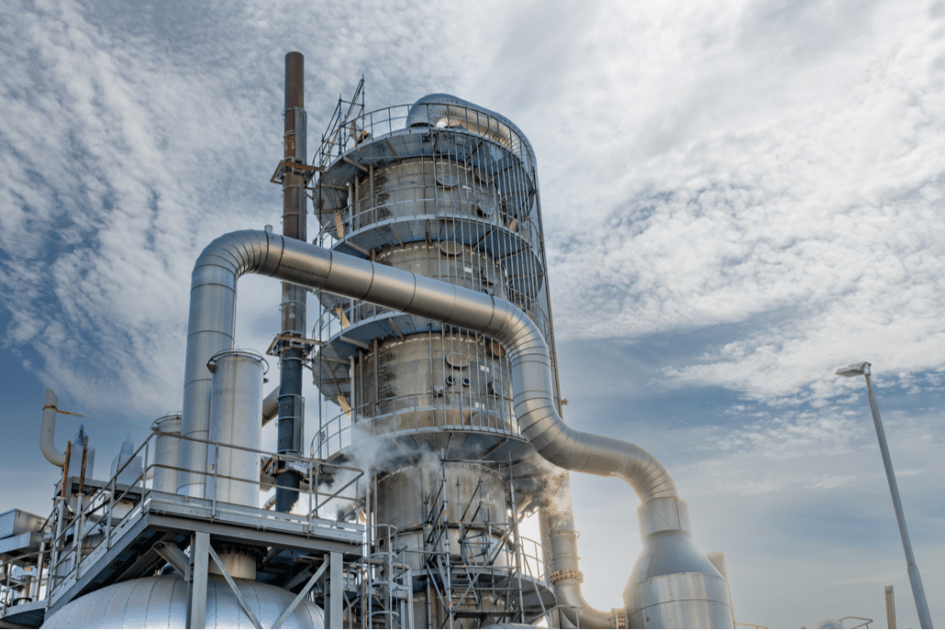
Situation
The energy management in a continuous distillation process (falling film evaporator) needed to be documented and reported. In addition, potential energy savings needed to be identified and evaluated in order to implement actions to decrease energy consumption. The steam supply (40 bar steam) was switched on and off dependent upon whether the evaporator was operating or not. In fact, switching the valve from open to closed requires manual action by a plant operator. Hence, the valve remains open for a short downtime of the evaporator (t >
8 – 12 h). To estimate the potential savings, the amount of 40 bar steam was determined when the evaporator was not under operation and the valve was not closed. The loss of 40 bar steam in tons can be directly translated into financial losses and thus needed to be addressed.
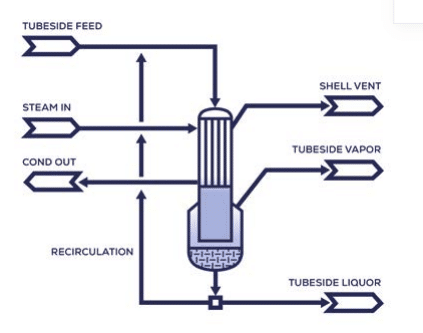
Problem
This process consisted of two parts: one manual part activated by an operator and the actual filtration part. The waiting time and fixation for the manual period needed to be identified separately from the real time period for the filtration period. Identifying periods when the evaporator was shut down and steam was supplied required filtering data in Excel, which was difficult and time consuming. Moreover, the data integration of steam flow over non-operational periods required additional steps in Excel, which required even more time. Therefore, process experts needed to be able to more quickly and easily identify these periods to understand how to reduce energy consumption. This would in turn reduce costs and increase savings.
Solution
Process experts used TrendMiner to identify periods of interest based on inlet and steam flows, so they could determine which periods were waiting times for the manual part of the process and which periods were the actual filtration part of the process.
Approach
- Filters were used to distinguish between the waiting time of the manual steps and the time for the actual filtration. Next, the time distribution between these periods were plotted.
- The total amount of steam flow during shut down period was calculated.
- Value-based searches for plant shutdowns and simultaneous steam inflows were performed to determine the steam loss in tons as an integral of steam flow and to determine the number of shutdowns that were due to equipment failure and those due to problems during the manual part of the process.
- The total amount of steam flow during a shutdown period was calculated.
