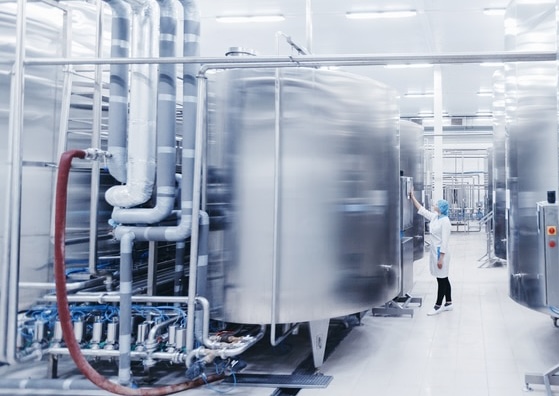
Situation
Infant cereals in at a food manufacturing factory go through a pasteurization process. The old pasteurization unit was thought to cause a bottleneck, so the company installed a new one. Two different lines (Line 1 and Line 2) had been set up. The lines are long pipes where a mix of flour, water, and additives is added to steam. The feed undergoes a thermic treatment where high temperatures (about 120º C) remove microorganisms. After that, a flash tank is connected to the outlet to remove the remaining steam and cool the product.
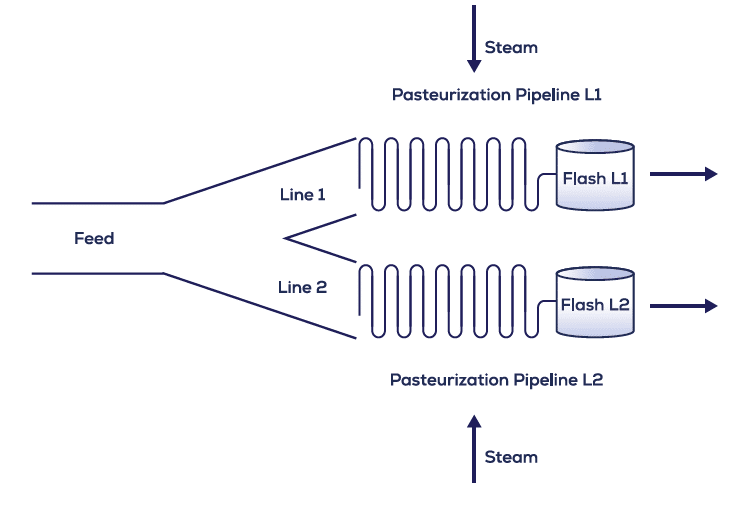
Problem
After just a month of operation, the new pasteurization unit has caused a lot of concerns. The most critical of these is unplanned shutdowns. When Line 1 is running and Line 2 starts up, Line 1 shuts down about 50-60% of the time. Because production calls for several recipe batches that require planned shutdowns, engineers cannot have any unplanned events to keep up with market demand. When the line does shut down, production loses two hours of time and wastes the batch.
Goals
- Understand what is causing the pasteurization line shutdowns
- Propose a solution to prevent them
Challenges
- Many variables involved in the pasteurization unit could be causing the trip
- Engineers lack information about the large number of automatic conditions that can cause the line to trip
- Programmers and more experienced process engineers do not have time to search for a cause
Approach
- Load and visualize the trends of the main variables associated with the pasteurization unit
- Analyze the behavior of the process during a shutdown
- Conduct value based and similarity searches to retrieve shutdown periods
- Add layers to compare different shutdowns
- Export meaningful charts to create reports and share them with the control team
Results
Overall, engineers realized 1-2% increased production, 5.4% wastes decrease, and €38,400/year in savings
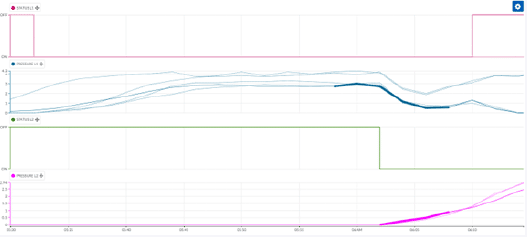
- Because both lines were connected to the same main pipe before they split, opening the valve of the Line 2 branch caused pressure in Line 1 to fall below 1.5 bars
- After the pressure had dropped for 30 seconds, Line 1 shut down
- The event only occurred when the general pressure of the main pipe fell below 5 bars
- After comparing different shutdowns, engineers determined that they could adjust the automatic shutdown to happen when the pressure dropped to 1.8 bars for at least 45 seconds
- Furthermore, whenever Line 2 is started while Line 1 already is running, the pressure will increase automatically to 7 bars for one minute
- Engineers used this information to create a dashboard where they could see other areas for improvements (maximum level reached in a tank, for example)
Situation
Infant cereals in at a food manufacturing factory go through a pasteurization process. The old pasteurization unit was thought to cause a bottleneck, so the company installed a new one. Two different lines (Line 1 and Line 2) had been set up. The lines are long pipes where a mix of flour, water, and additives is added to steam. The feed undergoes a thermic treatment where high temperatures (about 120º C) remove microorganisms. After that, a flash tank is connected to the outlet to remove the remaining steam and cool the product.
