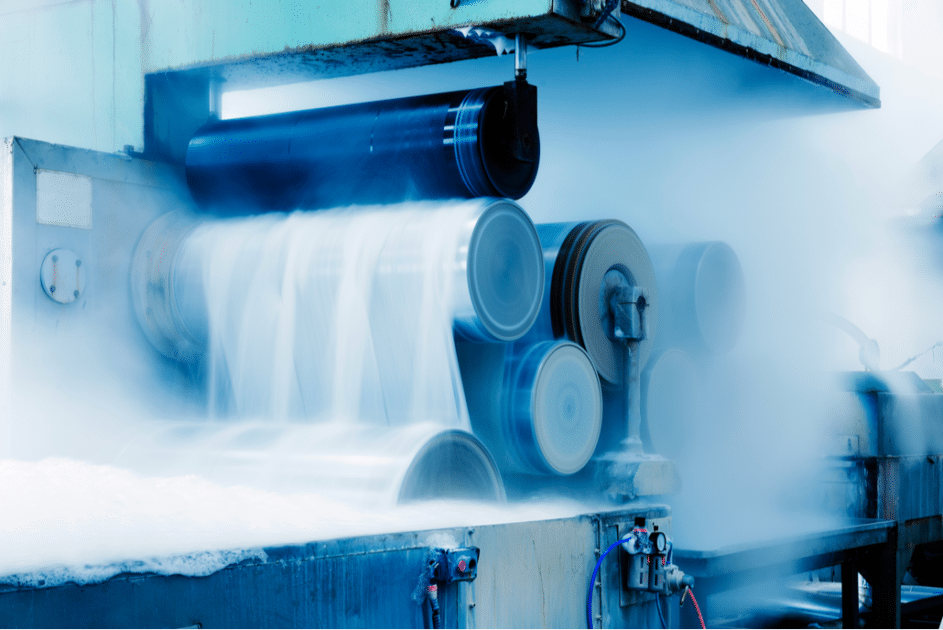
Situation
A plant in the chemical industry produces specialized fibers. In addition to their use in coatings and films, the resulting fibers are also used in the pharmaceutical space and are subject to strict quality constraints.
To produce fibers with the required and desired characteristics, the raw materials pass through a batch reactor. Each individual batch reaction has multiple stages, with each transition from one stage to the next being controlled very thoroughly. The final performance of the process is measured through metrics such as cycle time, end product quality, and yield.
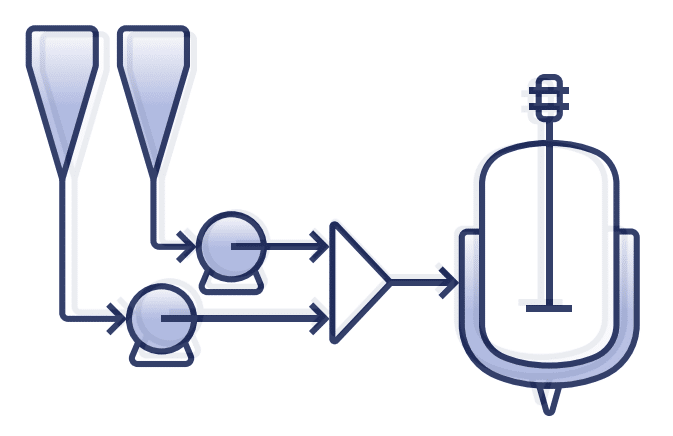
Problem
Gradually over time, the production of the fibers began to run suboptimally. Recent batches were taking longer to complete, which led to increased cycle times. Prior to using TrendMiner, the team attempted to identify the root cause of the cycle time delays, but they fell short using conventional tooling.
Solution
Comparing operation over time is a powerful workflow. TrendMiner was used to identify the 5 single best batches that were historically produced in the 5 years of data available in the historian as a comparison point for more recent production batches.
1. Preprocessing
To find the best batches in the wealth of data available, a good definition of what constitutes the golden standard is required. A preprocessing step was done to remove all batches that were irrelevant and should be disregarded for the next steps. In this case, these preprocessing steps were done:
– All batches of irrelevant product type were removed
– All batches that did not run to completion were removed
– All batches where the end quality did not meet the desired specification were removed
“Pre-processing can easily be accomplished in a matter of minutes by leveraging the search and filter functionalities of TrendMiner”
2. Golden Batch Identification
Once the pre-processing steps are completed, the dataset is reduced to batches that meet the minimum requirements. The next step is to further limit results to those batches that have the highest yield / shortest cycle time. This is easily accomplished by searching and sorting the results based on duration.
The 15 shortest batches were layered on top of each other, revealing the ideal golden batch profile in the process.
