Huntsman’s Journey Towards Analytics Maturity & Operational Excellence
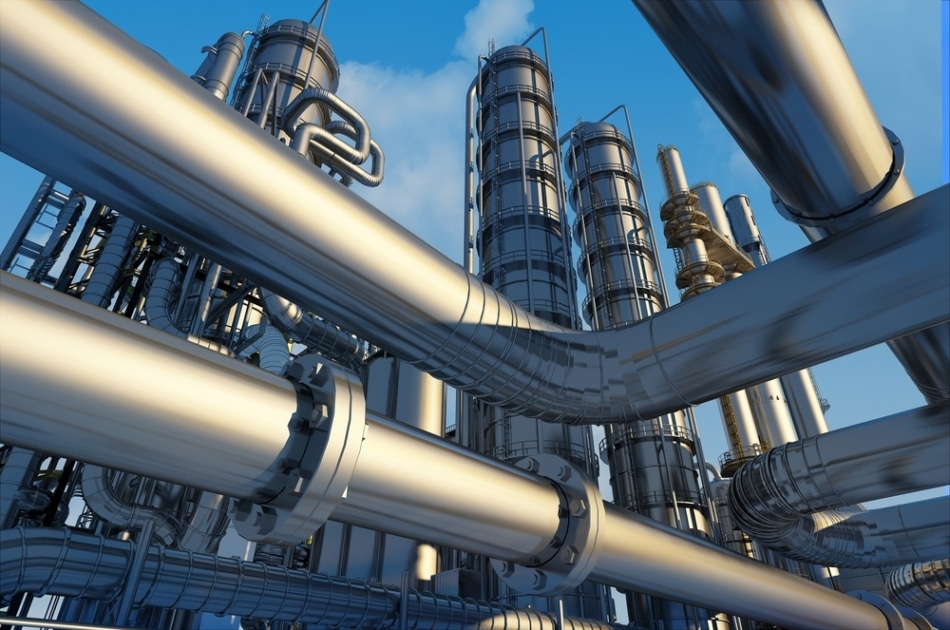
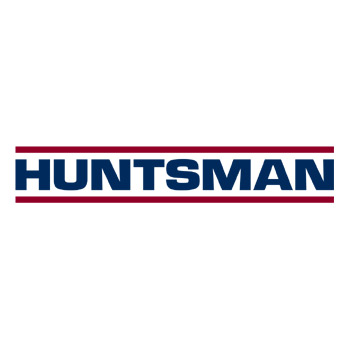
Huntsman Journey & Business Challenges
Historically, Huntsman process engineers would use their extensive
experience and process knowledge to try to understand the sensor-generated data. This approach was experience-driven rather than data-driven.
The company wanted to fully leverage the captured time-series data by transforming toward a data-driven work approach. However, first two challenges had to overcome: one related to data skills and one related to workflow.
When solving the data skills challenge, the organization had to take into consideration the different analytic skills of their process experts and data scientists. The disconnect between these two central problem-solving groups had to be overcome.
Solution & Implementation
This problem was solved by adopting TrendMiner self-service analytics which allowed process experts to do the data analytics themselves, thus moving their data skills closer to that of the data scientists. The process experts now had a tool that they could use to analyze the data giving them data-driven insights to make data-driven decisions.
The next step was to capture a way of working so that the personnel would successfully adopt and use self-service analytics. With any new work approach, personnel need to have the ‘mindset’ to
use the new tool and to want to make it a success. It was decided to solve this challenge by showing quick and important wins. Personnel were willing to adopt self-service analytics once they saw how using it could substantially ease their work and improve operations.
Also, with any new work approach to be successful,
‘methods’ and ‘management’ have to be in place. Huntsman created a standardized plan for implementing adoption which included proper management support. With these three aspects in place, Huntsman overcame these challenges allowing the organization’s workflows to go from an experience-driven to a data-driven work.