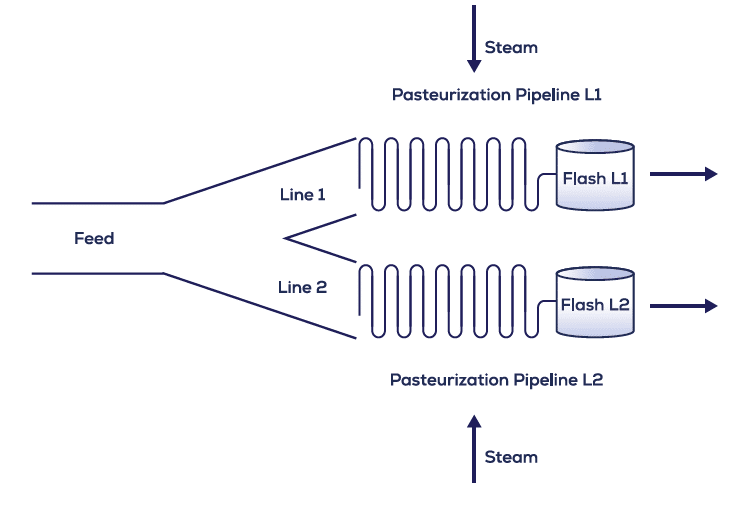
Problem
After just a month of operation, the new pasteurization unit has caused a lot of concerns. The most critical of these is unplanned shutdowns. When Line 1 is running and Line 2 starts up, Line 1 shuts down about 50-60% of the time. Because production calls for several recipe batches that require planned shutdowns, engineers cannot have any unplanned events to keep up with market demand. When the line does shut down, production loses two hours of time and wastes the batch.
Goals
- Understand what is causing the pasteurization line shutdowns
- Propose a solution to prevent them
Challenges
- Many variables involved in the pasteurization unit could be causing the trip
- Engineers lack information about the large number of automatic conditions that can cause the line to trip
- Programmers and more experienced process engineers do not have time to search for a cause
Approach
- Load and visualize the trends of the main variables associated with the pasteurization unit
- Analyze the behavior of the process during a shutdown
- Conduct value based and similarity searches to retrieve shutdown periods
- Add layers to compare different shutdowns
- Export meaningful charts to create reports and share them with the control team
Results
Overall, engineers realized 1-2% increased production, 5.4% wastes decrease, and €38,400/year in savings
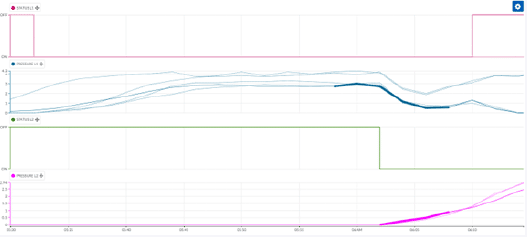
- Because both lines were connected to the same main pipe before they split, opening the valve of the Line 2 branch caused pressure in Line 1 to fall below 1.5 bars
- After the pressure had dropped for 30 seconds, Line 1 shut down
- The event only occurred when the general pressure of the main pipe fell below 5 bars
- After comparing different shutdowns, engineers determined that they could adjust the automatic shutdown to happen when the pressure dropped to 1.8 bars for at least 45 seconds
- Furthermore, whenever Line 2 is started while Line 1 already is running, the pressure will increase automatically to 7 bars for one minute
- Engineers used this information to create a dashboard where they could see other areas for improvements (maximum level reached in a tank, for example)
Download now
Subscribe to our newsletter
Stay up to date with our latest news and updates.
Other Webinars on demand
Explore Our Newest Content to Maximize Your Operational Efficiency
Other Resources
Explore Our Newest Content to Maximize Your Operational Efficiency