Unlocking Machine Learning
Clariant Brings ML Models Into Operation(s)
Nimet Sterneberg is helping his chemical engineering colleagues embrace a concept often new to them: data science.
“We have one central department of data scientists, and here we don’t really follow the very classical data analysis approach,” said Nimet, who is a chemical engineer but works in the data science division at Clariant. “So, we are trying to get this hybrid approach in the central department, and almost all of my colleagues are either chemists or chemical engineers.”
Nimet is not alone. Chemical engineers in the manufacturing industry who want to know more about their process behaviors often have turned to data scientists for answers. But this approach creates both a communications and knowledge gap between data scientists and engineers. Engineers can spend significant time explaining a process to a data scientist so he or she can crunch numbers.
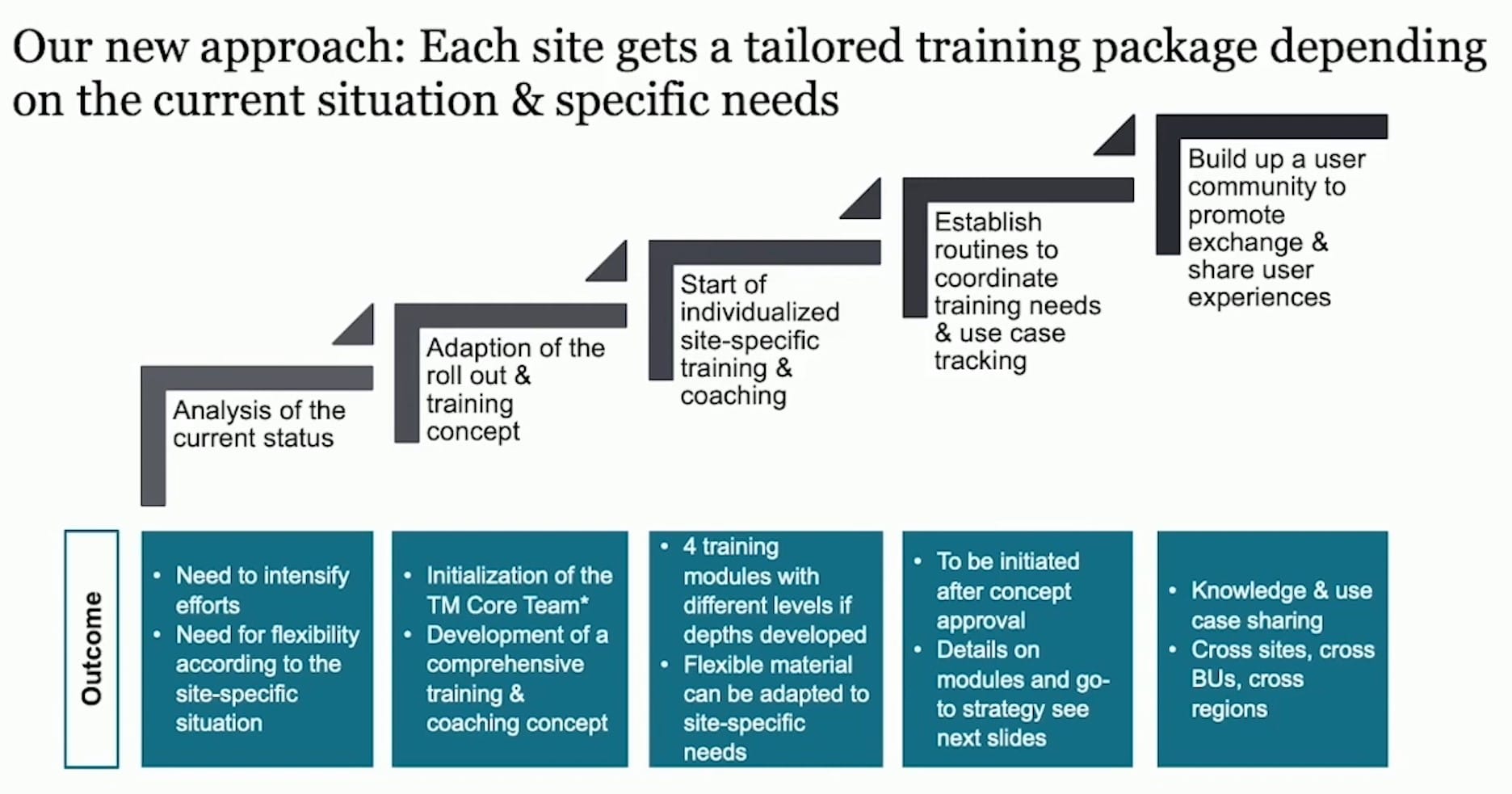
Closing the gap between engineers and data scientists such as myself brings us into the loop so we can work with our end users to do the analysis together. This is where we started to use the Python notebooks at Clariant.