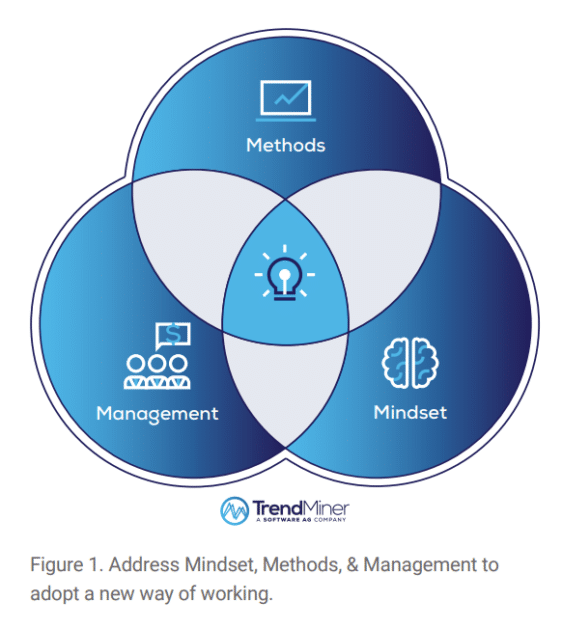
Use Case 1
Setting Soft Sensors For Product Quality Monitoring
For years, a Huntsman continuous isocyanate plant had been collecting daily process and offline-created lab analysis data, both of which were stored in the historian database.
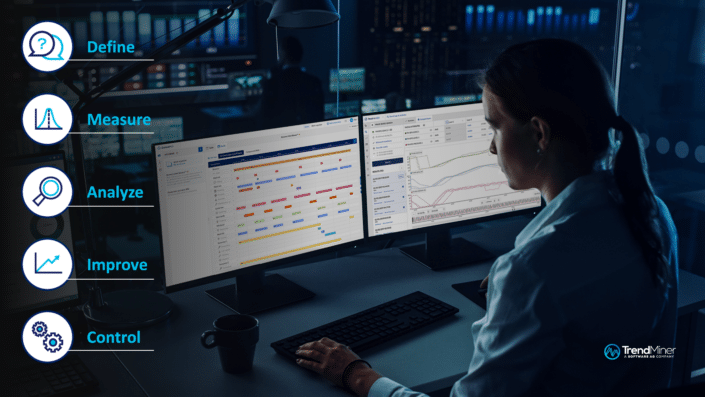
Solution
Early in 2016, the company’s teams used TrendMiner to build soft sensors on operating conditions to predict product quality for certain Isocyanates. The process experts in turn used these to make micro-adjustments to process setpoints to pro-actively minimize impurity levels.
As an example, one of the monitors predicted hydrolyzable chloride levels in the final product, and by tweaking vacuum pressure conditions, the impact on product quality was mitigated. In addition, monitors were set up to send out early warnings to tell the operators not to load trucks, preventing off-spec material from going to a customer.
Results
TrendMiner made it possible to have 24/7 quality control compared to a quality control situation with lab analyses that were only available for regular weekday work hours. With trucks being sent out 7 days per week, the soft sensors eliminated 75% of the expensive off-spec transportation cases which occurred on the weekends. In addition, a significant positive impact on lead time was achieved as unnecessary wait hours for the in-spec products were eliminated, with the average lead time being reduced by several hours. Finally, the extra insights on product quality also reduced the demand on lab resources as the number of uncertain situations for this specific product was reduced by as much as 10%.
Use Case 2
Fingerprinting Batch Processes To Check Product Quality
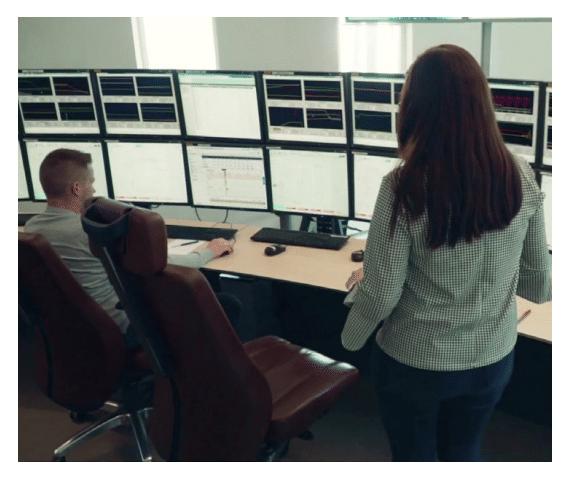
The common practice of the team was to check batch profiles using Excel. This approach required a lot of work, time, and expertise.
Solution
Since the end of 2018, process experts used TrendMiner to create fingerprints to check batch quality against specifications. In one of the Polyols processes, distinct pressure and temperature profiles were required to consistently create high-quality material. To ensure this quality, time-series patterns from known good batches were grouped and saved as a “fingerprint.” The golden batch fingerprint was then used as a real-time monitor to continuously check the process for deviations.
