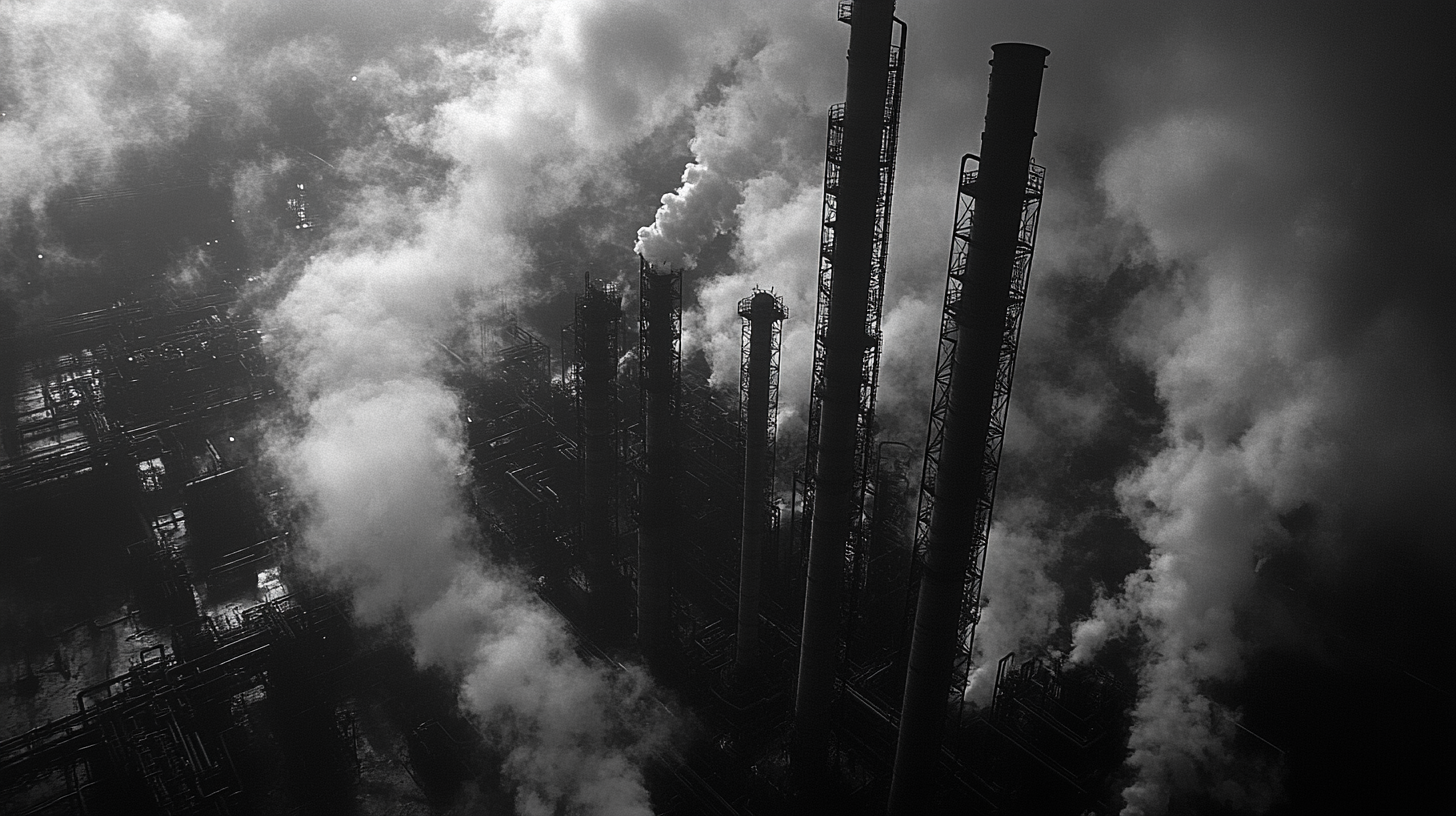
Situation
At this site, ammonia is produced. One of the steps in the production process is removing carbon dioxide from the product stream. It is important to remove as much carbon dioxide as possible, since it is an important factor in the inactivation of the catalyst. The removal of this product is done in a stripper or washing unit using a dedicated washing liquid.
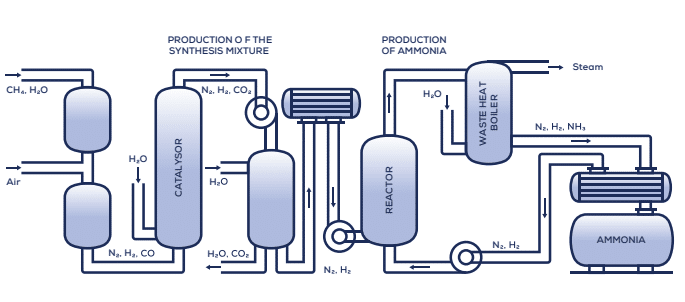
Problem
For a while, the carbon dioxide was not being washed out properly, and the plant was experiencing frequent carbon dioxide peaks. The occurrence of these peaks after the washing unit was unexpected behavior since the washing unit is designed to remove the CO2. Due to the complexity of the case, and their lack of sufficient tools, the team was previously unable to investigate the issue further
Solution
With the goal of reducing fines in mind, the team needed to pinpoint the cause of their high energy use. To do this, they used various TrendMiner functionalities to test their hypothesis and gain insight into the relationship between the flow rate and the power usage.
1. Impact Analysis
One of the key capabilities of TrendMiner is to compare different time periods to detect operational differences. If they could understand when and why some periods had more peaks than others, they could address the variability. In this case, the good periods had no peaks, and the throughput was kept constant.
