Unleash Smart Factory data with Real-time Monitoring & Alerting for High-Tech Manufacturing
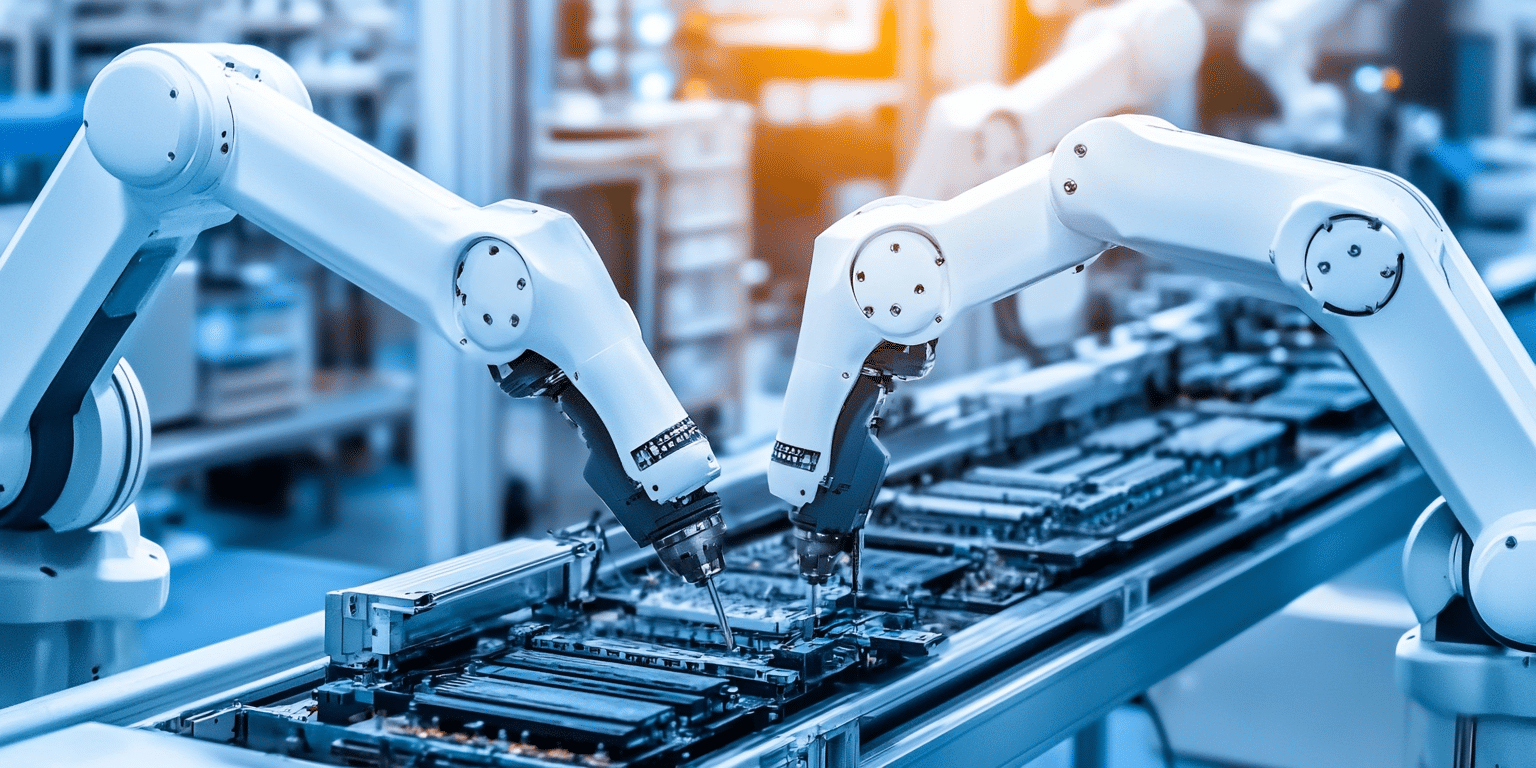
Situation
High-Tech manufacturing companies are at the forefront of a transformative wave, driven by the vision of building the Smart Factory. In these advanced production environments, machines and systems are interconnected, allowing communication across the entire manufacturing process. This connectivity is a strategic move towards operational excellence and competitive advantage.