Results
Subtle disturbances that would be difficult to capture in a numerical model were quickly identified using the fingerprint. Likewise, there was no need to check afterward if there were any abnormalities because the monitors gave early warnings for unexpected heat input which allowed operators to take appropriate action in time. This new approach to batch analysis and monitoring led to a significant reduction in off-spec batches and an increase in product quality.
Use Case 3
Quality Improvement Using TrendMiner Capabilities For DMAIC
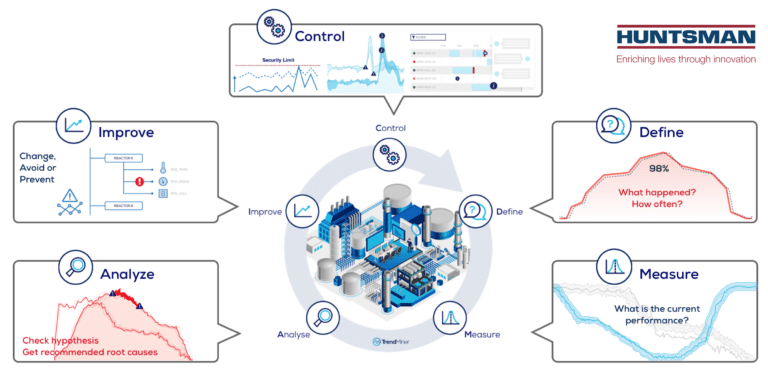
In one of the Advanced Materials plants, many batches in a wiped-film evaporator exceeded the solvent specification limit, resulting in off-spec products. Moreover, this same plant had observed a multi-year drift in quality as measured by the QA lab. Process experts suspected that this issue was due to a change in testing methods; however, the frequency of off-spec production demanded a resolution.
Solution
A complete Six-Sigma DMAIC analysis was performed using the various capabilities of TrendMiner. The analysis included using value-based searches, layer comparisons, statistical comparison tables, scatterplots, filtering, and the recommendation engine.
By observing scatter plots, process experts easily tracked batch performances to see which ones were inside and which ones were outside of the operating zone. Multiple differences between the plant’s on-spec and off-spec production campaigns were revealed. The differences were enough to convince subject matter experts that long-term changes were occurring in the process. Through further investigation, the misreading of flowmeters was ruled out, and a non-negligible offset between measured and true pressure was found.
Results
TrendMiner allowed the process experts to complete a faster root cause analysis on a much larger data set. They were also able to identify differences in the subtle pressure readings and thus call for more tests to be done. After making process changes based on these findings, quality improvements were confirmed within a few days. (Learn more about how you can ensure Continuous Improvement 4.0 through the DMAIC cycle with TrendMiner self-service analytics.)
With the use of TrendMiner self-service industrial analytics, Huntsman process experts:
- Became “analytics enabled” so they could fully leverage sensor-generated time-series data.
- Eliminated data silos.
- Became much more effective in coming up with solutions for operational problems.
- Compared past patterns looking for good and bad production behavior.
- Reduced off-spec batches.
- Performed fast root cause analyzes on much larger data sets.
- Improved product quality.
- Optimized each phase of the classic DMAIC cycle in the Six-Sigma methodology.
Download The Full Huntsman Success Story
Download this free PDF and learn how Huntsman used TrendMiner self-service analytics in its digitalization evolution and production optimization to establish 24-hour engineering support.
