The Ultimate Guide to Process Safety Management
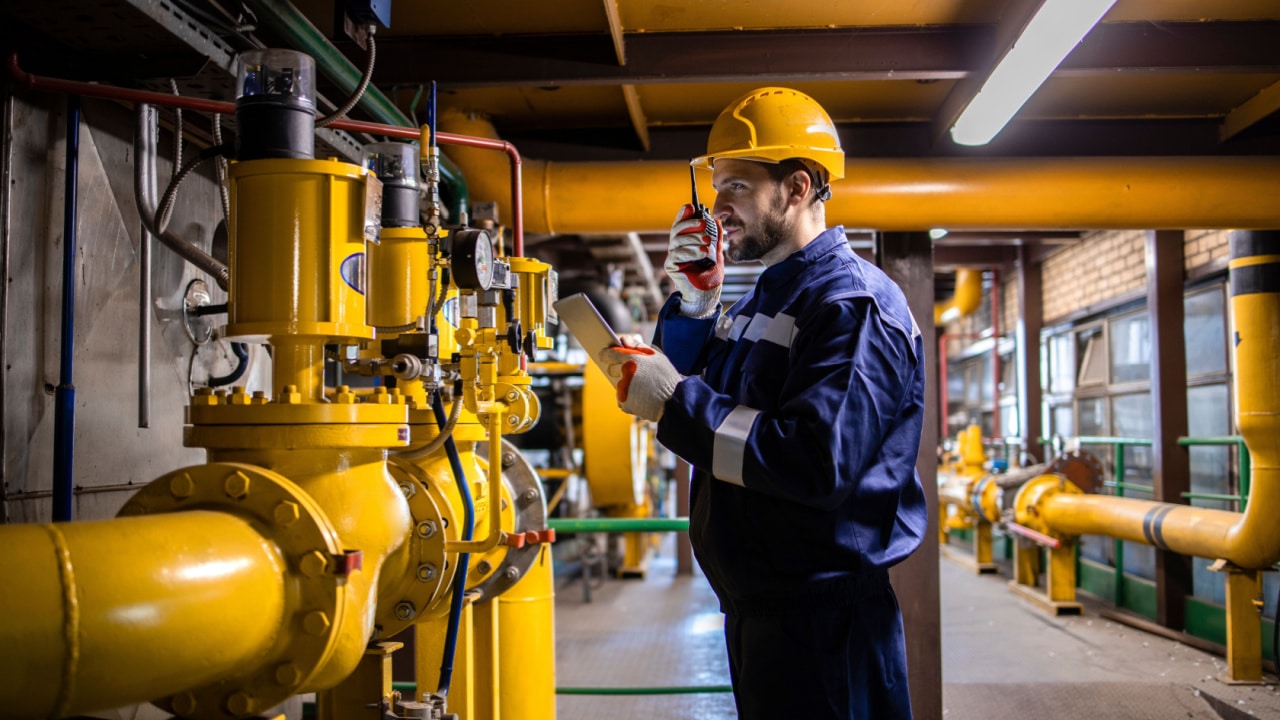
Table of Contents
Introduction
Process Safety Management (PSM) is a comprehensive framework that aims to prevent or mitigate major incidents in industries handling hazardous chemicals or operations involving potential safety hazards. It focuses on identifying, evaluating, and managing the risks associated with these processes to protect workers, communities, and the environment.
The objective of PSM is to minimize the likelihood of catastrophic incidents such as explosions, fires, chemical releases, or other accidents that could result in severe injuries, fatalities, or significant property damage.
PSM involves a systematic approach with several key elements. These include:
- Development of process safety information, such as process descriptions, equipment specifications, and hazard analyses.
- Establishment of comprehensive procedures and practices for maintaining and operating equipment safely.
- Thorough employee training programs on process hazards and safety protocols.
- Identification and assessment of potential hazards through methods like process hazard analysis (PHA) and hazard and operability studies (HAZOP).
- Implementation of appropriate safeguards, such as safety interlocks, emergency shutdown systems, and protective equipment.
- Effective management of change (MOC) to evaluate and communicate any modifications to the process, equipment, or procedures.
- Regular auditing, inspection, incident investigation, and near-miss reporting to identify deviations and implement corrective actions.
PSM is an ongoing commitment to continuously improve safety performance. It is regulated by government agencies in many countries, and non-compliance can result in penalties and legal consequences.
