The Importance of Timely Process Communication in Manufacturing
In this special blog post, TrendMiner customer Sukhpal Singh, Production Engineer at Kuraray America, discusses how efficient, timely process communication is essential for industrial manufacturing optimization and how a tool like TrendMiner makes this happen.
Sukhpal Singh has been in the manufacturing industry for over 10 years as a Process Operator and Engineer. He’s been involved with the key commissioning of the PVOH unit along with Methanol recovery and acid distillation. Sukhpal works on improving the final products and services for Kuraray customers through the use of advanced software like MOC tools, Yokogawa, Exaquantum, auto trends, etc. His daily routine involves professional work in research, development, design, operation, evaluation, and improvement of processes, plants, equipment, methods, or products.
Sukhpal Singh has become the winner of TrendMiner of the Year Award 2020. Watch this short interview to see how Sukhpal benefits from using TrendMiner and how TrendMiner technology assists in hybrid working mode.
The Vital Role of Effective Communication
In many ways, we have lost effective person to person communication, but we have great tools available in this age to talk to each other digitally. Effective communication is key for any industrial manufacturing process. And it plays a vital role in delivering a quality product to the customer. Good communication skills are essential for every team to operate an optimized plant, keeping the team working with focus and efficiency.
On the other hand, lack of communication causes many disruptions and problems. Process trouble can be prevented well ahead with proper tools and engineering knowledge. And since most plants have advanced process controls and optimization to push forward to new limits, the scene is set for great plant communication given the right tool.
Communicating Critical Process Issues Through Email Alerts
A few weekends ago, while I was home, I received an email alert about a potential process issue. I got in my truck, drove to the plant, and walked up to my team and asked them what they were doing and what was going on. They were surprised to see me and wondered how I knew there was an issue. I told them that I had received an alert by email from our industrial analytics software which monitors our operations. I knew exactly what the critical process problem was by the alert. With process monitors and alerts in place, we were able to take preventive actions diverting a more serious incident.
Never Miss an Alarm
Alarms are essential to notify personnel and keep the plant safe and stable. But sometimes an alarm can be missed by operation and can lead to an incident which costs money and disrupts the plant in delivering a quality product. There are some tools available to communicate critical process issues to operators and engineers. Tools like TrendMiner’s self-service analytics can send critical emails on a specific vital process to the defined group.
For example, if a distillation column is flooding and differential pressure is rising, a new board operator may not be able to detect that. Engineers can set automatic alerts to be promptly informed, so they can reach out to operation to fix the problem before it becomes more significant. This type of communication through a useful analytics tool allows for a faster response from the critical teams in your plants.
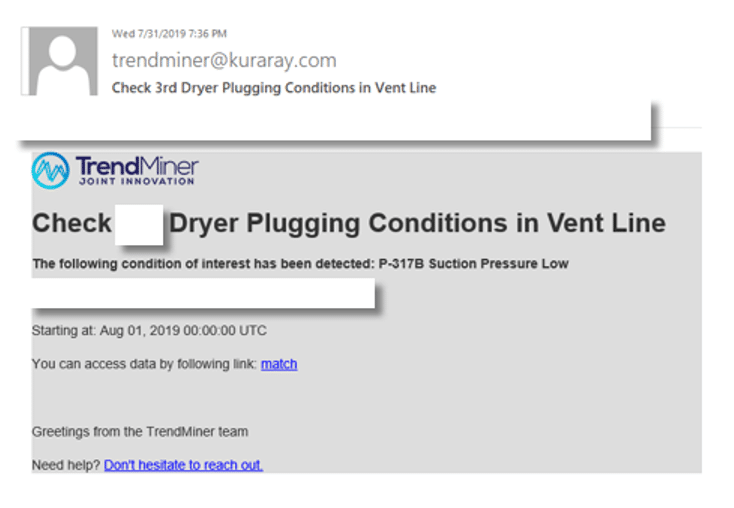
Automatic Report Generation Eases a Plant Manager’s Job
As you well know, engineers use excel sheets heavily to analyze data and then to communicate the findings to the involved people. Engineers must rely on emails, presentations, and phone calls to get their messages and their information across. Additionally, management needs to know how the plant is operating, how the units are operating. Are the units up or down? Instead of this information getting lost between different people and numerous files, daily reports can be generated automatically with an analytics tool like TrendMiner.
Generating reports automatically saves experts time looking for the information. Moreover, since plant managers have busy schedules, they may not always be available for a phone communication to receive necessary process information. They need to know if the production units are making quality products – if the production unit goes down. They can know this information automatically in the TrendMiner.
Safety Is Improved with Effective Plant Communication
Safety is essential in the plants, and effective plant communication is necessary to ensure it. Missed communication in safety processes can be bad for the operation and can result in injuries. A well-designed process will shut down automatically to prevent big fires or incidents. However, when management receives automatic email alerts, they can respond quicker, preventing safety and environmental incidents.
Process Optimization Using Data Evaluation Tools
Optimization has become easier with newly available tools for engineers. TrendMiner is one of these tools, and this software makes it very easy to correlate process tags with a confidence of higher than 90%. I have used this tool to directly communicate relationships with operations, so our teams can find the optimal points right away. Optimizing the plants will cause less upsets, and energy can be lowered to minimal levels.
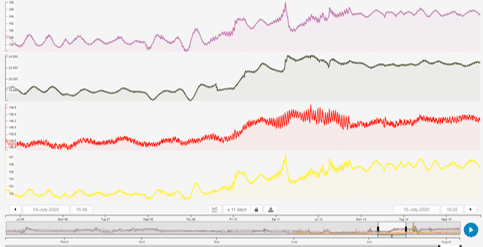
Our plant has also used TrendMiner to manage live data tracking of startups. This tool makes it easier to compare our best old startups to the current start up trends. You can use your old start up trends to compare with live trends to communicate the differences in the startup which will lead to consistent efficient same startups every time. This reduces waste generation and quick start ups.
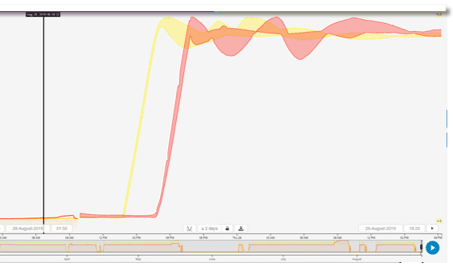
Final Thoughts
Effective communication improves plant productivity and process stability. Response to plant upsets becomes faster by using tools such as TrendMiner that can provide this level of communication. The plant becomes more integrated by receiving proper communication and messaging across all levels.
Improved communication through automatic email alerts saves time and increases production efficiency. Safety and environmental incidents are prevented since process monitoring can be set to send alerts to the relevant personnel, so they can take preventive action. And achieving optimization becomes easier. By tracking startups, you can substantially reduce energy and waste.