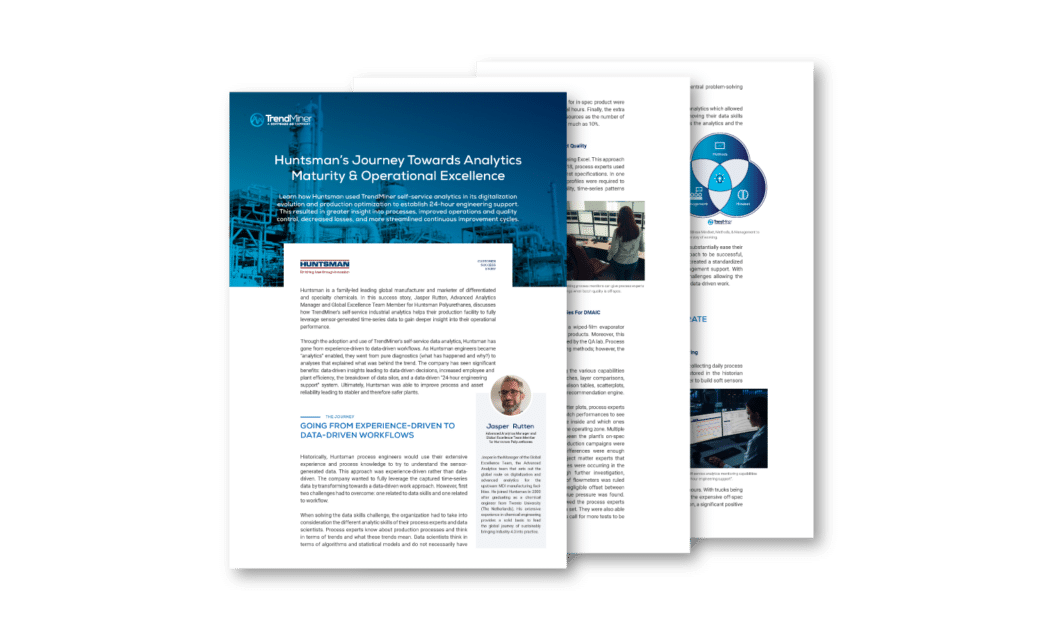
Huntsman Journey & Business Challenges
Historically, Huntsman process engineers would use their extensive
experience and process knowledge to try to understand the sensor-generated data. This approach was experience-driven rather than data-driven.
The company wanted to fully leverage the captured time-series data by transforming toward a data-driven work approach. However, first two challenges had to overcome: one related to data skills and one related to workflow.
When solving the data skills challenge, the organization had to take into consideration the different analytic skills of their process experts and data scientists. The disconnect between these two central problem-solving groups had to be overcome.
Solution & Implementation
This problem was solved by adopting TrendMiner self-service analytics which allowed process experts to do the data analytics themselves, thus moving their data skills closer to that of the data scientists. The process experts now had a tool that they could use to analyze the data giving them data-driven insights to make data-driven decisions.
The next step was to capture a way of working so that the personnel would successfully adopt and use self-service analytics. With any new work approach, personnel need to have the ‘mindset’ to
use the new tool and to want to make it a success. It was decided to solve this challenge by showing quick and important wins. Personnel were willing to adopt self-service analytics once they saw how using it could substantially ease their work and improve operations.
Also, with any new work approach to be successful,
‘methods’ and ‘management’ have to be in place. Huntsman created a standardized plan for implementing adoption which included proper management support. With these three aspects in place, Huntsman overcame these challenges allowing the organization’s workflows to go from an experience-driven to a data-driven work.
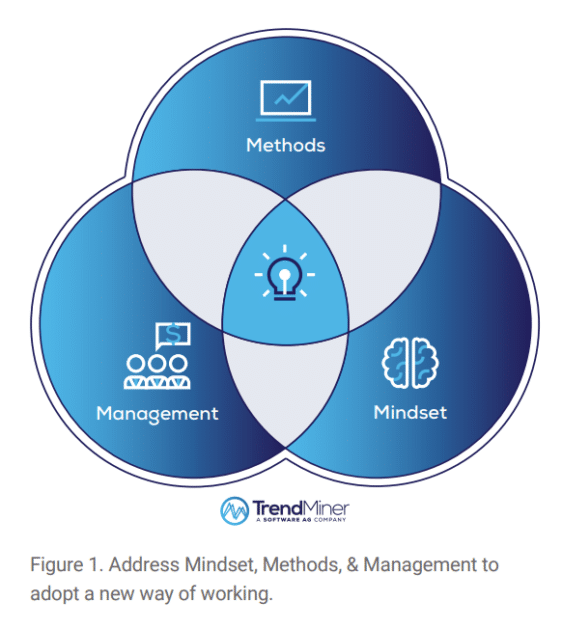
Use Case 1
Setting Soft Sensors For Product Quality Monitoring
For years, a Huntsman continuous isocyanate plant had been collecting daily process and offline-created lab analysis data, both of which were stored in the historian database.
