Reduce Energy Costs in Dairy Processing: Optimize Evaporators and Spray Dryers with Industrial Analytics
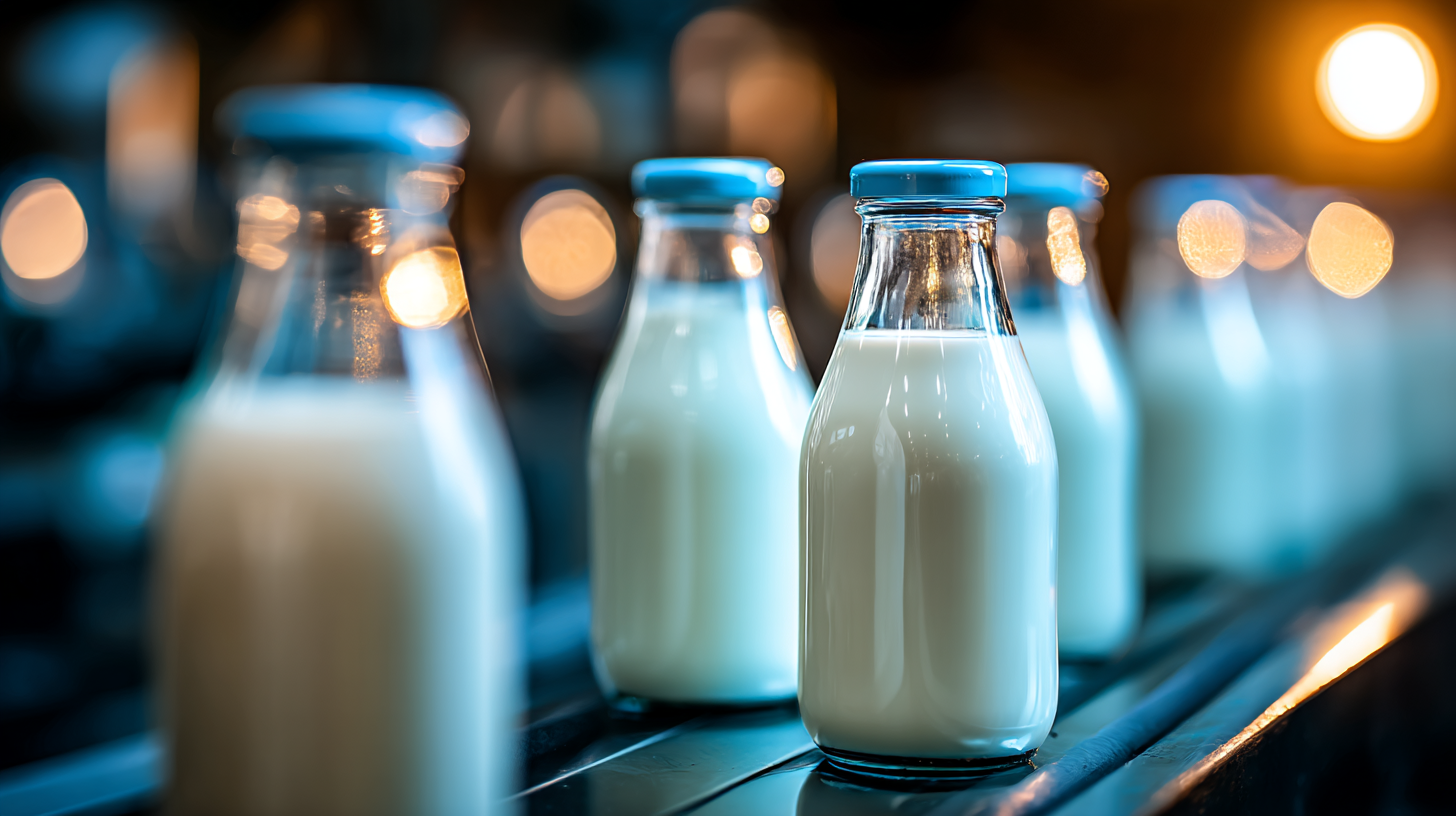
Table of Contents
Energy Efficiency as a Competitive Advantage
Energy efficiency is an important operational factor for dairy plants aiming to manage costs and achieve sustainability goals. The dairy industry has high energy demands, particularly in thermal processes like evaporation and spray drying. These operations often represent over 70% of a facility’s total energy consumption.