Overall, PSM is a systematic and comprehensive approach that ensures the safe operation of processes, prevents major accidents, and protects the well-being of employees, the public, and the environment.
The Importance of PSM in Various Industries
Process safety management (PSM) plays a critical role in various industries by ensuring the safety and well-being of workers, protecting the environment, and preventing major accidents. PSM encompasses the appropriate design, operation, maintenance, and modification of facilities to manage the integrity and safety of hazardous processes. Here, we explore the importance of PSM in different industries and why it is crucial for their sustainability and success.
- Chemical Industry: PSM helps mitigate risks associated with highly hazardous materials and processes, reducing the likelihood of catastrophic incidents such as explosions, fires, or chemical releases. It emphasizes hazard identification and control, effective training, process design reviews, and incident investigation techniques.
- Oil and Gas Industry: Proper implementation of PSM supports effective risk management throughout the entire lifecycle of operations, reducing the risks of fires, explosions, well blowouts, and oil spills.
- Pharmaceutical Industry: PSM prevents accidents that could lead to chemical exposures or contamination, safeguarding both workers and pharmaceutical products. It ensures appropriate measures for handling hazardous waste, protecting air quality, and adhering to regulatory requirements.
- Food & Beverage: PSM relates to traceability, food processing and clean production to avoid contamination and impact on human health for which adherence and compliance to regulatory requirements is crucial.
- Mining Industry: PSM helps identify and manage risks associated with extraction, processing, and transportation of minerals, reducing the occurrence of accidents and injuries.
- Manufacturing Industry: Effective PSM programs contribute to the safe handling and processing of materials, minimizing incidents and fostering a safe working environment.
Overall, PSM is essential for minimizing the risk of major accidents, protecting workers’ health and safety, preserving the environment, enhancing reputation, and ensuring long-term sustainability in various industries.
Regulatory Bodies
The Occupational Safety and Health Administration (OSHA) is a key regulatory body in the United States. OSHA enforces safety and health regulations to ensure the well-being and protection of workers. Its Process Safety Management (PSM) standard, found in Title 29 Code of Federal Regulations (CFR) Part 1910.119, establishes requirements for managing hazardous chemicals and preventing major chemical accidents.
Other regulatory bodies that may be involved in process safety management, depending on the industry or region, include:
- Environmental Protection Agency (EPA): Regulates and enforces environmental laws related to chemical safety and hazardous waste management.
- Chemical Safety Board (CSB): Investigates chemical accidents and makes recommendations to prevent future incidents.
- European Union (EU) Agencies: Responsible for regulating process safety management in the European Union.
- Food & Drug Administration (FDA): Responsible for protecting the public health by ensuring the safety, efficacy, and security of human and veterinary drugs, biological products, and medical devices; and by ensuring the safety of food supply, cosmetics, and products that emit radiation.
Specific regulatory bodies involved in process safety management can vary based on the country, industry, and nature of activities.
The Relevance of PSM in the Context of Advanced Analytics and Real-Time Monitoring
Process Safety Management (PSM) focuses on preventing and mitigating potential accidents associated with highly hazardous chemicals in the workplace. Advanced analytics and real-time monitoring are valuable tools for enhancing PSM, improving safety performance, and increasing operational efficiency. Here are several reasons why PSM and advanced analytics/real-time monitoring are highly relevant to each other:
- Early detection of abnormalities: Real-time monitoring systems allow continuous monitoring of process variables, enabling quick detection of deviations from normal operating conditions.
- Predictive maintenance: Advanced analytics help predict equipment failures, optimizing maintenance schedules and reducing the risk of accidents.
- Process optimization: Analyzing vast amounts of data through advanced analytics identifies patterns and trends that can optimize processes and improve safety.
- Improved incident response: Real-time monitoring systems provide instant alerts when abnormal conditions are detected, facilitating quick response and corrective actions.
- Compliance and regulatory requirements: Advanced analytics and real-time monitoring systems help organizations meet safety regulations and monitor safety performance.
Advanced analytics and real-time monitoring are highly relevant to Process Safety Management. Integrating these technologies into PSM programs enhances risk management strategies, improves incident response, optimizes processes, and ensures compliance with safety regulations. This comprehensive approach fosters safer operations, protects personnel and assets, and contributes to the well-being of organizations and stakeholders.
The Evolution of Process Safety Management
The Historical Context and Need for PSM
Industrial accidents involving hazardous chemicals have been occurring for centuries, but it was not until the 20th century that more systematic approaches to safety management began to emerge. Before the development of Process Safety Management (PSM), safety management often focused on personal protective equipment and responding to accidents rather than prevention.
