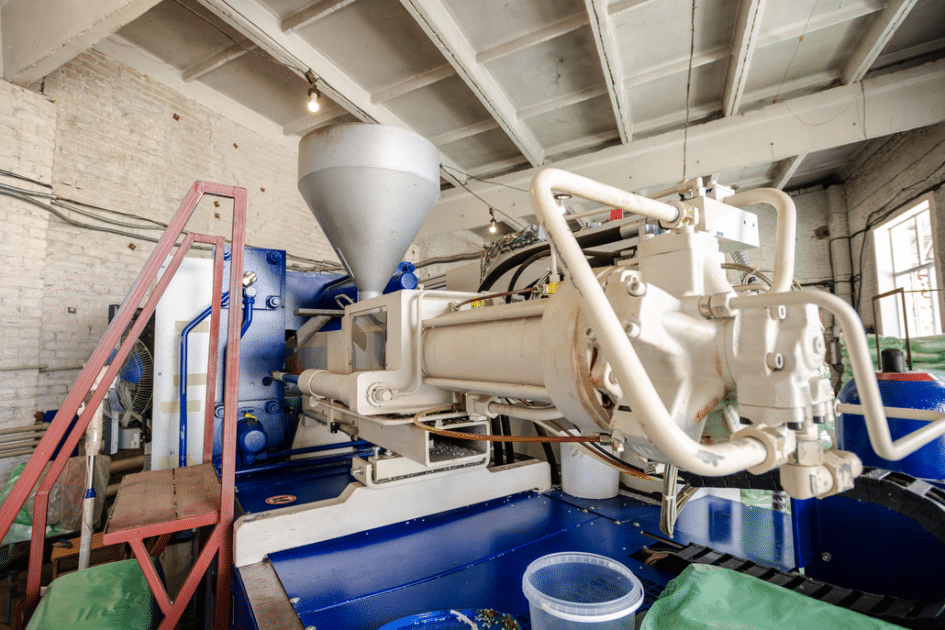
Situation
At this plant, solid particles are produced in a prill tower. In this process, the product is sprayed from the top of the tower and solidifies while falling down. The plant’s goal is to produce as many particles
as possible (in wt%) that fall within the required specifications. The final particle size and distribution depends on numerous factors, and particles that are off specification are discarded.
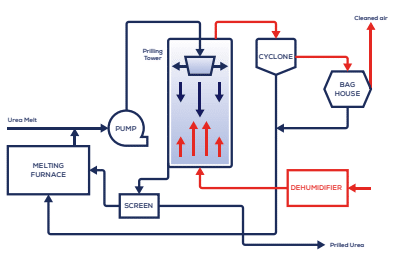
Problem
On average, 25% of the product was not meeting particle size requirements—this meant that a significant fraction of their product was being discarded. Plant engineers suspected that this fraction could be reduced. There were already many hypotheses about the factors that influenced the final yield or efficiency of the prill tower, such as the temperature in the tower and the feed. The engineers sought to test and quantify these relationships, but experienced difficulties doing so with conventional tooling
Solution
Using TrendMiner, the team was able to calculate yield in a short timeframe. This was important as it was the key variable the team sought to optimize. Once the calculation was made, the team could proceed to test the hypotheses they previously developed.
1. Yield calculation
After being sprayed from the tower and solidifying, the product goes to a solids packaging system where the product is sieved and bagged right away. There is no flow measurement, but rather the bags are placed on a scale and weighted while filling. This meant that a calculation needed to be created to estimate the average yield. This calculation could be derived by the ratio between the amount of particles with the correct particle size by the total amount of particles. By saving and reusing this KPI, the team can now also easily follow up the performance of the tower.
Next, using TrendMiner’s search capabilities and layer comparison tool, the engineers could detect and identify periods with high or low average yield. This step was critical in allowing them to extract valuable information out of their data.
2. Hypothesis 1: Effects of spray dryer temperature on particle size
With the yield calculated, the team could proceed to investigate their first hypothesis, which was that the temperature in the spray dryer had an impact on the yield. The temperature of interest was selected, then a search was done in TrendMiner for periods with a constant flow for at least 5 hours. The results were then sorted based on their minimum and maximum top temperatures. In the TrendMiner compare table it was seen that for periods with a lower temperature, the average yield was significantly higher, with results between 6 and 16% of increased yield. To quantify the relationship, the engineers used the data to create a scatter plot. The trendline showed that approximately for one degree fahrenheit temperature difference the yield can be improved by one per cent for a given constant flow.
