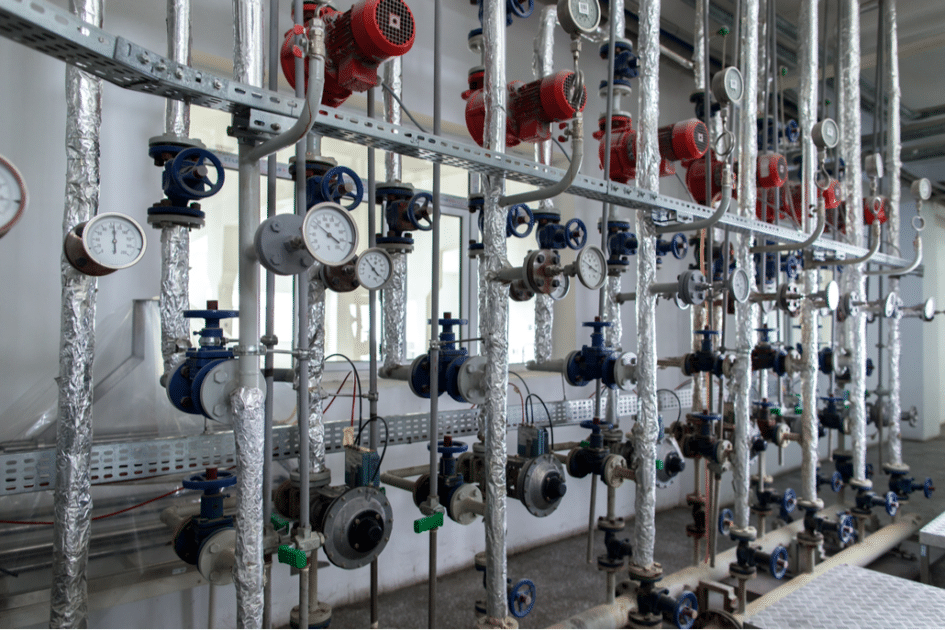
Situation
A plant in the food industry is chemically modifying starch for use in various applications, and coagulation is an important part of their production cycle. In this process, small protein particles are coagulated to form larger particles that can easily be separated in the next processing step. The coagulation process is operated continuously during campaigns, so downtime needs to be avoided.
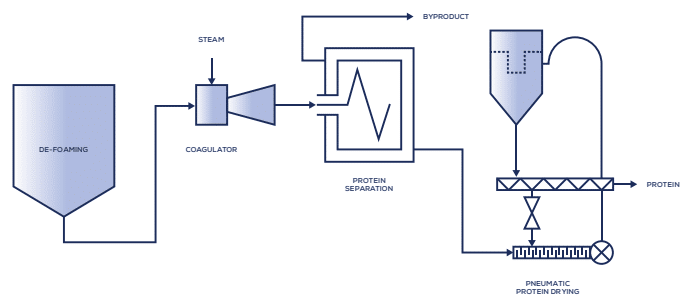
Problem
During the last campaign, the coagulator failed significantly more often than during previous campaigns. The engineers needed to figure out why this was happening and how to prevent this behavior moving forward. Due to the complexity of the issue, and the team’s lack of an analytics expert, they could not identify a root cause before using TrendMiner. In fact, they didn’t know where to begin, so with TrendMiner’s help they formulated hypotheses to test.
Solution
TrendMiner’s descriptive, discovery, and diagnostic functionalities were used to analyze the team’s operational data and formulate a hypothesis. Once this was done and the issue was remediated, TrendMiner’s fingerprint capabilities were used to set up monitors that would notify the team of future problematic behavior. The steps taken were:
1. Descriptive Analysis (What has happened?)
Tags relevant to the unit operation & problem were used to analyze historical performance. This indicated when the decline from baseline performance began.
2. Discovery Analysis (When did it happen?)
TrendMiner’s similarity search was used to retrieve all coagulator shutdowns to assess the impact of the problem. This showed that from September until November of the previous year, the coagulator unit tripped 44 times. This was alarming because the unit only tripped a handful of times during the prior campaign.
3. Diagnostic Analytics (Why did it happen?)
Further analysis with TrendMiner’s layer comparison tool allowed users to quickly compare good and bad periods and identify the process parameters that were different. Good periods were when the coagulator did not fail for a significant period. Bad periods were right before coagulator failure. The layer comparison showed that the flow of process water towards the coagulator was lower during bad periods of operation. The root cause for the decreased flow was caused by an increased pressure in an upstream flash tank. With this information, the hypothesis was formed that coagulator problems occur due to boiling of the liquid after the coagulation unit. The boiling liquid would indeed result in a higher pressure of the flash tank and would induce inaccurate flow measurements and control signals that potentially shut down the pump.