The approach results in the continuous collection of vast amounts of data from various stages of production, ranging from raw material handling to final product assembly. However, the true potential of a Smart Factory lies in its ability to transform this raw data into actionable insights and tangible business value. The challenge for High-Tech manufacturers is not just to collect data but to effectively leverage it.
Challenges
The manual workflow involves several cumbersome steps:
- Process experts manually download data from individual production machines.
- Data scientists prepare and clean the data using tools like MatLab or Python.
- Multiple batches of data are plotted and layered for comparison in Excel.
- The results are shared with the shopfloor expert via spreadsheets.
- Implementing changes based on the analysis is slow, and often the insights are not revisited.
This process not only takes approximately 2 hours but also poses significant challenges:
- The approach is reactive rather than proactive.
- Sharing results and analyses is difficult.
- Live-monitoring and alerting capabilities are non-existent, leading to a lack of timely interventions.
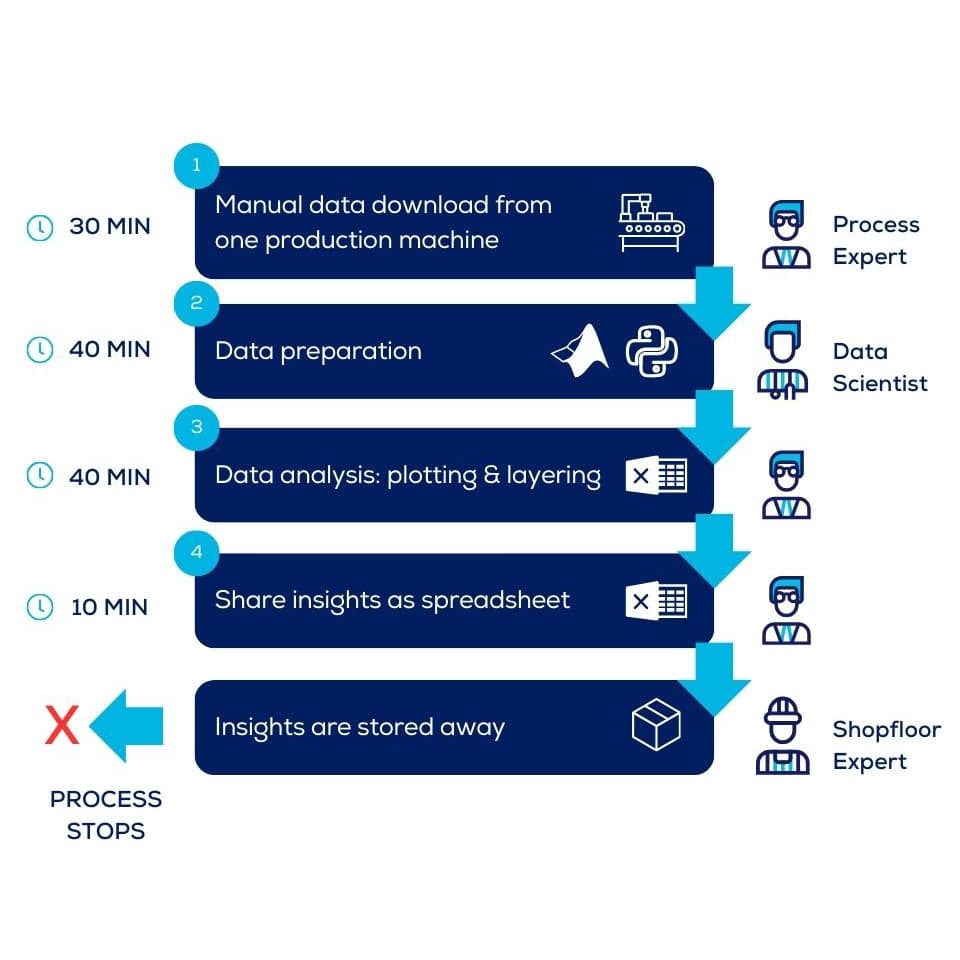
Problem
A High-Tech manufacturing company aims to optimize its production process by leveraging data analytics. Traditionally, data from production machines are manually downloaded and analyzed by process experts and data scientists. This method is time-consuming and inefficient, hindering the company’s ability to quickly adapt to changes and improve processes.
