Toray Improves Operational Efficiency with Self-Service Analytics
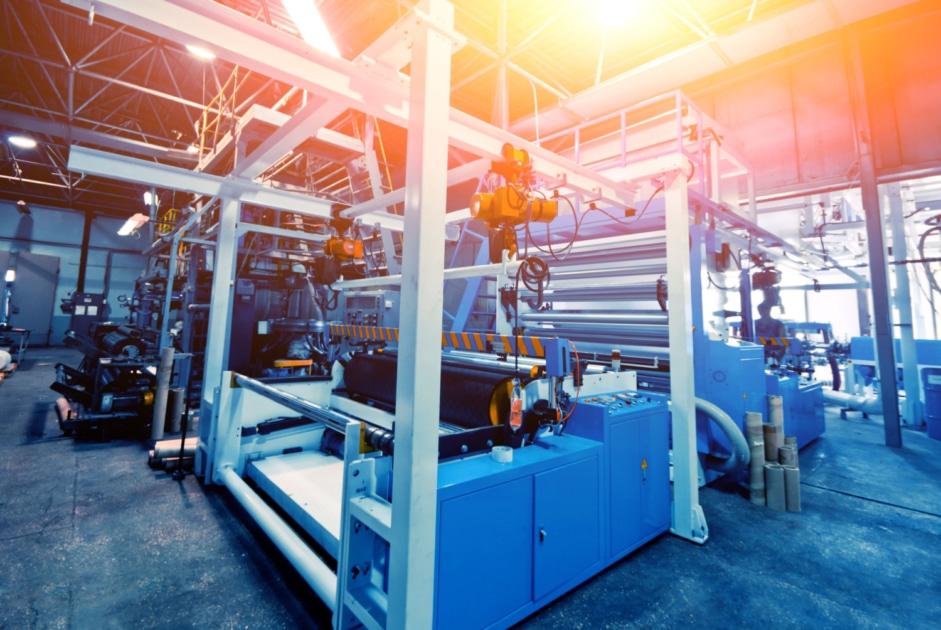
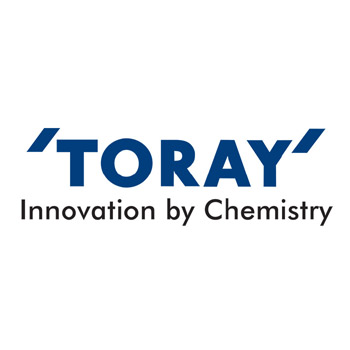
About Toray
Toray Industries Inc., founded in 1926, is a multinational corporation headquartered in Japan that specializes in industrial products centered on technologies in organic synthetic chemistry, polymer chemistry, and biochemistry. Its founding business areas were fibers and textiles, as well as plastics and chemicals. The company has also diversified into areas such as pharmaceuticals, biotechnology and R&D, medical products, reverse osmosis bigmembranes, electronics, IT-products, housing and engineering, and advanced composite materials.
In the advanced composite materials division, Toray is the leading global supplier. The company specializes in thermoset technology, thermoplastic composites, composite tooling, and ancillary products. They are used in aeronautical, automotive, and personal fitness equipment.
What they say
“I’ve seen the whole transition of where we started, using paper, and Excel, from where we were just typing numbers in to where we are now with TrendMiner. It’s been a fun ride. I really support it, management supports it, Toray Industries supports it, and they are really looking to use all the data we collected. One of the issues we had was we collected it all, but now what? And this is the ‘now what’ that I’ve found.” - Doug Bower, Principal Process Engineer, Toray Plastics
Their Digitalization Journey & Business Challenges
Toray wanted to get rid of paper. Engineers had to record equipment behavior manually, and then enter the information from that recording into spreadsheets to perform an analysis. Sometimes, this required taking measurements in extremely hot environments. Toray invested in sensors to send time-series data back to a historian.