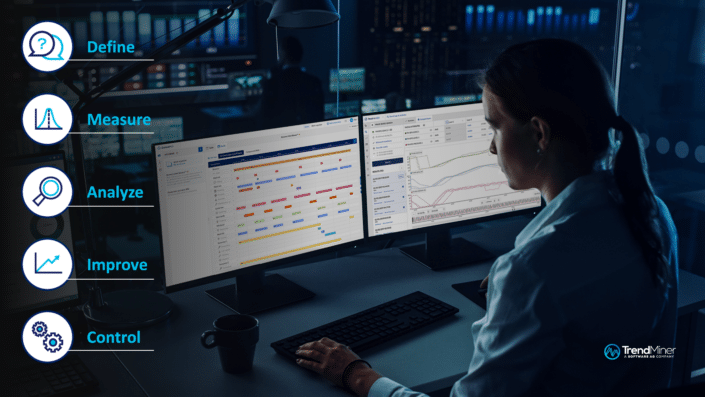
Solution
Early in 2016, the company’s teams used TrendMiner to build soft sensors on operating conditions to predict product quality for certain Isocyanates. The process experts in turn used these to make micro-adjustments to process setpoints to pro-actively minimize impurity levels.
As an example, one of the monitors predicted hydrolyzable chloride levels in the final product, and by tweaking vacuum pressure conditions, the impact on product quality was mitigated. In addition, monitors were set up to send out early warnings to tell the operators not to load trucks, preventing off-spec material from going to a customer.
Results
TrendMiner made it possible to have 24/7 quality control compared to a quality control situation with lab analyses that were only available for regular weekday work hours. With trucks being sent out 7 days per week, the soft sensors eliminated 75% of the expensive off-spec transportation cases which occurred on the weekends. In addition, a significant positive impact on lead time was achieved as unnecessary wait hours for the in-spec products were eliminated, with the average lead time being reduced by several hours. Finally, the extra insights on product quality also reduced the demand on lab resources as the number of uncertain situations for this specific product was reduced by as much as 10%.
Use Case 2
Fingerprinting Batch Processes To Check Product Quality
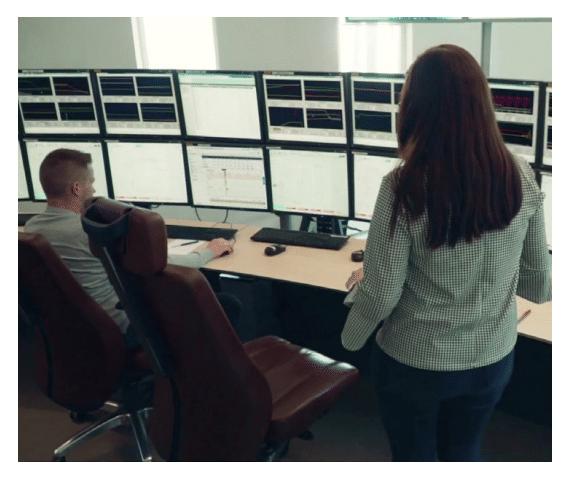
The common practice of the team was to check batch profiles using Excel. This approach required a lot of work, time, and expertise.
Solution
Since the end of 2018, process experts used TrendMiner to create fingerprints to check batch quality against specifications. In one of the Polyols processes, distinct pressure and temperature profiles were required to consistently create high-quality material. To ensure this quality, time-series patterns from known good batches were grouped and saved as a “fingerprint.” The golden batch fingerprint was then used as a real-time monitor to continuously check the process for deviations.
Results
Subtle disturbances that would be difficult to capture in a numerical model were quickly identified using the fingerprint. Likewise, there was no need to check afterward if there were any abnormalities because the monitors gave early warnings for unexpected heat input which allowed operators to take appropriate action in time. This new approach to batch analysis and monitoring led to a significant reduction in off-spec batches and an increase in product quality.
Use Case 3
Quality Improvement Using TrendMiner Capabilities For DMAIC
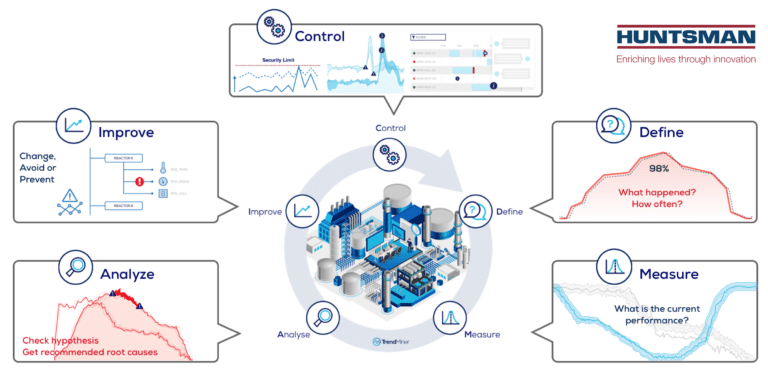
In one of the Advanced Materials plants, many batches in a wiped-film evaporator exceeded the solvent specification limit, resulting in off-spec products. Moreover, this same plant had observed a multi-year drift in quality as measured by the QA lab. Process experts suspected that this issue was due to a change in testing methods; however, the frequency of off-spec production demanded a resolution.