In the early 20th century, several major incidents brought attention to the devastating consequences of chemical accidents and the need for better safety management practices.
- Texas City disaster (1947): A ship carrying ammonium nitrate exploded in Texas City, resulting in the death of nearly 600 people. This incident highlighted the safety risks associated with the storage and handling of hazardous chemicals.
- Seveso disaster (1976): An explosion at a chemical plant in Seveso, Italy, released a toxic cloud and caused widespread environmental contamination and health effects for the local population. This incident emphasized the need for better process safety management practices to prevent catastrophic accidents.
Key Incidents Leading to the Development of PSM Standards
Several major incidents further emphasized the importance of effective process safety management and led to the development of PSM standards and guidelines:
- Flixborough Disaster (1974): An explosion at a chemical plant in Flixborough, UK, caused by a ruptured cyclohexane reactor, resulted in the release of a toxic cloud and the death of 28 people. This incident highlighted the need for robust management systems and better process design to prevent accidents.
- Three Mile Island Accident (1979): Although primarily a nuclear incident, the partial meltdown at the Three Mile Island nuclear power plant in the USA drew attention to the importance of effective operating procedures, operator training, and emergency planning. It emphasized the need for a comprehensive approach to process safety management and learning from near-miss incidents.
- Bhopal Gas Tragedy (1984): The Bhopal gas tragedy in India resulted in the release of toxic gases from a pesticide plant, causing thousands of immediate deaths and long-term health effects for thousands more. The incident raised global awareness about the need for strong process safety programs and regulations to prevent such disasters.
These incidents, along with others not mentioned, led to increased recognition of the need for a comprehensive approach to process safety management. As a result, organizations, regulatory bodies, and industry associations began developing standards and guidelines to systematically manage the hazards of highly hazardous chemicals. This eventually led to the development of various PSM standards, such as the OSHA Process Safety Management Standard in the United States and the CCPS Guidelines for Risk-Based Process Safety globally.
Today, PSM is a fundamental part of managing the risks associated with operating chemical processes. It helps organizations ensure the safety of their workers, protect the environment, and prevent major accidents by implementing robust process safety programs, conducting hazard analyses, establishing clear written procedures, and promoting continuous improvement in safety performance.
Regulatory Framework and International Standards
OSHA is the primary agency responsible for enforcing workplace health and safety regulations in the United States. They set and enforce standards, conduct inspections, provide training, and promote cooperation with employers to improve safety. The specific regulations for Process Safety Management (PSM) can be found in Title 29 of the Code of Federal Regulations (CFR), Section 1910.119.
The PSM standard requires employers to implement safety measures to reduce risks associated with hazardous chemicals. This includes hazard analysis, operating procedures, employee training, safety reviews, and mechanical integrity programs. OSHA conducts inspections and penalties for noncompliance to ensure adherence to regulations and protect workers and the public.
To reduce regulatory burdens on small businesses, the Small Business Regulatory Enforcement Fairness Act (SBREFA) requires agencies like OSHA to consider the impact of regulations on these entities. OSHA has established the SBREFA panel, consisting of industry representatives, small businesses, and the agency, to review and provide input on draft regulations. They also offer a Small Business Assistance Program to help small businesses understand and comply with PSM regulations.
Internationally, various standards and bodies contribute to process safety. The International Labour Organization (ILO) sets global standards for occupational safety and health, promoting process safety management. The American Institute of Chemical Engineers (AIChE) develops technical guidelines and industry best practices for process safety. The International Organization for Standardization (ISO) publishes standards for safety and risk management, including ISO 45001 for occupational health and safety management systems.
OSHA considers these international standards and guidelines when developing or updating PSM regulations, ensuring alignment with best practices while accommodating national requirements. These efforts promote global process safety and a consistent understanding of PSM principles across nations.
Core Elements of PSM
The 14 core elements of Process Safety Management (PSM) are designed to enhance workplace safety. They are:
- Employee Involvement: Engage employees in the creation and upkeep of PSM programs.
- Process Safety Information (PSI): Maintain accurate data on chemical hazards and equipment.
- Process Hazard Analysis (PHA): Use methods like HAZOP to identify process risks.
- Operating Procedures: Establish guidelines for safely handling Highly Hazardous Chemicals (HHCs).
- Training: Equip employees with the skills and knowledge for safe process handling.
