Root Cause Analysis and Troubleshooting using TrendMiner Industrial Analytics
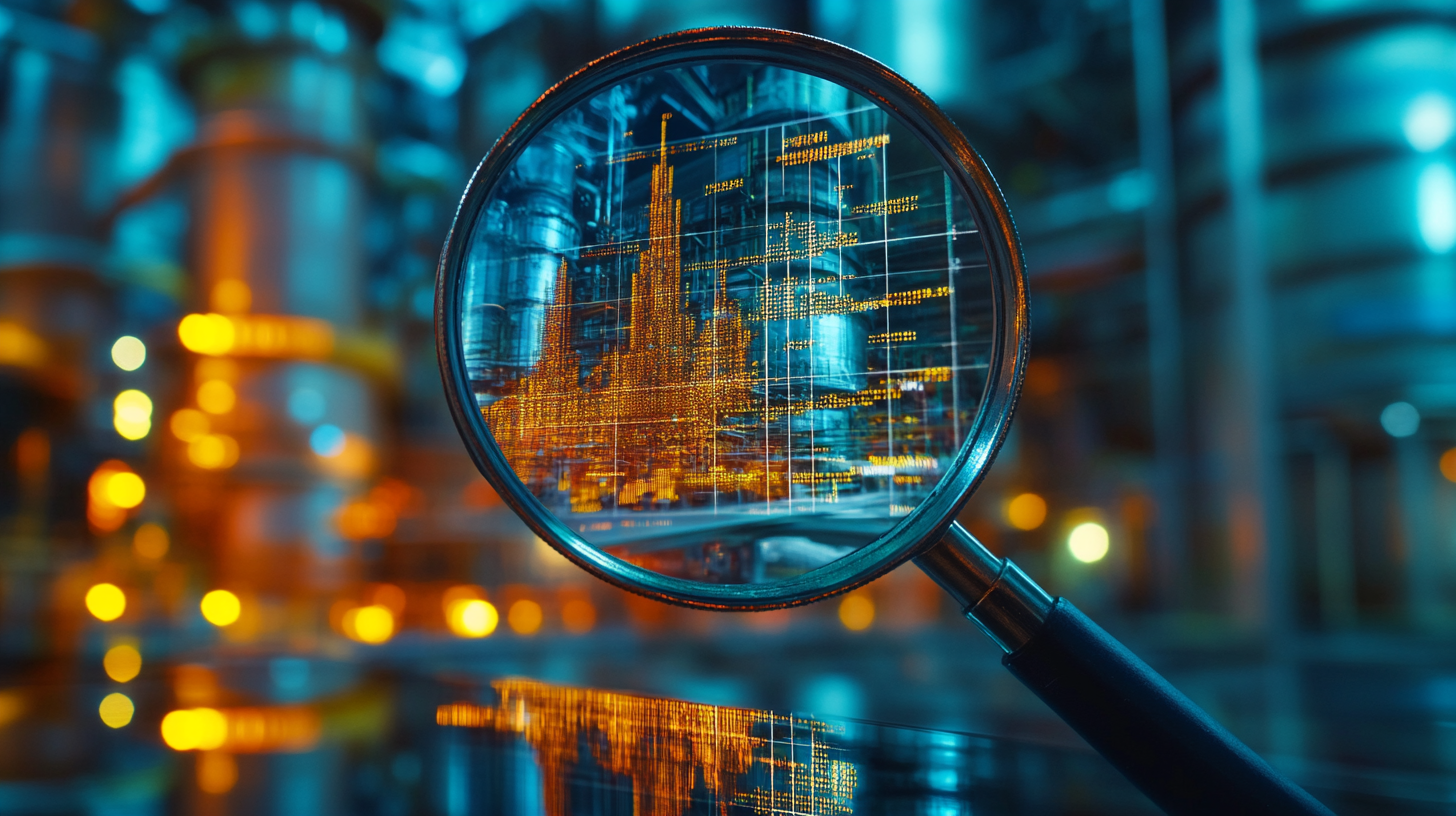
Table of Contents
Root cause analysis is a critical process in industrial settings, aimed at identifying the underlying cause of a problem or an issue. It involves digging deeper into the factors that contribute to a particular event, allowing for effective troubleshooting and problem-solving. In today’s complex industrial landscape, where data is abundant and varied, leveraging advanced analytics tools such as TrendMiner can greatly enhance the root cause analysis process. This article explores the concept of root cause analysis, introduces various troubleshooting methods, and highlights the benefits of using TrendMiner Industrial Analytics for effective problem-solving.
What is Root Cause Analysis?