Solution
A complete Six-Sigma DMAIC analysis was performed using the various capabilities of TrendMiner. The analysis included using value-based searches, layer comparisons, statistical comparison tables, scatterplots, filtering, and the recommendation engine.
By observing scatter plots, process experts easily tracked batch performances to see which ones were inside and which ones were outside of the operating zone. Multiple differences between the plant’s on-spec and off-spec production campaigns were revealed. The differences were enough to convince subject matter experts that long-term changes were occurring in the process. Through further investigation, the misreading of flowmeters was ruled out, and a non-negligible offset between measured and true pressure was found.
Results
TrendMiner allowed the process experts to complete a faster root cause analysis on a much larger data set. They were also able to identify differences in the subtle pressure readings and thus call for more tests to be done. After making process changes based on these findings, quality improvements were confirmed within a few days. (Learn more about how you can ensure Continuous Improvement 4.0 through the DMAIC cycle with TrendMiner self-service analytics.)
With the use of TrendMiner self-service industrial analytics, Huntsman process experts:
- Became “analytics enabled” so they could fully leverage sensor-generated time-series data.
- Eliminated data silos.
- Became much more effective in coming up with solutions for operational problems.
- Compared past patterns looking for good and bad production behavior.
- Reduced off-spec batches.
- Performed fast root cause analyzes on much larger data sets.
- Improved product quality.
- Optimized each phase of the classic DMAIC cycle in the Six-Sigma methodology.
Download The Full Huntsman Success Story
Download this free PDF and learn how Huntsman used TrendMiner self-service analytics in its digitalization evolution and production optimization to establish 24-hour engineering support.
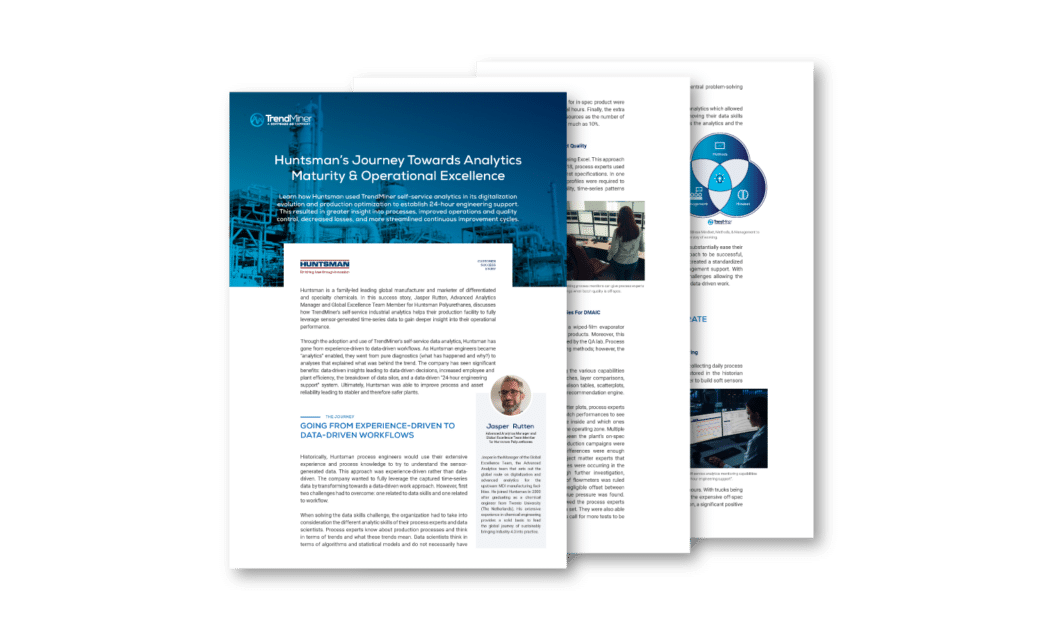
Download now
Subscribe to our newsletter
Stay up to date with our latest news and updates.
Other Webinars on demand
Explore Our Newest Content to Maximize Your Operational Efficiency
Other Resources
Explore Our Newest Content to Maximize Your Operational Efficiency