- Contractor Safety: Ensure contractors comply with the company’s safety program.
- Pre-Startup Safety Review (PSSR): Validate safety measures before starting new processes.
- Mechanical Integrity: Regularly inspect and maintain process equipment.
- Hot Work Permits: Issue permits for tasks involving open flames or heat.
- Management of Change (MOC): Safely manage alterations to process or technology.
- Incident Investigation: Analyze incidents to improve safety protocols.
- Emergency Planning: Prepare for emergencies with robust plans and procedures.
- Compliance Audits: Regularly evaluate the effectiveness of PSM programs.
- Trade Secrets: Balance safety needs with information confidentiality.
Employing these elements cohesively enhances workplace safety by mitigating risks related to HHCs.
The Role of Technology in PSM
Advanced analytics, real-time monitoring, and predictive insights are pivotal in elevating Process Safety Management (PSM).
Advanced (Industrial) Analytics: This technology scrutinizes both historical and real-time data to identify safety patterns and risks, enabling companies to act proactively. For example, data on past incidents can highlight early warning signs to prevent future accidents.
Real-time Monitoring: These systems continually capture data from facility sensors, tracking variables like temperature and pressure. Any irregularities trigger immediate alerts, facilitating quick, informed decisions.
Predictive Insights: By applying machine learning to historical data, this technology forecasts safety risks and guides preemptive action. It helps strategically allocate resources to high-risk areas and optimize maintenance schedules.
In summary, these technologies enable data-driven, proactive safety management. They not only mitigate risks but also improve overall operational safety, benefitting workers, the environment, and the community.
Implementation Guide
Streamlined steps to enact Process Safety Management (PSM):
- Leadership Commitment: Secure senior management’s buy-in, define safety objectives, and allocate resources for PSM.
- Assemble Team: Form a cross-functional team to oversee PSM, coordinating all related tasks.
- Hazard Analysis: Conduct a Process Hazard Analysis (PHA) using methods like HAZOP or FMEA to identify control measures.
- Operating Procedures: Draft clear Standard Operating Procedures (SOPs) for all vital processes, including emergency response.
- Employee Training: Educate all involved staff in hazard awareness, safe practices, and the significance of PSM.
- Manage Change: Establish a robust Management of Change (MOC) process to assess the safety impact of any alterations.
- Incident Learning: Foster continuous improvement by thoroughly investigating incidents and sharing lessons learned.
- Audits & Metrics: Regularly audit PSM compliance and set key performance indicators to track safety improvements.
Best Practices & Common Pitfalls
Best Practices:
- Involve all employees in PSM and maintain open communication.
- Create a safety-first culture.
- Utilize PSM software to streamline processes.
- Benchmark against industry leaders for continuous improvement.
Common Pitfalls:
- Inadequate management buy-in.
- Insufficient staff training and engagement.
- Skimping on hazard analysis.
- Outdated or incomplete SOPs.
- Poor change management.
Case Studies:
- BP Texas City: After the 2005 explosion, BP overhauled its PSM, leading to improved safety metrics and culture.
- Turin Chemical Plant: After several incidents, a thorough PSM overhaul led to fewer accidents, improved safety metrics, and regulatory compliance.
These cases underline the transformative power of effective PSM—enhancing workplace safety and overall performance.
Industry-Specific Applications
Manufacturing
- PSM Focus: Control measures, equipment maintenance, and documented operating procedures.
- Unique Needs: Broad range of hazardous materials and machinery requiring vigilant monitoring.
Chemicals
- PSM Focus: Hazard identification, risk assessment, and process design.
- Unique Needs: High-risk substances, rigorous inspections, and emergency plans.
Oil & Gas
- PSM Focus: Hazard prevention via engineering controls and solid operating procedures.
- Unique Needs: Complex processes, high temperatures/pressures, and emergency training.
Pharmaceuticals
- PSM Focus: Hazard assessment, equipment/process design, and robust safeguards.
- Unique Needs: High standards for product quality and specialized emergency response plans.
Tailoring Strategy: While PSM core principles remain constant, each industry must adapt them to fit their unique risk profiles, processes, and standards.
Conclusion: PSM is indispensable across sectors for safeguarding personnel and communities. Customizing PSM strategies allows industries to manage their unique risks effectively.
The Business Case for PSM
ROI Considerations
- Scope: Quantifies the financial gains from safety initiatives.
- Key Factors: Lower insurance costs, fewer penalties, improved productivity, and brand enhancement.