As energy costs fluctuate and sustainability regulations evolve, optimizing energy consumption supports both profitability and compliance. In addition, energy efficiency helps facilities meet environmental, social, and governance (ESG) targets and reporting requirements.
The Hidden Costs of Energy Inefficiency
Utility costs are visible on balance sheets, but many sources of energy loss are less obvious and can persist undetected within daily operations.
Key Sources of Hidden Energy Waste
- Fouling and Scaling:
Over time, mineral deposits and product residues build up on heat exchanger surfaces in evaporators and spray dryers. This fouling reduces heat transfer efficiency, requiring more energy to achieve the same processing result. - Manual Operation and Inconsistent Setpoints:
Some facilities rely on manual adjustments or basic automation that may not account for changes in milk properties, ambient conditions, or product demand. This can lead to periods of over- or under-heating, wasted energy, and variable product quality. - Delayed Detection of Anomalies:
Issues may not be detected until they have already led to higher energy use or quality concerns. Systems may operate at suboptimal efficiency for extended periods before corrective action is taken. - Suboptimal Clean-In-Place (CIP) Scheduling:
Cleaning too frequently results in unnecessary use of energy, chemicals, and water, while infrequent cleaning allows fouling to increase energy requirements and may affect product safety.
These issues increase operational costs and can contribute to a higher carbon footprint.
Why Traditional Monitoring Tools Fall Short
Traditional monitoring methods—such as spreadsheets, manual readings, or basic trend charts—have limited effectiveness in managing complex energy systems.
Limitations of Conventional Tools
- Lack of Real-Time Context:
Data may not be available in real time or lack operational context, making it difficult to connect energy use with events on the plant floor. - Limited Ability to Analyze Complex Interactions:
Evaporators and spray dryers involve many variables, including milk composition, flow rates, temperature, and cleaning cycles. Spreadsheets are not designed to handle such multivariate interactions in real time. - Reactive Approach:
Problems are often identified only after they occur. Early warning signs may be missed, resulting in avoidable inefficiencies. - Time-Consuming Data Access:
Engineers may spend significant time compiling and formatting data, reducing the resources available for analysis and process improvement.
These limitations can make it difficult for teams to shift from reactive troubleshooting to proactive management.
How Industrial Analytics Powers Dairy Energy Optimization
Industrial analytics platforms such as TrendMiner help address these gaps by providing tools for continuous monitoring, analysis, and decision support. They enable teams to analyze operational data and identify opportunities for improvement.
Core Capabilities of Industrial Analytics
- Continuous Monitoring of Energy-Intensive Assets:
Analytics tools collect and analyze performance data from evaporators, spray dryers, and supporting utilities, providing an up-to-date view of system health and efficiency. - Pattern Recognition and Fingerprinting:
Advanced algorithms can learn the patterns of optimal operation for each asset. Deviations from these patterns are flagged for further review. - Root Cause Analysis:
When anomalies occur—such as increased steam usage or changes in dryer outlet temperature—the system can help identify underlying causes. - Predictive Alerts:
Analytics tools can issue early warnings when indicators such as heat transfer efficiency begin to decline, supporting more timely interventions. - Self-Service Analytics:
Many modern platforms are designed for use by process experts, enabling teams to conduct analysis without requiring specialist IT support.
These capabilities allow organizations to reduce costs and improve operational reliability.
Case Examples from Dairy Manufacturing
Dairy processors have used analytics-driven approaches to identify and correct energy inefficiencies, often with minimal changes to existing infrastructure.
Case 1: Reducing Evaporator Fouling
A dairy plant observed increasing steam consumption in its multi-effect evaporator. Using analytics, the team identified a gradual reduction in heat transfer efficiency due to fouling.
- Action: The cleaning schedule was adjusted based on real-time performance data.
- Result: Energy consumption was reduced by 12%, providing annual cost savings.
Case 2: Stabilizing Spray Dryer Performance
Another plant experienced recurring energy spikes and product quality issues during spray drying. Analytics revealed inconsistent inlet air temperatures and varying feed concentrations.
- Action: Operators used real-time monitoring to improve control over process variables.
- Result: Energy use decreased by 7%, with improvements in product quality consistency.