Solution
Implementing TrendMiner Self-Service Analytics revolutionizes the workflow by bringing all steps together in one tool:
- Data from all types of machines and other sources are visualized in seconds using TrendMiner.
- Data preparation: Identify time periods of interest and filter out not relevant events in seconds
- Data analysis quickly and easily performed: batches are compared in only a few clicks without the need for data science knowledge.
- Alerts and insights are immediately set up and insights are shared with colleagues.
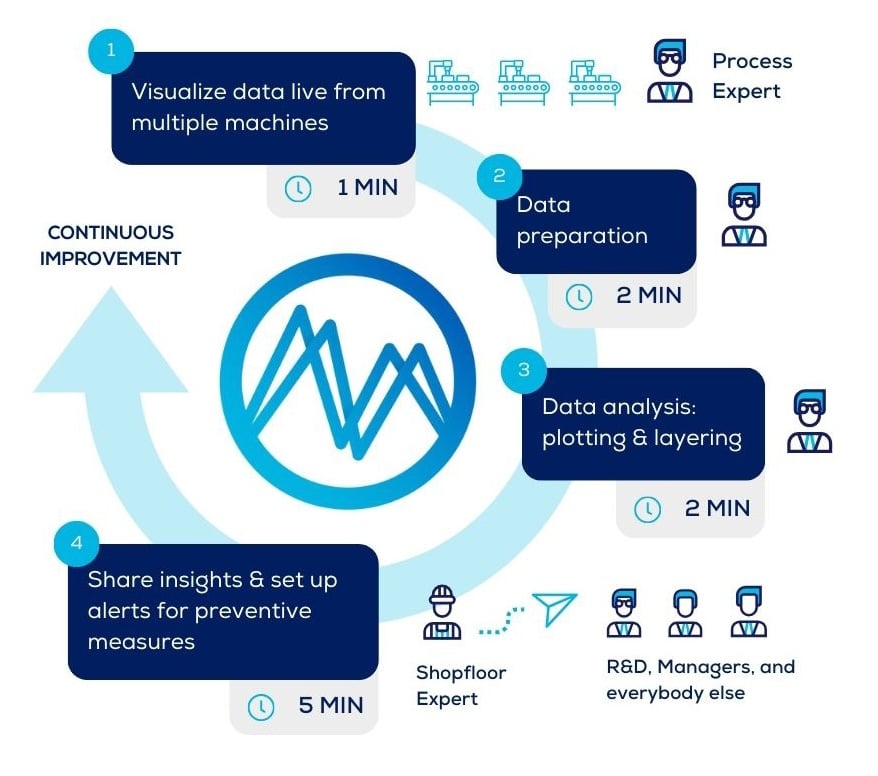
Results
- Time Savings – The automated process reduces the time required for data analysis from 2 hours to just a few minutes, allowing the team to focus on actionable insights rather than data preparation.
- Efficiency Improvement – Achieving a huge increase in efficiency enables the company to react faster to production issues and implement changes more swiftly.
- Proactive Monitoring – The ability to set up alerts and continuously monitor production parameters helps in identifying and addressing potential problems before they escalate, e.g. in form of Predictive Maintenance.
- Scalability – The solution is scalable to other systems and parameters, making it adaptable to various production environments and requirements.
- Enhanced Collaboration – Immediate sharing of insights fosters better communication and collaboration among team members, leading to data-driven decision-making and continuous improvement.
By leveraging TrendMiner, the manufacturing company can achieve a higher level of operational efficiency, ensure better utilization of resources, and drive overall productivity.
Situation
High-Tech manufacturing companies are at the forefront of a transformative wave, driven by the vision of building the Smart Factory. In these advanced production environments, machines and systems are interconnected, allowing communication across the entire manufacturing process. This connectivity is a strategic move towards operational excellence and competitive advantage.