Cost-Benefit Analysis
- Scope: Assesses the financial viability of PSM initiatives.
- Key Factors: Risk reduction, potential accident costs, and operational expenses.
Risk Mitigation Strategies
- Process Design: Opt for inherently safer technologies and build in safeguards.
- Safety Systems: Employ alarms and safety shutdowns for immediate incident response.
- Training & Competency: Equip staff with crucial process knowledge and safety procedures.
- Maintenance & Inspection: Regular equipment checks to preemptively address issues.
- Management of Change: Formal processes for assessing and handling any process changes.
- Emergency Response: Detailed planning, regular drills, and a clear communication chain.
Balancing ROI considerations, cost-benefit analyses, and risk mitigation not only fortifies safety but also fortifies compliance and financial stability.
A platform such as TrendMiner, can seamlessly integrate into any PSM strategy across these sectors. Its real-time monitoring and predictive insights can be a game-changer, especially for industries dealing with complex processes and high-risk scenarios. By contributing to more informed decision-making and predictive maintenance, TrendMiner adds an additional layer of safety and operational excellence, making it easier to realize a quick ROI.
Future Trends in PSM
The advent of AI in Manufacturing Process Safety is ushering in a transformative era for Process Safety Management (PSM). This section sheds light on how the integration of Artificial Intelligence (AI) and Machine Learning (ML) is reshaping key aspects of PSM, including risk assessment, incident prevention, and emergency response. By harnessing data-driven models and real-time monitoring, AI and ML are elevating safety standards, enabling proactive risk mitigation, and optimizing emergency strategies. This technological evolution not only boosts current PSM efficiency but also gears it for future adaptability, marking a significant shift towards a more dynamic and responsive approach in manufacturing safety.
Adoption of AI & ML
Scope: Enhances multiple PSM components including risk assessment, incident prevention, and emergency response.
Risk Assessment
- AI/ML Impact: Data-driven models utilizing historical incident reports, sensor data, and maintenance logs to facilitate dynamic and accurate risk evaluations.
- Key Benefits: Proactive risk mitigation and accident prevention.
Incident Prevention
- AI/ML Impact: Real-time monitoring of operational systems to identify abnormal behaviors, potential failures, and human errors.
- Key Benefits: Early warning systems and proactive corrective actions.
Emergency Response
- AI/ML Impact: AI-driven decision support for rapid situational analysis and strategy recommendations during emergencies.
- Key Benefits: Optimized emergency responses and reduced incident impact.
Scalability & Future-Proofing
- AI/ML Impact: Automation of repetitive tasks and efficient data processing, enabling scalability.
- Key Benefits: Adaptable to industry evolutions, continually improving accuracy over time based on new data.
AI and ML are becoming pivotal in elevating PSM’s effectiveness. They enhance risk assessment accuracy, optimize incident prevention, and refine emergency responses. The innate scalability and future-proofing features of AI and ML ensure that PSM systems remain robust and adaptable.
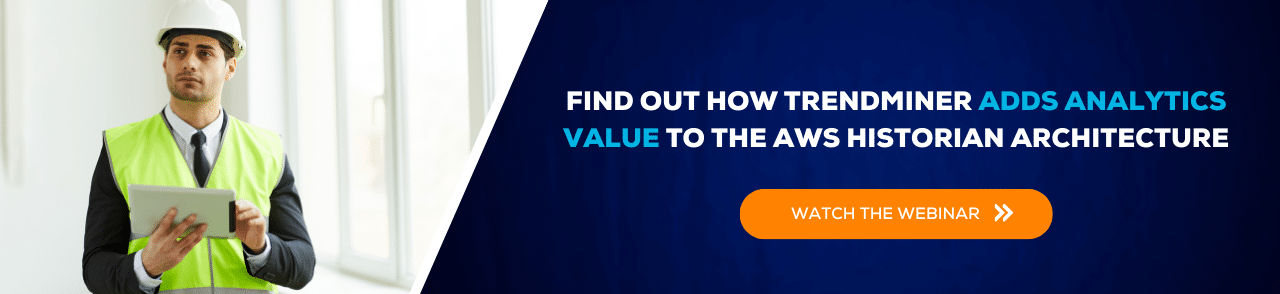
Conclusion:
Process Safety Management (PSM) is a critical component of managing the risks associated with operating chemical processes. It ensures the safety of workers, protects the environment, and prevents major accidents by implementing robust process safety programs, conducting hazard analyses, establishing clear written procedures, and promoting continuous improvement in safety performance.