- The steam consumption in weight (kg or t) was reported to determine savings potential.
- Steam flow while the evaporator was not in operation was monitored to analyze the optimization potential.
Results
After the analysis, it was discovered that there were 18 times the cycle time exceeded the acceptable time range. Three of these times were due to equipment failure, and the rest were due to problems/inefficiencies in performing the manual step of the process. Equipment failure is not easily controlled. However, problems with the manual step was resolved by establishing a standardized procedure which gave specific instructions to the operators on how to perform this step. Additional results included the following:
- In 2020, events of steam savings potential were realized, one for approximately 60 tons of steam (40 bar) for more than 10 hours and additional events for less than 10 hours resulting in further savings potential.
- Time savings for reporting steam losses were realized.
- Monitors for steam loss were set to send email notifications to the control room in case a valve is not closed for 10 hours during non-operational periods thus justifying the investment in a controlled steam valve.
Situation
The energy management in a continuous distillation process (falling film evaporator) needed to be documented and reported. In addition, potential energy savings needed to be identified and evaluated in order to implement actions to decrease energy consumption. The steam supply (40 bar steam) was switched on and off dependent upon whether the evaporator was operating or not. In fact, switching the valve from open to closed requires manual action by a plant operator. Hence, the valve remains open for a short downtime of the evaporator (t >
8 – 12 h). To estimate the potential savings, the amount of 40 bar steam was determined when the evaporator was not under operation and the valve was not closed. The loss of 40 bar steam in tons can be directly translated into financial losses and thus needed to be addressed.
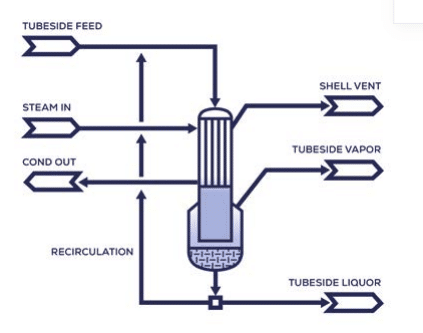
Problem
This process consisted of two parts: one manual part activated by an operator and the actual filtration part. The waiting time and fixation for the manual period needed to be identified separately from the real time period for the filtration period. Identifying periods when the evaporator was shut down and steam was supplied required filtering data in Excel, which was difficult and time consuming. Moreover, the data integration of steam flow over non-operational periods required additional steps in Excel, which required even more time. Therefore, process experts needed to be able to more quickly and easily identify these periods to understand how to reduce energy consumption. This would in turn reduce costs and increase savings.
Solution
Process experts used TrendMiner to identify periods of interest based on inlet and steam flows, so they could determine which periods were waiting times for the manual part of the process and which periods were the actual filtration part of the process.
Approach
- Filters were used to distinguish between the waiting time of the manual steps and the time for the actual filtration. Next, the time distribution between these periods were plotted.
- The total amount of steam flow during shut down period was calculated.
- Value-based searches for plant shutdowns and simultaneous steam inflows were performed to determine the steam loss in tons as an integral of steam flow and to determine the number of shutdowns that were due to equipment failure and those due to problems during the manual part of the process.
- The total amount of steam flow during a shutdown period was calculated.
- The steam consumption in weight (kg or t) was reported to determine savings potential.
- Steam flow while the evaporator was not in operation was monitored to analyze the optimization potential.
Results
After the analysis, it was discovered that there were 18 times the cycle time exceeded the acceptable time range. Three of these times were due to equipment failure, and the rest were due to problems/inefficiencies in performing the manual step of the process. Equipment failure is not easily controlled. However, problems with the manual step was resolved by establishing a standardized procedure which gave specific instructions to the operators on how to perform this step. Additional results included the following:
- In 2020, events of steam savings potential were realized, one for approximately 60 tons of steam (40 bar) for more than 10 hours and additional events for less than 10 hours resulting in further savings potential.
- Time savings for reporting steam losses were realized.
- Monitors for steam loss were set to send email notifications to the control room in case a valve is not closed for 10 hours during non-operational periods thus justifying the investment in a controlled steam valve.
Download now
Subscribe to our newsletter
Stay up to date with our latest news and updates.
Other Webinars on demand
Explore Our Newest Content to Maximize Your Operational Efficiency
Other Resources
Explore Our Newest Content to Maximize Your Operational Efficiency