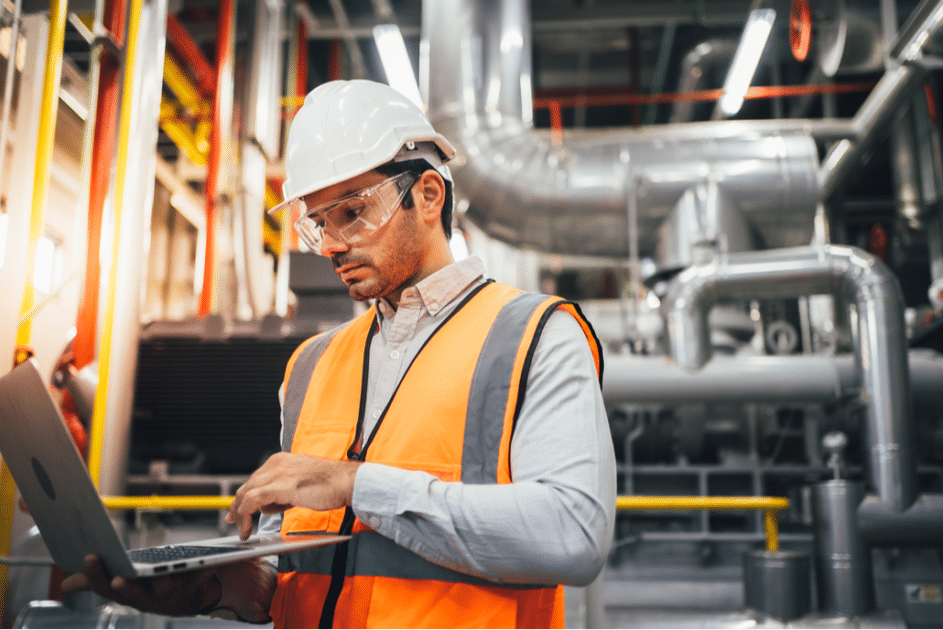
Situation
The plant has a turbo tube dryer where after the reaction the product paste is dried by steaming into a shell and tube heat exchanger with the help of vacuum. The plant has an annual product capacity of 7000MT. The plant was commissioned in 2015 and since then has frequently experienced operational difficulties and problems with product quality. The most important quality parameters which indicate a problem are pH, moisture and % unsulfated matter. A record of the batch runs without any quality issues is also available.
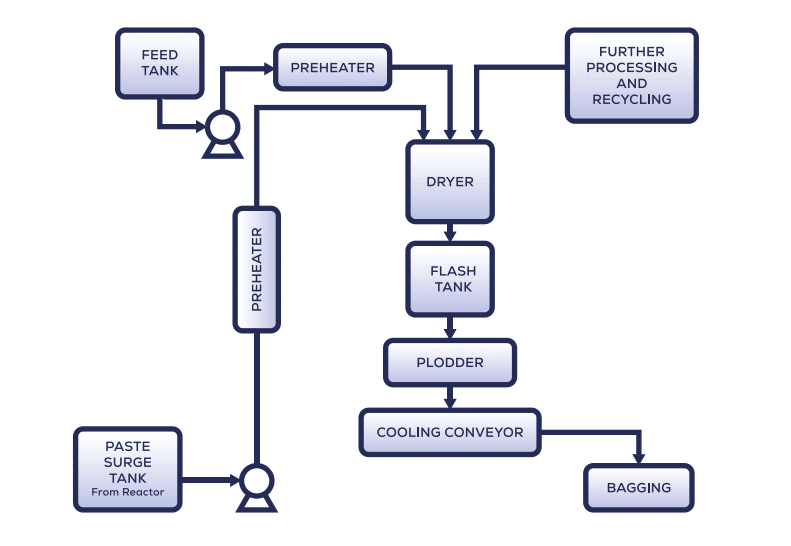
Problem
There were several batches that had issues with the product quality, the cause of which was unclear. For each of the quality indicators, several parameters needed to be investigated. These parameters included pH regulated by caustic flow, % unsulfated matter dependent on organic flow, moisture on dryer temperature and several other dependencies.
Solution
Desired outcomes included the ability to compare a current run and batches with quality issues with the golden runs, and to configure a monitor to send an alert when the live batches showed a deviation from the golden batch behavior. This alert would notify process experts to proactively take action to avoid problems.