The adoption of advanced technologies, such as artificial intelligence (AI) and machine learning (ML), is revolutionizing PSM by enhancing risk assessment accuracy, optimizing incident prevention, and refining emergency responses. These technologies offer scalability and future-proofing features, allowing PSM systems to remain robust and adaptable.
Historical incidents, such as the Texas City disaster and the Bhopal gas tragedy, have highlighted the need for effective process safety management practices and led to the development of PSM standards and guidelines [4]. Regulatory frameworks, such as the OSHA Process Safety Management Standard, play a crucial role in enforcing safety measures and protecting workers and the public.
To successfully implement PSM, organizations should focus on key elements such as hazard analysis, operating procedures, employee training, safety reviews, and mechanical integrity programs. It is also important to address common pitfalls, such as inadequate management buy-in and insufficient staff training and engagement.
By balancing ROI considerations, cost-benefit analyses, and risk mitigation, organizations can fortify safety, compliance, and financial stability. Advanced analytics and real-time monitoring systems play a vital role in PSM by enabling early detection of abnormalities, predictive maintenance, process optimization, improved incident response, and compliance with regulatory requirements.
Incorporating TrendMiner, a real-time monitoring and predictive insights platform, into PSM strategies can be a game-changer for industries dealing with complex processes and high-risk scenarios. It adds an additional layer of safety and operational excellence, facilitating more informed decision-making and predictive maintenance, ultimately leading to a quick return on investment.
Overall, PSM is an essential framework for ensuring the safe operation of chemical processes. By embracing technological advancements, adhering to regulatory standards, and implementing best practices, organizations can foster safer operations, protect personnel and assets, and contribute to the well-being of all stakeholders involved.
Additional Resources
1. Tools:
Hazard and Operability Study (HAZOP): HAZOP is a systematic process for identifying potential hazards and operability issues in a system. It involves a team of experts analyzing the design and operation of a process to identify deviations from normal operations that could result in risks.
Failure Modes and Effects Analysis (FMEA): FMEA is a structured approach to identify and prioritize potential failure modes in a system, process, or product. It assesses the effects of these failures and helps develop strategies to mitigate them.
Bowtie Analysis: Bowtie analysis is a visual tool that helps in understanding and communicating the causes, consequences, and safeguards related to potential hazards. It creates a clear and intuitive overview of risk scenarios.
Layers of Protection Analysis (LOPA): LOPA is used to estimate the likelihood and consequences of various process incidents. It identifies layers of protection and their effectiveness in preventing or mitigating incidents.
Safety Instrumented Systems (SIS): SIS involves using instrumentation and control systems to automatically respond to hazardous situations, often using Safety Integrity Levels (SILs) to quantify their reliability.
Root Cause Analysis (RCA): RCA is a method for identifying the underlying causes of incidents or accidents. It helps in understanding why a particular event occurred and how to prevent its recurrence.
Process Hazard Analysis (PHA): PHA encompasses various techniques, including HAZOP and FMEA, to systematically evaluate potential hazards in a process.
Quantitative Risk Assessment (QRA): QRA involves using mathematical models to quantify the risks associated with a process. It considers factors like probability, consequence, and exposure to assess risk levels.
Process Safety Management Systems (PSM): PSM is an overarching framework that includes policies, procedures, and practices to manage process safety effectively. It often includes elements like management of change, training, and incident investigation.
Safety Data Sheets (SDS): While not a tool per se, SDS provides essential information about hazardous chemicals, including their properties, handling, and emergency response measures. Digital tools and databases can help manage and access SDS efficiently.
These are just a few examples of process safety management tools and methodologies used to ensure the safety and integrity of various industrial processes. If you have specific questions or need more details about any of these tools, feel free to ask.
2. Further Reading:
– “Guidelines for Risk Based Process Safety” by American Institute of Chemical Engineers (AIChE): This comprehensive guide provides a systematic approach to managing process safety risks based on industry best practices, helping organizations develop and implement effective process safety management systems.
– “Management of Process Hazards” by Frank Mannan: This book offers practical insights into managing process hazards, covering topics such as hazard identification, risk assessment, safety audits, emergency planning, and process safety performance measurement.
– “Guidelines for Process Safety Documentation” by Center for Chemical Process Safety (CCPS): This resource provides helpful guidance on developing various process safety management documents, including guidelines for process safety information, process safety hazard analysis, and operating procedures. It offers valuable templates and examples for creating effective documentation.
