Achieving Smart Factory Success: Goals and Challenges
How do you realize a Smart Factory? What are usual goals and challenges? And what are some of the positive outcomes gained? All good questions. It may sound complicated, but once you understand what this entails including some of its goals and challenges, then you can structure a plan. And knowing the positive outcomes, you’ll be psyched about making this happen for your plant.
What You Need to Achieve a Smart Factory
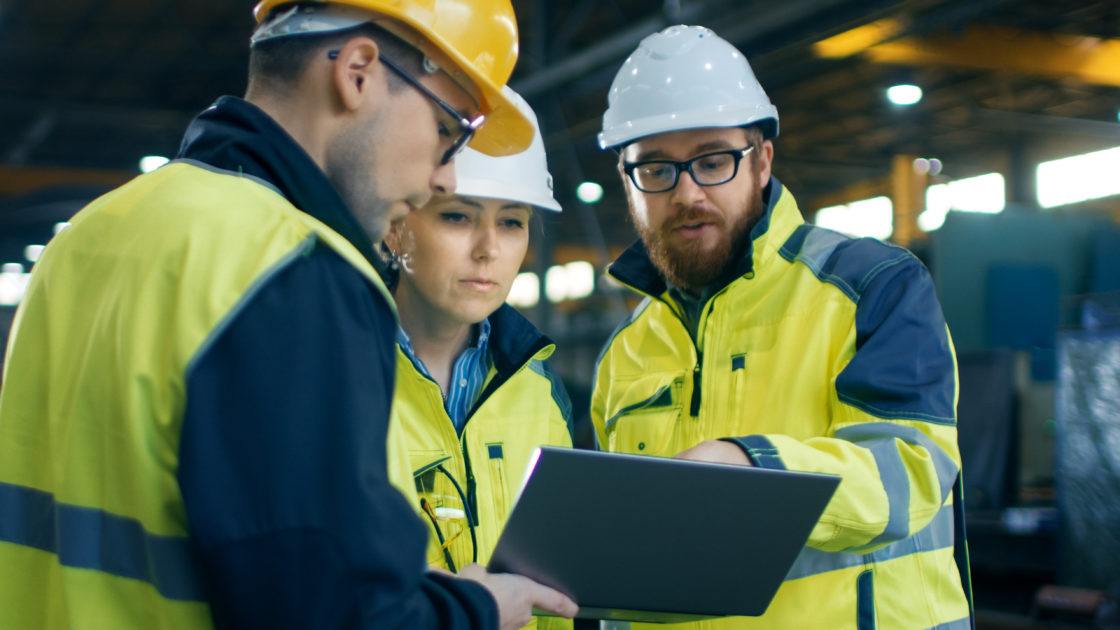
Realizing this goal involves bringing together different facets to create a manufacturing cyber and physical system. What’s needed? First, most if not all machines and equipment in your factory should have embedded sensors that will capture the manufacturing processing data – aka digitalization.
Second, your factory should have the capability to collect, transmit, and store this data, so it should have a data communication system for transmission and access to cloud storage systems or high-performance databases.
Third, your factory should implement and utilize a powerful, easy-to-understand self-service analytics tool that uses patented pattern recognition technology to translate plant data into usable information.
Moreover, personnel at all levels of the operation – such as subject matter experts and plant operators – should be able to use this tool. Why? Because they are the ones who know the manufacturing process, and they are the ones that know what the data is telling about the process. They can then act on this information. Basically, this is the purpose of having a Smart Factory: capturing and analyzing the manufacturing data to assist process experts and operators in running the plant at its highest level.
Smart Factories – The Goals & Inevitable Challenges
The goals are straight forward.