“Getting the leads to solve a use case through influence factors in the traditional way was a tough task. With TrendMiner’s powerful influence factors capabilities we solved a chemical wash-out problem in only 2 hours.”
2. Comparison
Now that the engineers understood when the issues began, they could use TrendMiner to analyze those periods. The periods before May 2014 (good operation) and after May 2014 (bad operation) were compared to determine similar and deviating operating behaviour. This was done using layer comparison in TrendMiner.
When searching for the periods where carbon dioxide where carbon dioxide peaks appeared., TrendMiner indicated both numerically and visually that more peaks occurred after the installation of the packed washing column in May 2014. These signs of change in operation gave reason to compare on the period before the packed column was installed with the period after the packed column was installed.
The numerical comparison using the layer comparison functionality within TrendMiner showed that the washing fluid flow towards the column was higher due to the lower pressure before the methanator in the period after the new column was installed. Two new insights were gained from the layer comparison:
- The carbon dioxide peaks are not highly affected by the temperature of the process gas, but rather by the limited quantity of supplied washing fluid.
- Accordingly, the steam consumption needed to supply the heat to the process gas could be reduced in practice. The engineers concluded that lowering the pressure before the methanator would likely decrease the amount of carbon dioxide peaks, leading to a more stable operation.
Results
Faced with a complex case of carbon dioxide peaks, plant engineers were previously unable to identity and resolve the issue at hand. With a few simple steps in TrendMiner, however, the plant discovered that steam consumption could be decreased with approximately 165 tons per day. Additionally, due to the more stable operation, the daily ammonia production would increase by 50 tons. This corresponds to an estimated business value of $2.1 million/year.
1 Day
Spent by the engineers for assessing and solving the use case, which would have cost days without the use of TrendMiner
~$2.1 million/year
Increase in business value due to identification of the root cause for capacity loss.
Situation
At this site, ammonia is produced. One of the steps in the production process is removing carbon dioxide from the product stream. It is important to remove as much carbon dioxide as possible, since it is an important factor in the inactivation of the catalyst. The removal of this product is done in a stripper or washing unit using a dedicated washing liquid.
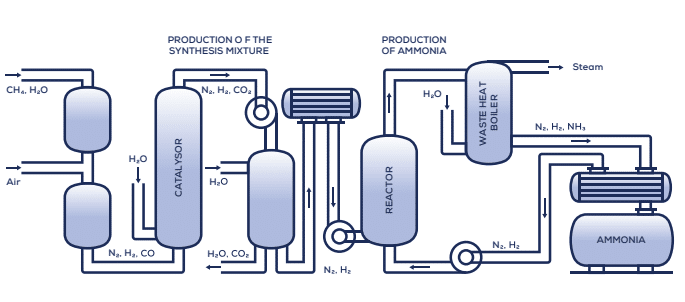
Problem
For a while, the carbon dioxide was not being washed out properly, and the plant was experiencing frequent carbon dioxide peaks. The occurrence of these peaks after the washing unit was unexpected behavior since the washing unit is designed to remove the CO2. Due to the complexity of the case, and their lack of sufficient tools, the team was previously unable to investigate the issue further
Solution
With the goal of reducing fines in mind, the team needed to pinpoint the cause of their high energy use. To do this, they used various TrendMiner functionalities to test their hypothesis and gain insight into the relationship between the flow rate and the power usage.
1. Impact Analysis
One of the key capabilities of TrendMiner is to compare different time periods to detect operational differences. If they could understand when and why some periods had more peaks than others, they could address the variability. In this case, the good periods had no peaks, and the throughput was kept constant.
“Getting the leads to solve a use case through influence factors in the traditional way was a tough task. With TrendMiner’s powerful influence factors capabilities we solved a chemical wash-out problem in only 2 hours.”
2. Comparison
Now that the engineers understood when the issues began, they could use TrendMiner to analyze those periods. The periods before May 2014 (good operation) and after May 2014 (bad operation) were compared to determine similar and deviating operating behaviour. This was done using layer comparison in TrendMiner.
When searching for the periods where carbon dioxide where carbon dioxide peaks appeared., TrendMiner indicated both numerically and visually that more peaks occurred after the installation of the packed washing column in May 2014. These signs of change in operation gave reason to compare on the period before the packed column was installed with the period after the packed column was installed.
The numerical comparison using the layer comparison functionality within TrendMiner showed that the washing fluid flow towards the column was higher due to the lower pressure before the methanator in the period after the new column was installed. Two new insights were gained from the layer comparison:
- The carbon dioxide peaks are not highly affected by the temperature of the process gas, but rather by the limited quantity of supplied washing fluid.
- Accordingly, the steam consumption needed to supply the heat to the process gas could be reduced in practice. The engineers concluded that lowering the pressure before the methanator would likely decrease the amount of carbon dioxide peaks, leading to a more stable operation.
Results
Faced with a complex case of carbon dioxide peaks, plant engineers were previously unable to identity and resolve the issue at hand. With a few simple steps in TrendMiner, however, the plant discovered that steam consumption could be decreased with approximately 165 tons per day. Additionally, due to the more stable operation, the daily ammonia production would increase by 50 tons. This corresponds to an estimated business value of $2.1 million/year.
1 Day
Spent by the engineers for assessing and solving the use case, which would have cost days without the use of TrendMiner
~$2.1 million/year
Increase in business value due to identification of the root cause for capacity loss.
Download now
Subscribe to our newsletter
Stay up to date with our latest news and updates.
Other Webinars on demand
Explore Our Newest Content to Maximize Your Operational Efficiency
Other Resources
Explore Our Newest Content to Maximize Your Operational Efficiency