– “Chemical Process Safety: Fundamentals with Applications” by Daniel A. Crowl and Joseph F. Louvar: This textbook provides a comprehensive introduction to chemical process safety concepts, including risk assessment, hazard analysis techniques, and process safety management principles. It is a valuable resource for gaining a deeper understanding of process safety management practices.
FAQs
1. What is Process Safety Management (PSM)?
Process Safety Management (PSM) is a systematic approach to managing the risks associated with processes involving hazardous chemicals, with the goal of preventing accidents and incidents that could have catastrophic outcomes. PSM aims to ensure that proper safety protocols, procedures, and controls are implemented and maintained throughout the entire lifecycle of a process.
2. Why is PSM important?
PSM is crucial because it helps prevent catastrophic incidents, such as explosions, fires, toxic releases, and other accidents that can result in severe injuries, fatalities, and significant damage to facilities and the environment. By implementing and following PSM guidelines, companies can enhance operational safety, protect their employees and communities, preserve the environment, and maintain sustainable business operations.
3. What are the key elements of PSM?
The key elements of Process Safety Management typically include:
– Process safety information: Detailed information about the hazards, equipment, and materials involved in the process.
– Process hazard analysis: A systematic assessment of potential hazards and risks associated with the process.
– Operating procedures: Clearly defined and written instructions for safe and proper operation of the process.
– Employee training: Ongoing training to ensure employees understand the hazards, safety procedures, and emergency response plans.
– Mechanical integrity: Procedures to ensure that equipment is properly designed, installed, operated, and maintained to prevent failures.
– Management of change: A process to assess and manage potential safety risks associated with any changes to the equipment, materials, or procedures.
– Pre-startup safety review: A thorough check of newly installed or modified equipment and procedures to identify and address potential safety concerns before starting operations.
– Emergency planning and response: Procedures and training for responding to emergencies, including evacuation plans, alarm systems, and communication protocols.
– Compliance audits: Regular evaluations to ensure that all aspects of the PSM program are being followed and any deficiencies are addressed.
– Incident investigation: A thorough investigation process to identify the root causes of incidents and take measures to prevent similar occurrences in the future.
4. Who is responsible for implementing PSM?
The responsibility for implementing PSM lies with the company or facility that handles the hazardous processes. Senior management plays a crucial role in ensuring the commitment, resources, and support necessary to establish and maintain a robust PSM program. However, every employee has a role to play in adhering to and promoting safe practices and reporting any potential hazards or concerns.
5. Are there regulatory requirements for PSM?
Yes, in many countries, there are regulatory requirements governing the implementation of PSM. For example, in the United States, the Occupational Safety and Health Administration (OSHA) has established the Process Safety Management standard (29 CFR 1910.119), which outlines specific requirements for managing hazardous processes. Other countries may have their own regulations or guidelines tailored to their local context.
6. How does PSM help prevent accidents?
PSM helps prevent accidents by implementing systematic approaches to identify and control hazards. By thoroughly understanding the processes, their risks, and the necessary safety measures, companies can implement controls and protocols to eliminate or reduce the potential for accidents. Additionally, training employees on proper procedures, maintaining equipment integrity, and conducting regular audits and reviews enhance safety and prevent incidents from occurring or escalating.
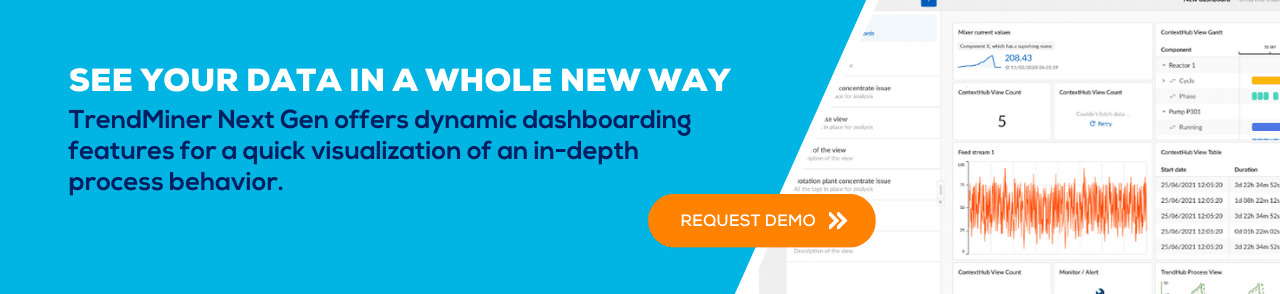
This content was generated using AI. While TrendMiner strives for accuracy, we encourage readers to verify important information. We use AI-generated content to increase efficiencies and provide certain insights, but it may not reflect human expertise or opinions
Unlock Your Industrial Potential
Discover how our analytics solutions can transform your process industry operations today.