3. Comparison
The final step consisted of overlaying 10 recent batches on top of the golden batch profile created in the previous step. Immediately, a clustering became apparent. Midway through the full batch cycle, the recent batches significantly deviated from the historically best performers. Subject matter experts could immediately recognize that this was related to a change in the ramping up of a raw material feed. Material was being added at slower rate compared to historical golden batches.
An improvement project is now underway to re-tune the feed controller and map the feed ramp rate to match historical performance.
Results
The engineers had been faced with increased cycle times for quite a while, leading to tangible production and revenue losses. Leveraging the analytics capabilities of TrendMiner, a root cause was identified and a solution is being developed. The improvement potential is around 30 minutes on a 9 hour batch cycle, which corresponds to an estimated $1 million per year in business value.
4 Hours
The time it took the engineers to assess and solve the problem using TrendMiner, which would have otherwise taken a number of days.
~$1 million
Increase in business value due to production consistency and batch cycle time reduction.
Situation
A plant in the chemical industry produces specialized fibers. In addition to their use in coatings and films, the resulting fibers are also used in the pharmaceutical space and are subject to strict quality constraints.
To produce fibers with the required and desired characteristics, the raw materials pass through a batch reactor. Each individual batch reaction has multiple stages, with each transition from one stage to the next being controlled very thoroughly. The final performance of the process is measured through metrics such as cycle time, end product quality, and yield.
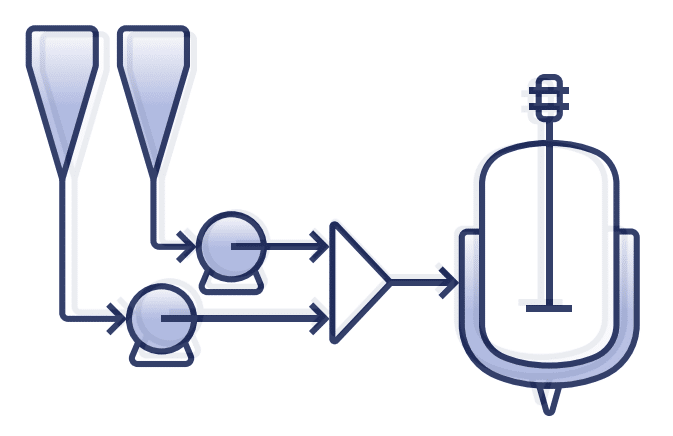
Problem
Gradually over time, the production of the fibers began to run suboptimally. Recent batches were taking longer to complete, which led to increased cycle times. Prior to using TrendMiner, the team attempted to identify the root cause of the cycle time delays, but they fell short using conventional tooling.
Solution
Comparing operation over time is a powerful workflow. TrendMiner was used to identify the 5 single best batches that were historically produced in the 5 years of data available in the historian as a comparison point for more recent production batches.
1. Preprocessing
To find the best batches in the wealth of data available, a good definition of what constitutes the golden standard is required. A preprocessing step was done to remove all batches that were irrelevant and should be disregarded for the next steps. In this case, these preprocessing steps were done:
– All batches of irrelevant product type were removed
– All batches that did not run to completion were removed
– All batches where the end quality did not meet the desired specification were removed
“Pre-processing can easily be accomplished in a matter of minutes by leveraging the search and filter functionalities of TrendMiner”
2. Golden Batch Identification
Once the pre-processing steps are completed, the dataset is reduced to batches that meet the minimum requirements. The next step is to further limit results to those batches that have the highest yield / shortest cycle time. This is easily accomplished by searching and sorting the results based on duration.
The 15 shortest batches were layered on top of each other, revealing the ideal golden batch profile in the process.
3. Comparison
The final step consisted of overlaying 10 recent batches on top of the golden batch profile created in the previous step. Immediately, a clustering became apparent. Midway through the full batch cycle, the recent batches significantly deviated from the historically best performers. Subject matter experts could immediately recognize that this was related to a change in the ramping up of a raw material feed. Material was being added at slower rate compared to historical golden batches.
An improvement project is now underway to re-tune the feed controller and map the feed ramp rate to match historical performance.
Results
The engineers had been faced with increased cycle times for quite a while, leading to tangible production and revenue losses. Leveraging the analytics capabilities of TrendMiner, a root cause was identified and a solution is being developed. The improvement potential is around 30 minutes on a 9 hour batch cycle, which corresponds to an estimated $1 million per year in business value.
4 Hours
The time it took the engineers to assess and solve the problem using TrendMiner, which would have otherwise taken a number of days.
~$1 million
Increase in business value due to production consistency and batch cycle time reduction.
Download now
Subscribe to our newsletter
Stay up to date with our latest news and updates.
Other Webinars on demand
Explore Our Newest Content to Maximize Your Operational Efficiency
Other Resources
Explore Our Newest Content to Maximize Your Operational Efficiency