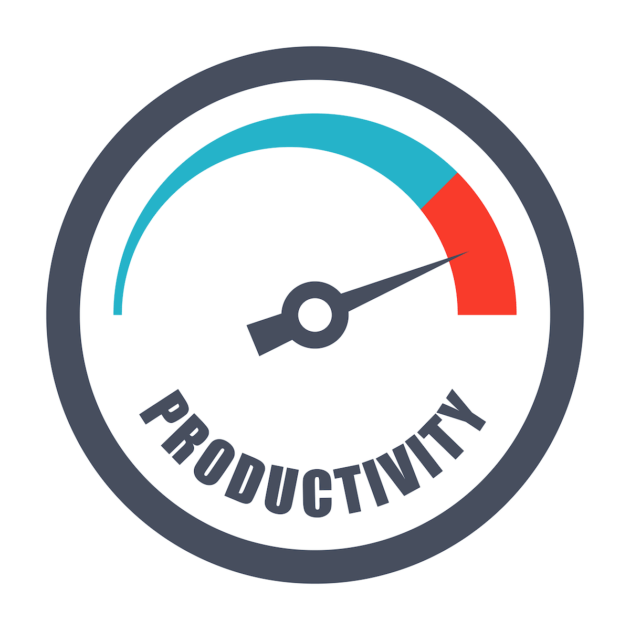
Clearly, the company would want to embrace technological advancements, fully utilize the plant’s design and data, establish solid, fluid, and safe operating practices, and create a knowledgeable, supportive and effective team to run the factory. The key is to have the plant process experts recognize the importance of making data-driven decisions and using, analyzing, and applying the insights gained from this data to guide the factory to its maximum operating level.
Okay, now the challenges.
The company must ensure the correct organizational support is in place in order to fully realize their goal of becoming a Smart Factory. The first challenge for a company will be developing and supporting crucial areas of expertise: IT experts, subject matter experts, analytics team leaders, and change management experts.
- IT experts must know how to retrieve and store the data, so they must have skills in data aggregation, cloud storage, and data servers and know how to maintain these new systems, sensors and software.
- Subject matter experts are the ones that fully understand the plant set up and its processes. They will understand the story the data is telling. However, they will need an analytics tool to translate data into actionable information.
- Analytics team leaders would be the plant personnel chosen to be trained to use the self-service analytics software. They would then lead others in adopting new work methods and provide training and support along the way.
- Change management experts must outline and define implementation measures to be taken by the company to realize the Smart Factory. Such measures must identify operators and track performance. These findings can then be used to make effective decisions to achieve agile, consistent, and optimal operation.
The second challenge will be selecting a specific process to serve as the pilot. The pilot will be used to demonstrate the feasibility and worth of the self-service industrial analytics tool and to quickly show improvements to plant management. Once the pilot is successful, then more processes can be trialed and proven. Another outcome of the pilot is obtaining a better understanding of how to achieve improved plant performance and to achieve greater plant efficiency.
The third challenge is getting everyone from top-management to factory floor personnel to develop a new mindset and to embrace a new way of running the factory. One way to do this is by showing operational improvements quickly through the pilot run; it is easier to convince factory experts to get on board when they see the value of the new approach. Another way is to provide the needed support and encouragement. Setting up a support team structure is crucial.
Substantial Positive Outcomes
Plant efficiency and flexibility are increased. Process experts have greater visibility into the factory operation, so they can more effectively steer the process. Plant management is better supported since a self-service analytics tool allows operators to identify process deviations and take corrective measures. Additionally, such a tool can reveal hidden process restrictions and predict failure and maintenance issues. Plant managers will be able to maximize plant operation, save energy, reduce waste and downtime, and gain greater profitability.
Make the Change – Realizing a Smart Factory Is Worth It
Realizing a Smart Factory is a journey. Understanding the goals, challenges and positive outcomes is the beginning. But, in a nutshell:
- Digitize your plant to capture manufacturing data.
- Have a system in place that can handle and store this information.
- Use a self-service analytics tool to analyze the data.
- Train your team to use this software to understand the story it’s telling.
- Then let them act on this information, allowing them to improve the manufacturing process.
Each organizational level plays a part in the plant’s operations, and by giving process experts a user-friendly industrial data analytics platform, management is adopting a forward-thinking and competitive strategy to optimize not only plant operations but also plant personnel. What you get is a highly functional and productive team and plant. The results? Breakthroughs in productivity, profitability, and competitiveness.
Break from the past and envision a better future – You may already be halfway there!