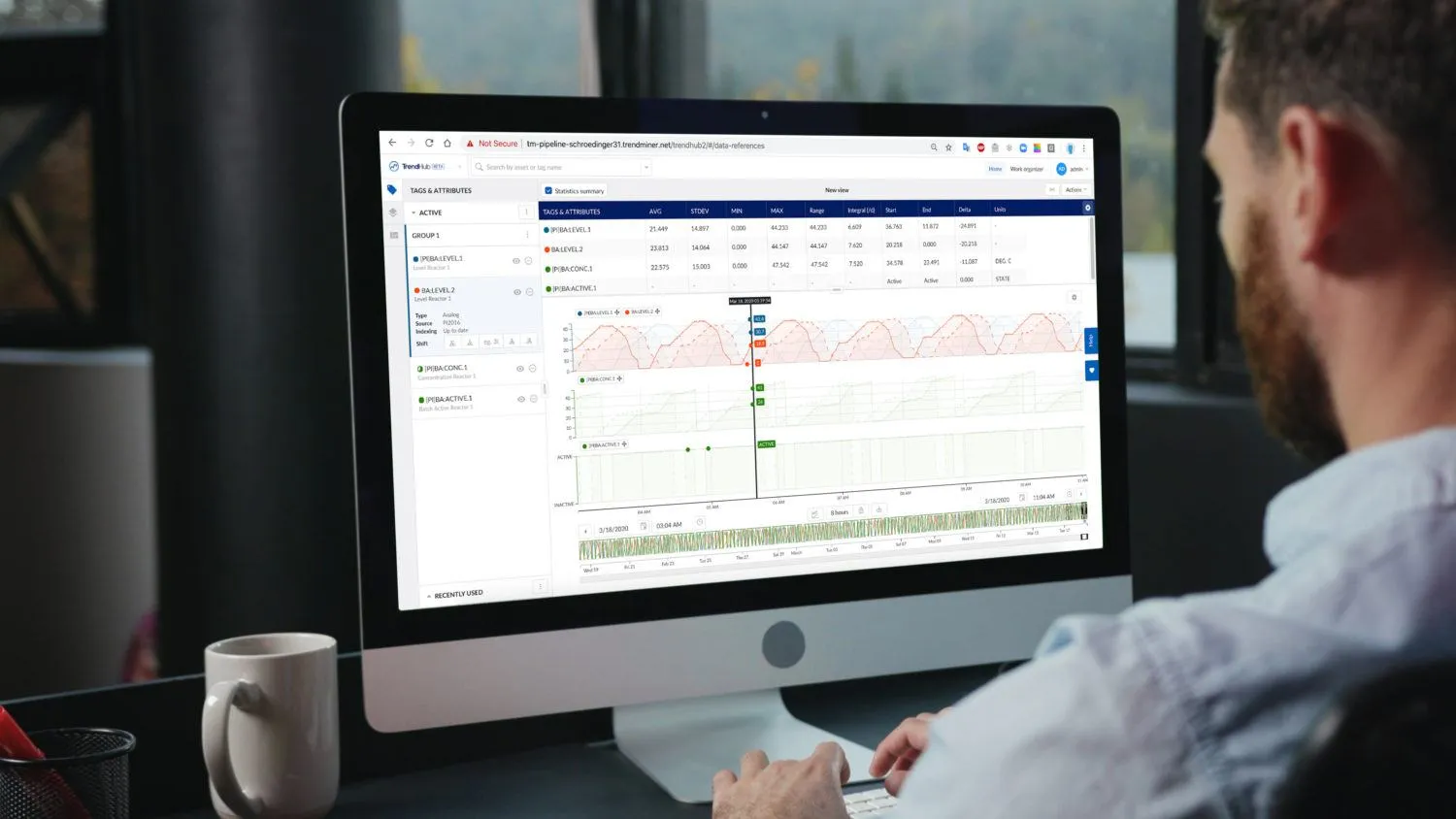
Subscribe to our newsletter
Stay up to date with our latest news and updates.
Latest Resources
Explore Our Newest Content to Maximize Your Operational Efficiency