The approach results in the continuous collection of vast amounts of data from various stages of production, ranging from raw material handling to final product assembly. However, the true potential of a Smart Factory lies in its ability to transform this raw data into actionable insights and tangible business value. The challenge for High-Tech manufacturers is not just to collect data but to effectively leverage it.
Challenges
The manual workflow involves several cumbersome steps:
- Process experts manually download data from individual production machines.
- Data scientists prepare and clean the data using tools like MatLab or Python.
- Multiple batches of data are plotted and layered for comparison in Excel.
- The results are shared with the shopfloor expert via spreadsheets.
- Implementing changes based on the analysis is slow, and often the insights are not revisited.
This process not only takes approximately 2 hours but also poses significant challenges:
- The approach is reactive rather than proactive.
- Sharing results and analyses is difficult.
- Live-monitoring and alerting capabilities are non-existent, leading to a lack of timely interventions.
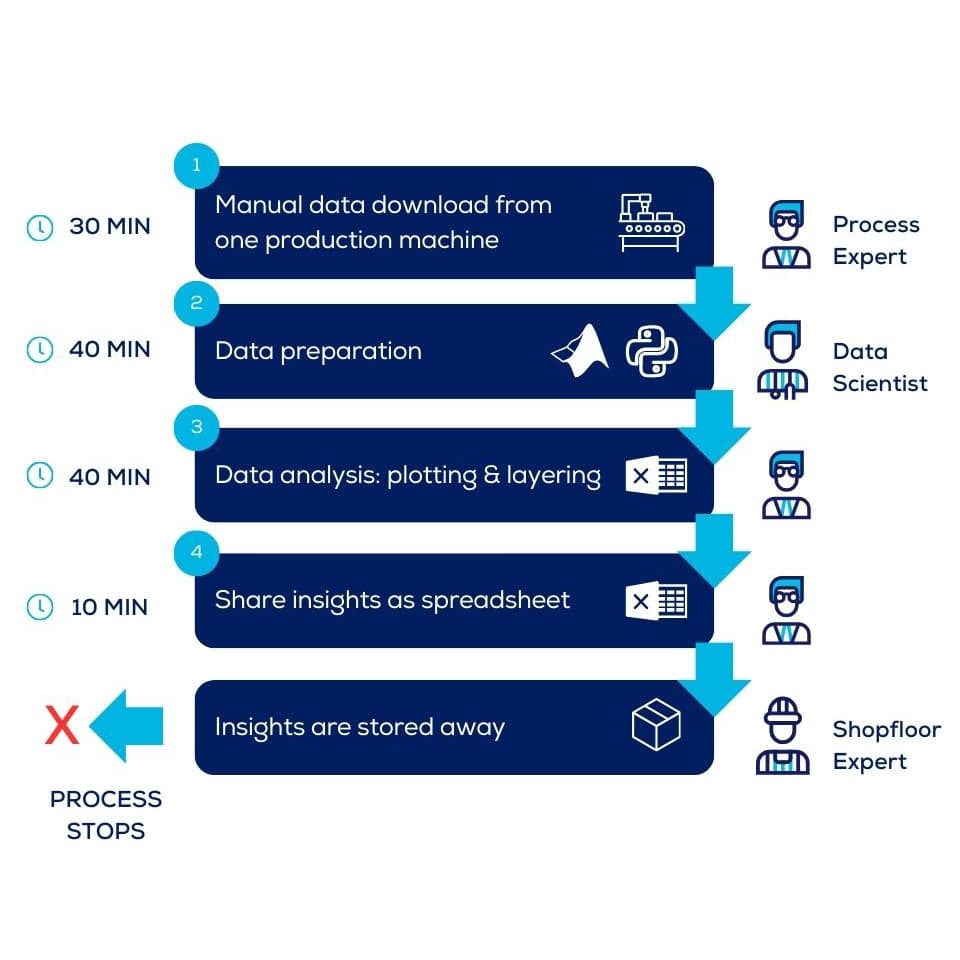
Problem
A High-Tech manufacturing company aims to optimize its production process by leveraging data analytics. Traditionally, data from production machines are manually downloaded and analyzed by process experts and data scientists. This method is time-consuming and inefficient, hindering the company’s ability to quickly adapt to changes and improve processes.