3. Hypothesis 2: Effect of feed flow temperature on particle size
After the previous test, a similar approach was taken used to look into the effect of the temperature of the feed flow. The hypothesis was that product with a higher temperature could possibly freeze quicker at certain conditions. Because the feed comes from two seperate tanks, a weighted average was calculated first. The results of the analysis found that nitrogen, temperature, and total feed was the same for periods with lower and higher feed temperatures. No significant effect on the yield could be seen for this period, which meant that this hypothesis could be rejected.
Results
In the past, this plant was forced to discard up to 25% of their final product due to failure to meet specifications. Despite previous efforts, plant engineers were unable to address these inefficiencies using available tools. Leveraging an array of TrendMiner functionality, engineers were finally able to identify the cause of decreased spray dryer yield. The data showed that the yield could be significantly improved when operating under cooler temperatures. In the end, these findings corresponded to an estimated $4 million, resulting in a substantial increase in business value.
6 Hours
Spent by the engineers for assessing and solving the use case, which would have cost days without the use of TrendMiner.
~$4 million
Increase in business value due because it was proven to be able to operate under cooler temperatures.
Situation
At this plant, solid particles are produced in a prill tower. In this process, the product is sprayed from the top of the tower and solidifies while falling down. The plant’s goal is to produce as many particles
as possible (in wt%) that fall within the required specifications. The final particle size and distribution depends on numerous factors, and particles that are off specification are discarded.
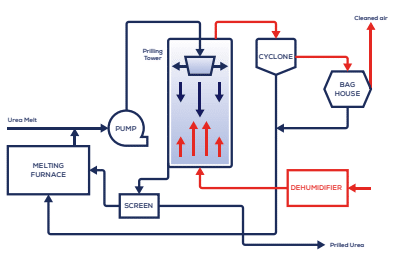
Problem
On average, 25% of the product was not meeting particle size requirements—this meant that a significant fraction of their product was being discarded. Plant engineers suspected that this fraction could be reduced. There were already many hypotheses about the factors that influenced the final yield or efficiency of the prill tower, such as the temperature in the tower and the feed. The engineers sought to test and quantify these relationships, but experienced difficulties doing so with conventional tooling
Solution
Using TrendMiner, the team was able to calculate yield in a short timeframe. This was important as it was the key variable the team sought to optimize. Once the calculation was made, the team could proceed to test the hypotheses they previously developed.
1. Yield calculation
After being sprayed from the tower and solidifying, the product goes to a solids packaging system where the product is sieved and bagged right away. There is no flow measurement, but rather the bags are placed on a scale and weighted while filling. This meant that a calculation needed to be created to estimate the average yield. This calculation could be derived by the ratio between the amount of particles with the correct particle size by the total amount of particles. By saving and reusing this KPI, the team can now also easily follow up the performance of the tower.
Next, using TrendMiner’s search capabilities and layer comparison tool, the engineers could detect and identify periods with high or low average yield. This step was critical in allowing them to extract valuable information out of their data.
2. Hypothesis 1: Effects of spray dryer temperature on particle size
With the yield calculated, the team could proceed to investigate their first hypothesis, which was that the temperature in the spray dryer had an impact on the yield. The temperature of interest was selected, then a search was done in TrendMiner for periods with a constant flow for at least 5 hours. The results were then sorted based on their minimum and maximum top temperatures. In the TrendMiner compare table it was seen that for periods with a lower temperature, the average yield was significantly higher, with results between 6 and 16% of increased yield. To quantify the relationship, the engineers used the data to create a scatter plot. The trendline showed that approximately for one degree fahrenheit temperature difference the yield can be improved by one per cent for a given constant flow.
3. Hypothesis 2: Effect of feed flow temperature on particle size
After the previous test, a similar approach was taken used to look into the effect of the temperature of the feed flow. The hypothesis was that product with a higher temperature could possibly freeze quicker at certain conditions. Because the feed comes from two seperate tanks, a weighted average was calculated first. The results of the analysis found that nitrogen, temperature, and total feed was the same for periods with lower and higher feed temperatures. No significant effect on the yield could be seen for this period, which meant that this hypothesis could be rejected.
Results
In the past, this plant was forced to discard up to 25% of their final product due to failure to meet specifications. Despite previous efforts, plant engineers were unable to address these inefficiencies using available tools. Leveraging an array of TrendMiner functionality, engineers were finally able to identify the cause of decreased spray dryer yield. The data showed that the yield could be significantly improved when operating under cooler temperatures. In the end, these findings corresponded to an estimated $4 million, resulting in a substantial increase in business value.
6 Hours
Spent by the engineers for assessing and solving the use case, which would have cost days without the use of TrendMiner.
~$4 million
Increase in business value due because it was proven to be able to operate under cooler temperatures.
Download now
Subscribe to our newsletter
Stay up to date with our latest news and updates.
Other Webinars on Demand
Press Play on Operational Improvement
Other Resources
Explore Our Newest Content to Maximize Your Operational Efficiency