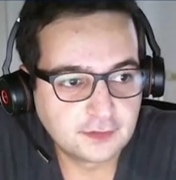
As a result, Nimet is one of the many chemical process engineers who have embraced the power of Industry 4.0 and self-service data analytics solutions to keep data scientists in the loop. They also have implemented a TrendMiner feature that helps them apply machine learning (ML) models for an even deeper dive into process behavior.
Unlocking Machine Learning: Clariant’s Model
Clariant’s digital maturity model is advanced. With TrendMiner as its partner, the company has evolved its plants into augmented factories. It is beginning to use more robust solutions to determine the root cause of process anomalies, but also to apply ML capabilities to its processes. With the ML capabilities, process engineers at Clariant can set up advanced monitoring and alert systems when known parameters deviate from learned behavior.
Nimet and his colleagues are using a TrendMiner feature that rolled out in 2021 to achieve this: The integration of Python notebooks.
“What we do is get the data from the historian using TrendMiner,” said Nimet. “We then gather the time-series data out of TrendMiner and use our own algorithms and our own data science platform, where we then create analytics on top of it, discuss the results, and get opinions for the next steps. Closing the gap between engineers and data scientists such as myself brings us into the loop so we can work with our end users to do the analysis together. This is where we started to use the Python notebooks at Clariant.”
Unlocking Machine Learning: The Power of Analytics
Python is a computer language that has been around since the 1980s. It was invented by a Dutch programmer who wanted to create a language that was powerful but easy enough for anyone to learn and use.
Data scientists use Python because short scripts of its code efficiently and effectively sort large amounts of data, which allows them to gain more insights about it. But the language can be used for a variety of tasks, including establishing ML techniques.
TrendMiner included proprietary Python notebooks with the release of 2021.R1 to improve data analysis and enable machine learning. It extended the notebook functionality in 2021.R2.