Root cause analysis is a systematic approach used to identify the fundamental reason behind an issue or problem in an industrial process. It goes beyond addressing the symptoms and focuses on understanding the underlying causes that lead to the occurrence of an event. By determining the root cause, organizations can implement effective corrective actions, prevent future occurrences, and optimize their processes.
Introduction to Troubleshooting Methods
Troubleshooting methods are techniques used to identify and resolve problems in industrial processes. These methods include fault tree analysis, fishbone diagrams, and the 5 Whys technique. Fault tree analysis involves mapping out the potential causes of an event in a tree-like structure to determine the most likely root cause. Fishbone diagrams, also known as cause-and-effect diagrams, visually represent the possible causes of an issue, helping in the identification of the root cause. The 5 Whys technique involves repeatedly asking “why” to get to the underlying cause of a problem, peeling back the layers until the root cause is revealed.
Leveraging TrendMiner Industrial Analytics
TrendMiner Industrial Analytics is an advanced analytics tool designed to analyze and visualize time-series data from various industrial sources. By leveraging machine learning and pattern recognition algorithms, TrendMiner enables organizations to gain valuable insights into their data, making it an ideal tool for root cause analysis and troubleshooting. TrendMiner’s intuitive interface allows users to explore their data, identify anomalies, and detect patterns that may indicate the root cause of an issue. The tool also offers advanced search capabilities, empowering users to search for specific events, trends, or patterns, making the troubleshooting process more efficient and effective.
Key Benefits of using TrendMiner Analytics
TrendMiner Industrial Analytics offers several key benefits when it comes to root cause analysis and troubleshooting. Firstly, it allows for faster and more accurate analysis by providing users with real-time access to their data and enabling them to quickly identify patterns and anomalies. This accelerates the root cause identification process, leading to faster problem resolution and reduced downtime. Additionally, TrendMiner’s machine learning capabilities enable it to learn from historical data, allowing for predictive analytics and the ability to proactively address potential issues. Finally, the user-friendly interface and intuitive search capabilities make TrendMiner accessible to all levels of users, from operators to data scientists, facilitating collaboration and knowledge sharing.
Applying Root Cause Analysis with TrendMiner
When applying root cause analysis with TrendMiner, organizations can follow a systematic approach. They can start by defining the problem, clearly stating the symptoms, and collecting relevant data. TrendMiner can then be used to analyze the data, visualizing it in easy-to-understand dashboards and identifying any patterns or deviations from normal operation. By exploring the data and drilling down into specific time periods or variables, the root cause of the issue can be determined. Once the root cause is identified, organizations can develop and implement corrective actions to prevent future occurrences.
Case Studies: Successful Troubleshooting Examples
Several industrial organizations have successfully utilized TrendMiner for root cause analysis and troubleshooting. In one case, a chemical plant experienced repeated equipment failures leading to significant downtime. By analyzing historical data in TrendMiner, the root cause was identified as a specific operating condition that caused excess stress on the equipment. This allowed the organization to adjust their operating practices, resulting in a decrease in equipment failures and improved overall performance. In another case, a power plant used TrendMiner to analyze data from multiple sensors to identify the root cause of increased energy consumption. The analysis revealed a malfunctioning valve, which was promptly replaced, leading to reduced energy costs and increased efficiency.
In conclusion, root cause analysis is a crucial process in industrial settings, enabling organizations to identify the underlying causes of problems and effectively troubleshoot them. Leveraging advanced analytics tools like TrendMiner Industrial Analytics enhances the root cause analysis process by providing real-time access to data, enabling faster analysis, and facilitating collaboration. By applying a systematic approach and utilizing TrendMiner’s capabilities, organizations can proactively address issues, prevent future occurrences, and optimize their processes for increased efficiency and performance.
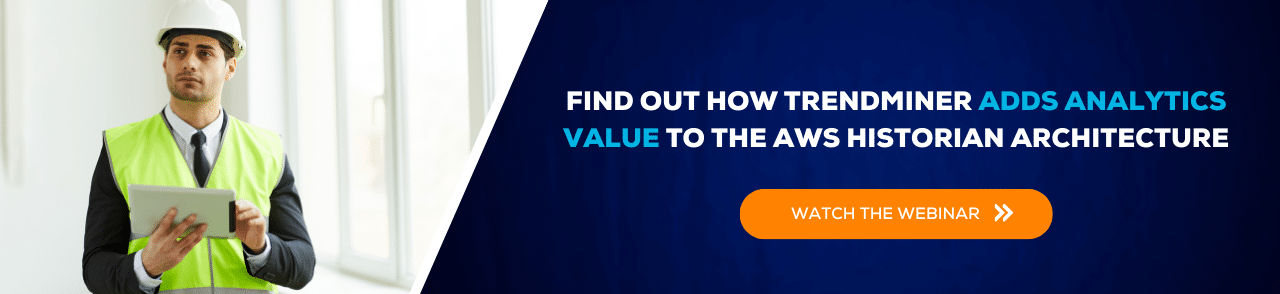
This content was generated using AI. While TrendMiner strives for accuracy, we encourage readers to verify important information. We use AI-generated content to increase efficiencies and provide certain insights, but it may not reflect human expertise or opinions
Unlock Your Industrial Potential
Discover how our analytics solutions can transform your process industry operations today.