Case 3: Integrating Energy and Cleaning Schedules
A third facility analyzed the relationship between CIP activities and energy use, discovering opportunities to better align cleaning with operational needs.
- Action: The CIP schedule was adjusted to target lines showing early signs of fouling.
- Result: Energy costs were reduced by 15% with no negative effect on product safety or quality.
These case studies demonstrate how focused monitoring and data-driven decision-making can improve efficiency.
Aligning Energy Strategies with Operational Goals
Energy optimization should be integrated with other plant objectives, such as product quality, throughput, and compliance. Analytics platforms make it possible to achieve energy savings without sacrificing these priorities.
Balancing Efficiency, Quality, and Throughput
- Monitoring Without Compromise:
Analytics systems track energy use alongside product quality and safety metrics to ensure efficiency efforts do not negatively impact results. - Optimized Cleaning:
Cleaning activities are scheduled based on real-time data rather than fixed intervals, reducing unnecessary downtime and resource use. - Compliance and Transparency:
Automated reporting helps facilities demonstrate compliance with energy and environmental regulations and document progress for audits or stakeholder reporting.
With these tools, energy optimization can support broader business goals.
Energy Optimization as Part of Digital Transformation
Digital transformation in dairy processing increasingly includes energy management as a key focus area. Analytics platforms contribute to this transformation by making data accessible and actionable.
How Digital Tools Support Energy Management
- Real-Time Visualization:
Dashboards provide a current overview of energy performance, helping operators spot and address deviations promptly. - Collaboration and Knowledge Sharing:
Shared digital platforms allow maintenance, engineering, and sustainability teams to work from the same data and insights. - Continuous Improvement and KPI Tracking:
Plants can set targets, monitor key performance indicators (KPIs), and make incremental improvements over time.
Integrating energy management with digital systems supports more effective and coordinated process optimization.
Unlocking Value: Energy as a Source of Competitive Advantage
Improving energy efficiency can contribute to lower costs, stable equipment operation, and progress toward sustainability goals.
- Reduced Operating Costs:
Lower energy use decreases overall operating expenses. - Improved Equipment Reliability:
Predictive analytics support timely maintenance and help prevent unplanned downtime. - Support for ESG Performance:
Documented improvements in energy use contribute to sustainability objectives. - Simplified Compliance:
Automated reporting and documentation can help meet regulatory requirements.
By focusing on measurable improvements, energy management becomes a practical and valuable aspect of plant operations.
Conclusion: Turning Energy from a Cost to a Competitive Lever
Dairy energy optimization can be achieved through the use of industrial analytics, providing benefits such as:
- Lower energy waste and operational costs.
- More reliable and efficient equipment operation.
- Support for sustainability and compliance requirements.
- Improved ability to track and achieve performance goals.
By making use of data and analytics, dairy plants can manage energy use more effectively and improve overall operational performance.
Additional Resources
- Energy Consumption on Dairy Farms: A Review of Monitoring, Prediction Modelling, and Analyses - MDPI
- Digital Tools for Dairy Energy Optimization - Food Engineering Magazine
- Increasing energy efficiency in industry - International Energy Agency
- How Dairy Processors Can Improve Energy Efficiency - Dairy Foods
Frequently Asked Questions (FAQ)
What are the biggest energy consumers in a dairy plant?
The most energy-intensive processes are evaporation and spray drying, accounting for the majority of thermal energy use. Refrigeration and CIP systems are also significant contributors.
How can energy inefficiency be detected early?
Continuous monitoring with analytics tools can reveal deviations from normal patterns, such as reduced heat transfer or increased energy use, allowing for early intervention.
Does optimizing energy impact dairy product quality?
When managed appropriately, energy optimization can maintain or improve product quality by reducing process variability and improving control.
What role does data play in energy optimization?
High-quality, contextualized data provides the foundation for real-time insights, trend analysis, and predictive maintenance, all of which are essential for efficient energy management.
Are there specific KPIs for energy efficiency in dairy plants?
Yes. Common KPIs include energy consumption per unit of product, benchmarks for equipment performance, deviations from baseline usage, and steam-to-milk ratios.