4. Predictive Analytics (How to avoid it?)
Testing this hypothesis in practice proved that the information found with TrendMiner was true. As a result, they were able to remediate the root cause and prevent further trips. Moving forward, it was critical to warn engineers when similar behavior occurred. With the high pressure value as predictive trigger, TrendMiner is now used to send a notification to the operators so they can quickly address future issues if they occur.
Results
Through their use of TrendMiner, the team was able to investigate and resolve a persistent issue with their coagulator unit. Without needing the help of a data scientist, they were able to develop the hypothesis that coagulator problems occur due to boiling of the liquid after the coagulation unit. They addressed the issue and saw immediate results — the coagulator unit tripped 50% less after remediation. Other trips can now be identified and investigated in a similar way.
4 Hours
In only a few hours without help of data scientists the engineers were able to improve the production process.
50% Downtime Reduction
Through the analysis with TrendMiner the root cause was found and early warnings can be send to the operators to avoid trips, helping to reduce downtime with more than 50%.
Situation
A plant in the food industry is chemically modifying starch for use in various applications, and coagulation is an important part of their production cycle. In this process, small protein particles are coagulated to form larger particles that can easily be separated in the next processing step. The coagulation process is operated continuously during campaigns, so downtime needs to be avoided.
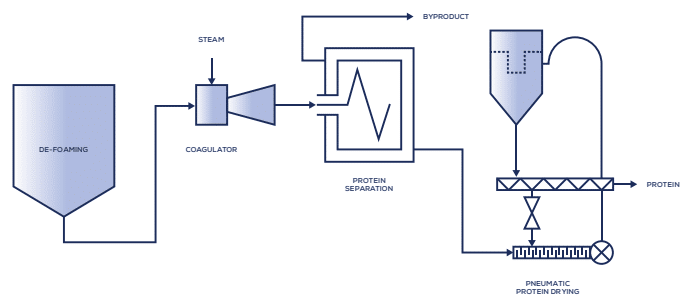
Problem
During the last campaign, the coagulator failed significantly more often than during previous campaigns. The engineers needed to figure out why this was happening and how to prevent this behavior moving forward. Due to the complexity of the issue, and the team’s lack of an analytics expert, they could not identify a root cause before using TrendMiner. In fact, they didn’t know where to begin, so with TrendMiner’s help they formulated hypotheses to test.
Solution
TrendMiner’s descriptive, discovery, and diagnostic functionalities were used to analyze the team’s operational data and formulate a hypothesis. Once this was done and the issue was remediated, TrendMiner’s fingerprint capabilities were used to set up monitors that would notify the team of future problematic behavior. The steps taken were:
1. Descriptive Analysis (What has happened?)
Tags relevant to the unit operation & problem were used to analyze historical performance. This indicated when the decline from baseline performance began.
2. Discovery Analysis (When did it happen?)
TrendMiner’s similarity search was used to retrieve all coagulator shutdowns to assess the impact of the problem. This showed that from September until November of the previous year, the coagulator unit tripped 44 times. This was alarming because the unit only tripped a handful of times during the prior campaign.
3. Diagnostic Analytics (Why did it happen?)
Further analysis with TrendMiner’s layer comparison tool allowed users to quickly compare good and bad periods and identify the process parameters that were different. Good periods were when the coagulator did not fail for a significant period. Bad periods were right before coagulator failure. The layer comparison showed that the flow of process water towards the coagulator was lower during bad periods of operation. The root cause for the decreased flow was caused by an increased pressure in an upstream flash tank. With this information, the hypothesis was formed that coagulator problems occur due to boiling of the liquid after the coagulation unit. The boiling liquid would indeed result in a higher pressure of the flash tank and would induce inaccurate flow measurements and control signals that potentially shut down the pump.
4. Predictive Analytics (How to avoid it?)
Testing this hypothesis in practice proved that the information found with TrendMiner was true. As a result, they were able to remediate the root cause and prevent further trips. Moving forward, it was critical to warn engineers when similar behavior occurred. With the high pressure value as predictive trigger, TrendMiner is now used to send a notification to the operators so they can quickly address future issues if they occur.
Results
Through their use of TrendMiner, the team was able to investigate and resolve a persistent issue with their coagulator unit. Without needing the help of a data scientist, they were able to develop the hypothesis that coagulator problems occur due to boiling of the liquid after the coagulation unit. They addressed the issue and saw immediate results — the coagulator unit tripped 50% less after remediation. Other trips can now be identified and investigated in a similar way.
4 Hours
In only a few hours without help of data scientists the engineers were able to improve the production process.
50% Downtime Reduction
Through the analysis with TrendMiner the root cause was found and early warnings can be send to the operators to avoid trips, helping to reduce downtime with more than 50%.
Download now
Subscribe to our newsletter
Stay up to date with our latest news and updates.
Other Webinars on demand
Explore Our Newest Content to Maximize Your Operational Efficiency
Other Resources
Explore Our Newest Content to Maximize Your Operational Efficiency