The company then determined it needed an advanced analytics solution that would give its process engineers a way to understand the data, and it turned to TrendMiner as its partner. With TrendMiner, Toray was able to load its conditions for various processes as tags that would be available to everyone within the organization.
Further, it reduced the need for engineers to work in the hot and dangerous environments. Whenever a new measurement must be taken manually in the field, that measurement can be loaded as a new tag. The company has been able to move away from paper and get real-time measurements of process behavior without posing a risk to process engineers.
“Another key point is that we’ve had some monitoring capabilities added in TrendMiner that are separate from our control logic. We can establish where the value should be. If it’s outside of a given range, it sends an alert. And for the most part, we are getting value out our alarms. Anyone in manufacturing will tell you nuisance alarms are just nuisance. They don’t drive the productivity forward.” - Mike Malone, Principal Process Engineer, Toray Plastics
Solutions & Implementation
Toray stores its operational data in a Proficy historian. Aside from the historian’s own trend client, the only other analytics solution on the plant floor was Tibco Spotfire for more general analytics purposes. TrendMiner works in tandem with these systems and serves as the company’s primary analytics application for operations.
Use Case 1: Monitors & Alerts
The rate of raw material preparation had dropped below the production output rate, which caused undesirable process changes, line speed reductions, and production downtime. Raw material preparation is a two-step process that involves batch scaling from multiple silos and then vacuum drying.
In most cases, the batch preparation is automated, and the cycles repeat over and over. This continues until engineers realize the batches are taking longer than usual based on the demand. This usually means the dryer is a problem, but data indicated that even small recurring delays in the scaling process had compounding impact downstream.
The batches could not be dried in time to get to market. Using TrendMiner, engineers created a new conditional formula tag from stored time-series data to compare the scaling rate to the output rate. They then used this tag as the basis for establishing a monitor that alerted key personnel when the output rate starts exceeding the scaling rate.
Use Case 2: Quality Analysis of Raw Materials
The blending of material used in creating special films and coatings can affect the quality of the finished product, but also have an impact on process behavior. Material that has not been blended correctly can lead to higher production and energy costs, and an overall loss of process efficiency as well as a loss of production.
Engineers at Toray wanted to know if the quality of the material they were using had been changing over time. Using TrendMiner, process experts added the raw material blend data for each item in ContextHub. After synching data back for several years, they capture ongoing data through a live updating query. Process experts could use the information to quickly determine the material blend in the film production.
Benefits
Toray started seeing benefits on its first day of using TrendMiner. Process experts were able to move away from paper and spreadsheet analysis and begin making data-driven decisions. With TrendMiner, Toray engineers have found:
- A user-friendly, intuitive environment helps bring new users up to speed quickly
- An unrivalled ability to search and navigate through six years of process operational data
- The software maximizes productivity and improves the quality and safety of the operation
- Self-service monitors and alerts allow users to set up their own search criteria, activate a monitor trigger, and have email and text alerts sent to key stakeholders in a matter of minutes
- Engineers get a quick visualization of processes that allow them to make decisions without the help of a data scientist
- Root cause analysis and troubleshooting that would have taken many hours or even days to complete can be done in much less time, increasing overall efficiency and profitability
About Toray
Toray Industries Inc., founded in 1926, is a multinational corporation headquartered in Japan that specializes in industrial products centered on technologies in organic synthetic chemistry, polymer chemistry, and biochemistry. Its founding business areas were fibers and textiles, as well as plastics and chemicals. The company has also diversified into areas such as pharmaceuticals, biotechnology and R&D, medical products, reverse osmosis bigmembranes, electronics, IT-products, housing and engineering, and advanced composite materials.
In the advanced composite materials division, Toray is the leading global supplier. The company specializes in thermoset technology, thermoplastic composites, composite tooling, and ancillary products. They are used in aeronautical, automotive, and personal fitness equipment.