Solution
Implementing TrendMiner Self-Service Analytics revolutionizes the workflow by bringing all steps together in one tool:
- Data from all types of machines and other sources are visualized in seconds using TrendMiner.
- Data preparation: Identify time periods of interest and filter out not relevant events in seconds
- Data analysis quickly and easily performed: batches are compared in only a few clicks without the need for data science knowledge.
- Alerts and insights are immediately set up and insights are shared with colleagues.
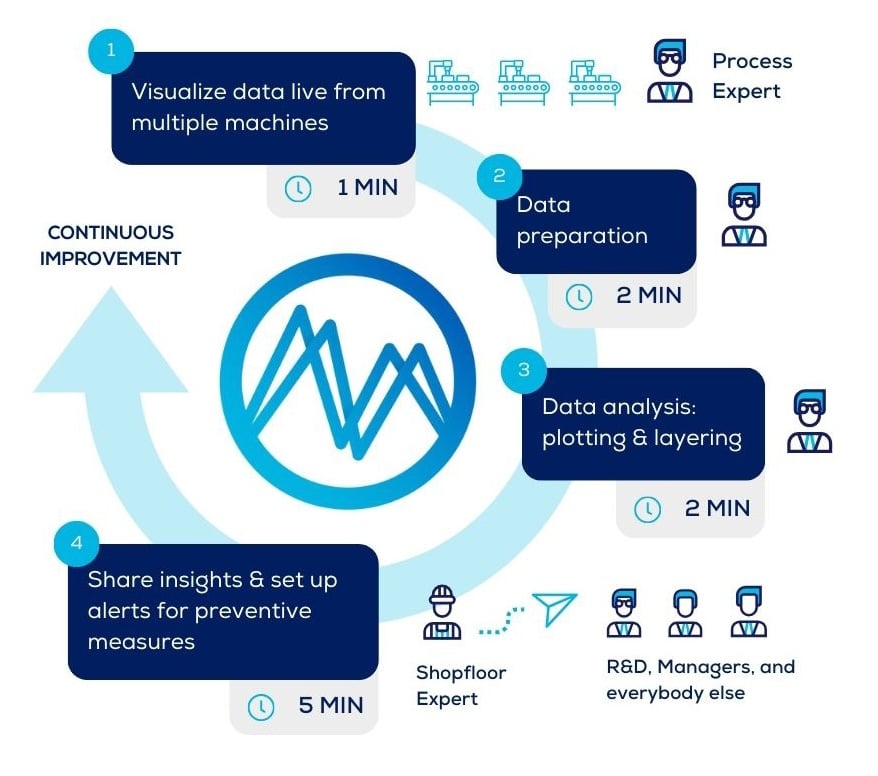
Results
- Time Savings – The automated process reduces the time required for data analysis from 2 hours to just a few minutes, allowing the team to focus on actionable insights rather than data preparation.
- Efficiency Improvement – Achieving a huge increase in efficiency enables the company to react faster to production issues and implement changes more swiftly.
- Proactive Monitoring – The ability to set up alerts and continuously monitor production parameters helps in identifying and addressing potential problems before they escalate, e.g. in form of Predictive Maintenance.
- Scalability – The solution is scalable to other systems and parameters, making it adaptable to various production environments and requirements.
- Enhanced Collaboration – Immediate sharing of insights fosters better communication and collaboration among team members, leading to data-driven decision-making and continuous improvement.
By leveraging TrendMiner, the manufacturing company can achieve a higher level of operational efficiency, ensure better utilization of resources, and drive overall productivity.
Download now
Subscribe to our newsletter
Stay up to date with our latest news and updates.
Other Webinars on demand
Explore Our Newest Content to Maximize Your Operational Efficiency
Other Resources
Explore Our Newest Content to Maximize Your Operational Efficiency