The previous system did not make it easy to compare trends since it was used mainly for visualization and not analysis. Additionally, quality information was stored in a separate system, making it quite time consuming to find and compare the right batches.
- Quality data from the lab recorded system was imported into TrendMiner via a CSV file to make finding and comparing batches easier and more efficient. The search functionality was used to retrieve all product runs from the historical data.
- A fingerprint of the good quality batches was created and was used against the bad quality batches for a comparison.
- A monitor was set up based on the fingerprint to look for deviations from the ideal behavior in real time while a batch was in production.
Results
- A framework was established for process experts to quickly gather relevant information from historical data.
- Monitoring was set up to check for deviations in current runs and send alerts notifying process experts proactively.
- Critical batch parameters were identified through the analysis of historical runs, providing experts with key metrics to keep an eye on.
Situation
The plant has a turbo tube dryer where after the reaction the product paste is dried by steaming into a shell and tube heat exchanger with the help of vacuum. The plant has an annual product capacity of 7000MT. The plant was commissioned in 2015 and since then has frequently experienced operational difficulties and problems with product quality. The most important quality parameters which indicate a problem are pH, moisture and % unsulfated matter. A record of the batch runs without any quality issues is also available.
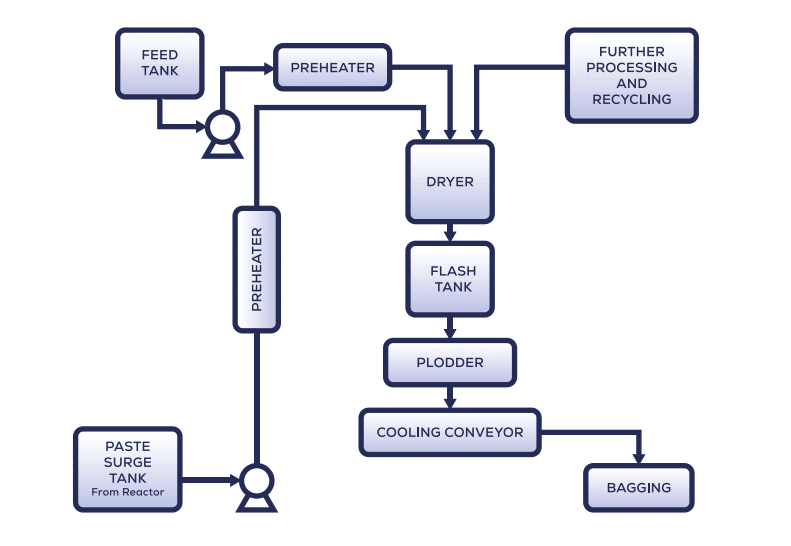
Problem
There were several batches that had issues with the product quality, the cause of which was unclear. For each of the quality indicators, several parameters needed to be investigated. These parameters included pH regulated by caustic flow, % unsulfated matter dependent on organic flow, moisture on dryer temperature and several other dependencies.
Solution
Desired outcomes included the ability to compare a current run and batches with quality issues with the golden runs, and to configure a monitor to send an alert when the live batches showed a deviation from the golden batch behavior. This alert would notify process experts to proactively take action to avoid problems.
The previous system did not make it easy to compare trends since it was used mainly for visualization and not analysis. Additionally, quality information was stored in a separate system, making it quite time consuming to find and compare the right batches.
- Quality data from the lab recorded system was imported into TrendMiner via a CSV file to make finding and comparing batches easier and more efficient. The search functionality was used to retrieve all product runs from the historical data.
- A fingerprint of the good quality batches was created and was used against the bad quality batches for a comparison.
- A monitor was set up based on the fingerprint to look for deviations from the ideal behavior in real time while a batch was in production.
Results
- A framework was established for process experts to quickly gather relevant information from historical data.
- Monitoring was set up to check for deviations in current runs and send alerts notifying process experts proactively.
- Critical batch parameters were identified through the analysis of historical runs, providing experts with key metrics to keep an eye on.
Download now
Subscribe to our newsletter
Stay up to date with our latest news and updates.
Other Webinars on demand
Explore Our Newest Content to Maximize Your Operational Efficiency
Other Resources
Explore Our Newest Content to Maximize Your Operational Efficiency