What they say
“I’ve seen the whole transition of where we started, using paper, and Excel, from where we were just typing numbers in to where we are now with TrendMiner. It’s been a fun ride. I really support it, management supports it, Toray Industries supports it, and they are really looking to use all the data we collected. One of the issues we had was we collected it all, but now what? And this is the ‘now what’ that I’ve found.” - Doug Bower, Principal Process Engineer, Toray Plastics
Their Digitalization Journey & Business Challenges
Toray wanted to get rid of paper. Engineers had to record equipment behavior manually, and then enter the information from that recording into spreadsheets to perform an analysis. Sometimes, this required taking measurements in extremely hot environments. Toray invested in sensors to send time-series data back to a historian.
The company then determined it needed an advanced analytics solution that would give its process engineers a way to understand the data, and it turned to TrendMiner as its partner. With TrendMiner, Toray was able to load its conditions for various processes as tags that would be available to everyone within the organization.
Further, it reduced the need for engineers to work in the hot and dangerous environments. Whenever a new measurement must be taken manually in the field, that measurement can be loaded as a new tag. The company has been able to move away from paper and get real-time measurements of process behavior without posing a risk to process engineers.
“Another key point is that we’ve had some monitoring capabilities added in TrendMiner that are separate from our control logic. We can establish where the value should be. If it’s outside of a given range, it sends an alert. And for the most part, we are getting value out our alarms. Anyone in manufacturing will tell you nuisance alarms are just nuisance. They don’t drive the productivity forward.” - Mike Malone, Principal Process Engineer, Toray Plastics
Solutions & Implementation
Toray stores its operational data in a Proficy historian. Aside from the historian’s own trend client, the only other analytics solution on the plant floor was Tibco Spotfire for more general analytics purposes. TrendMiner works in tandem with these systems and serves as the company’s primary analytics application for operations.
Use Case 1: Monitors & Alerts
The rate of raw material preparation had dropped below the production output rate, which caused undesirable process changes, line speed reductions, and production downtime. Raw material preparation is a two-step process that involves batch scaling from multiple silos and then vacuum drying.
In most cases, the batch preparation is automated, and the cycles repeat over and over. This continues until engineers realize the batches are taking longer than usual based on the demand. This usually means the dryer is a problem, but data indicated that even small recurring delays in the scaling process had compounding impact downstream.
The batches could not be dried in time to get to market. Using TrendMiner, engineers created a new conditional formula tag from stored time-series data to compare the scaling rate to the output rate. They then used this tag as the basis for establishing a monitor that alerted key personnel when the output rate starts exceeding the scaling rate.
Use Case 2: Quality Analysis of Raw Materials
The blending of material used in creating special films and coatings can affect the quality of the finished product, but also have an impact on process behavior. Material that has not been blended correctly can lead to higher production and energy costs, and an overall loss of process efficiency as well as a loss of production.
Engineers at Toray wanted to know if the quality of the material they were using had been changing over time. Using TrendMiner, process experts added the raw material blend data for each item in ContextHub. After synching data back for several years, they capture ongoing data through a live updating query. Process experts could use the information to quickly determine the material blend in the film production.
Benefits
Toray started seeing benefits on its first day of using TrendMiner. Process experts were able to move away from paper and spreadsheet analysis and begin making data-driven decisions. With TrendMiner, Toray engineers have found:
- A user-friendly, intuitive environment helps bring new users up to speed quickly
- An unrivalled ability to search and navigate through six years of process operational data
- The software maximizes productivity and improves the quality and safety of the operation
- Self-service monitors and alerts allow users to set up their own search criteria, activate a monitor trigger, and have email and text alerts sent to key stakeholders in a matter of minutes
- Engineers get a quick visualization of processes that allow them to make decisions without the help of a data scientist
- Root cause analysis and troubleshooting that would have taken many hours or even days to complete can be done in much less time, increasing overall efficiency and profitability
Download now
Subscribe to our newsletter
Stay up to date with our latest news and updates.
Other Webinars on demand
Explore Our Newest Content to Maximize Your Operational Efficiency
Other Resources
Explore Our Newest Content to Maximize Your Operational Efficiency