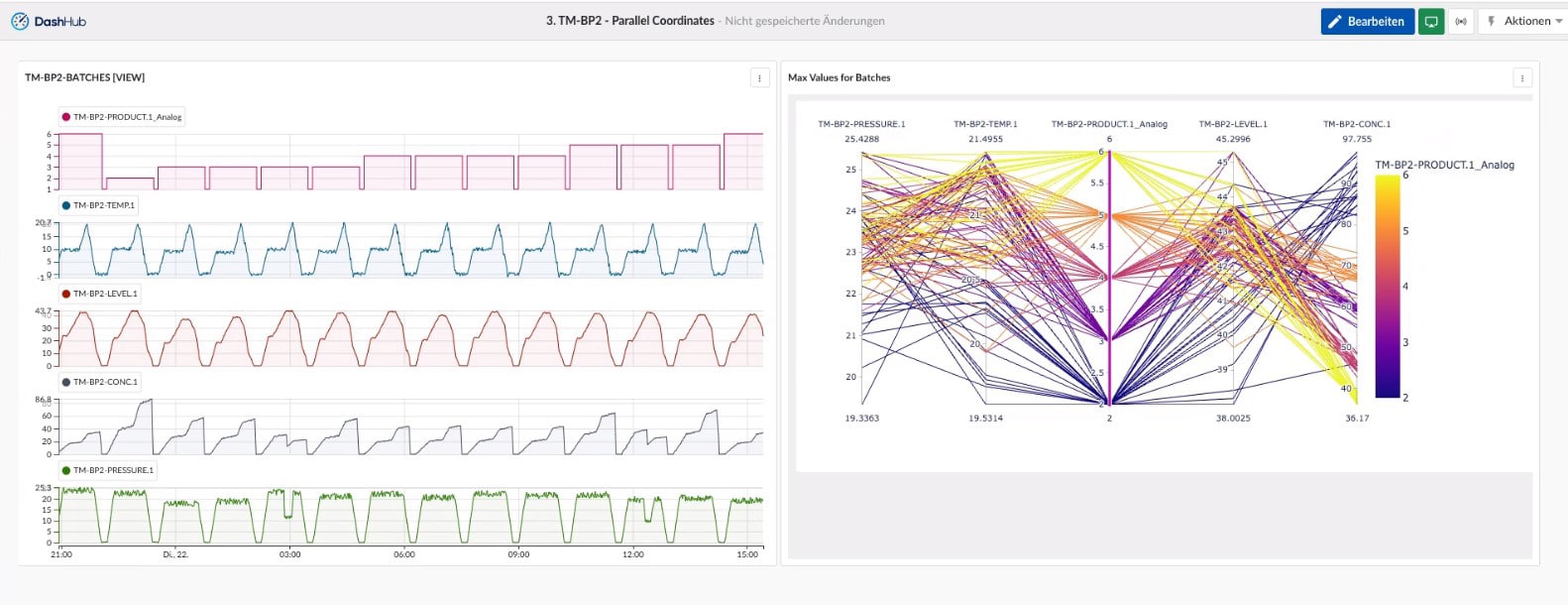
Clariant is using a TrendMiner feature that rolled out with the release of 2021.R1: The integration of Python notebooks. Process experts can view the machine learning parameters next to other tags in DashHub, and even side by side, as shown above. On the left are TrendMiner tags where temperature affects a process. On the right, the machine learning visualization demonstrates the ranges where temperate affects the process. The yellow lines indicate temperature will affect the process in that range, while the blue lines show the opposite. The areas in between can show how close a process is to either end of the range. Each of these lines can be viewed together, as shown, or separately to see just the temperatures that would or would not affect the process.
At Clariant, the data science team took advantage of the integration by improving the company’s DashHub view. It created new visualizations using ML tags in TrendMiner with the Python notebooks integration.
“What we did is we have basically enhanced the dashboard using different visualization types, which were not originally available in TrendMiner,” said Nimet.
Then, the company began supercharging its digitalization program with machine learning capabilities that allow process experts to establish an even stronger golden fingerprint. The software records patterns of good behavior over time. When a process does not match the learned good behavior, process engineers can set up a monitoring and alert system to allow them to take quick action.
“What we are going to do is to use this machine learning model (or machine learning tasks) that we’ve built to create more monitoring and alarms,” he said.
Unlocking Machine Learning: Realizing Greater Efficiency
As Nimet and his colleagues have increased their skill set with the addition of ML capabilities, they also found they gained greater efficiency across Clariant’s operations.
“We see notebooks and TrendMiner as a very powerful and very useful tool and feature,” said Nimet. “We were not chemical data scientists from the beginning. We evolved ourselves into data scientists. So, we are using advantages of classical engineering or chemical engineering and data-driven modeling. Each site has their own needs or pain points. In most of the cases, however, increasing throughput to improve production and make money is the goal.”
Check out Nimet’s 2021 TrendLab presentation where he describes how Clariant is unlocking machine learning for process experts across its plants.