This content was generated using AI. While TrendMiner strives for accuracy, we encourage readers to verify important information. We use AI-generated content to increase efficiencies and provide certain insights, but it may not reflect human expertise or opinions
Unlock Your Industrial Potential
Discover how our analytics solutions can transform your process industry operations today.
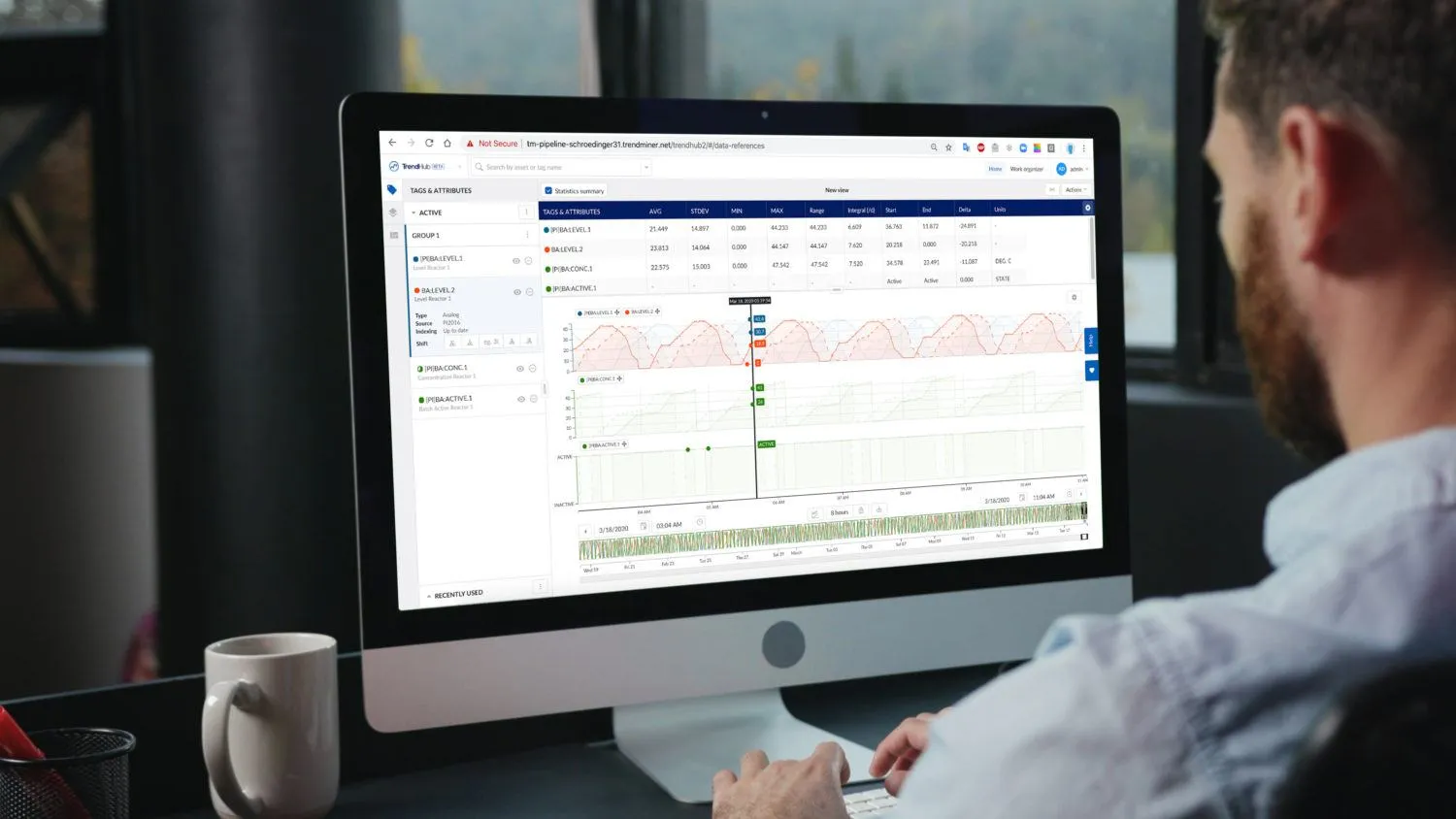
Subscribe to our newsletter
Stay up to date with our latest news and updates.
Latest Resources
Explore Our Newest Content to Maximize Your Operational Efficiency