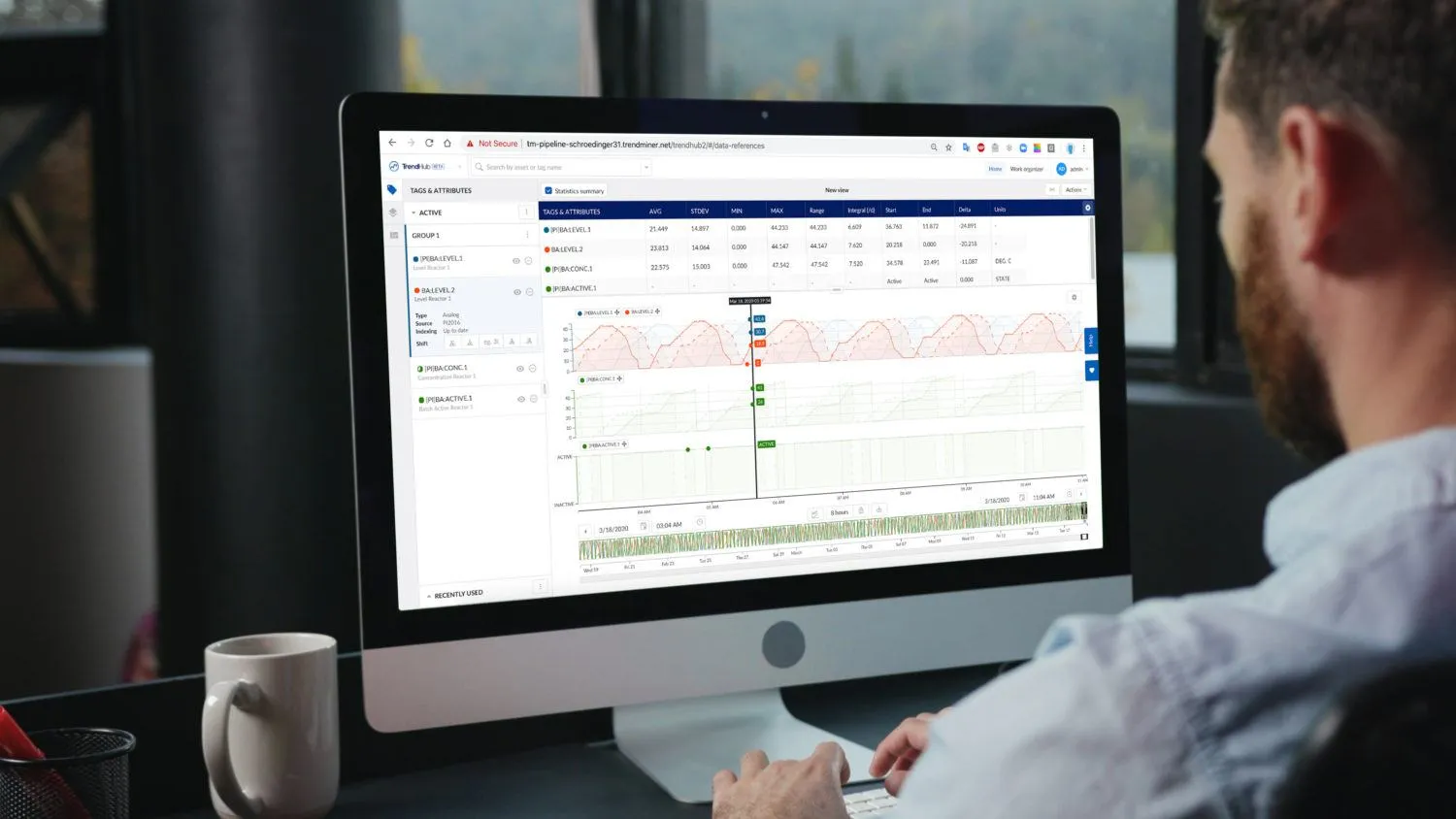
Subscribe to our newsletter
Stay up to date with our latest news and updates.
Latest Resources
Explore Our Newest Content to Maximize Your Operational Efficiency