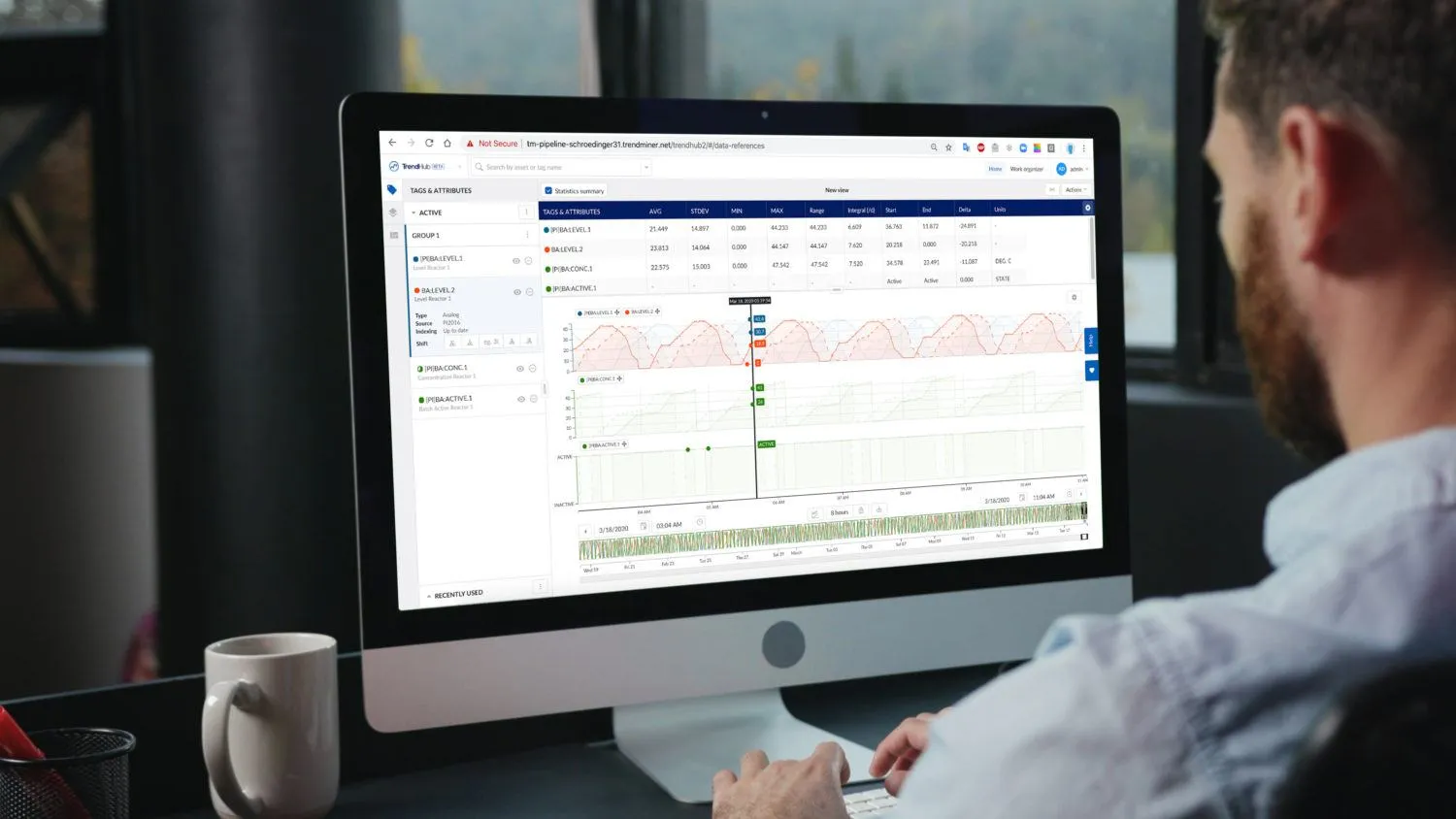
Subscribe to our newsletter
Stay up to date with our latest news and updates.
Latest Resources
Explore Our Newest Content to Maximize Your Operational Efficiency