Sustainable Data Analytics: Cutting CO₂ Emissions
The Chemical Industry has found itself in a frenzy of environmental challenges, but sustainable data analytics can help chemical companies stay green.
Chemical companies generate 6% of global greenhouse emissions. When the Paris Agreement was signed in 2015, governments worldwide set a goal to decrease global warming to 1.5 degrees Celsius. The United Nations Climate Change Conference reiterated that goal in November 2021.
In fact, the goal is net zero emissions—putting the same amount of carbon dioxide in the environment as was taken out during the manufacturing process.
Process engineers have the task to ensure their plants are recapturing emissions correctly while optimizing operations. This makes the industry a prime candidate for digitalization and a self-analytics solution.
Self-Service Sustainable Data Analytics
Chemical plants were early to the digitalization game. They used Industrial Internet of Things (IIoT) to capture raw process data from sensors throughout the facility.
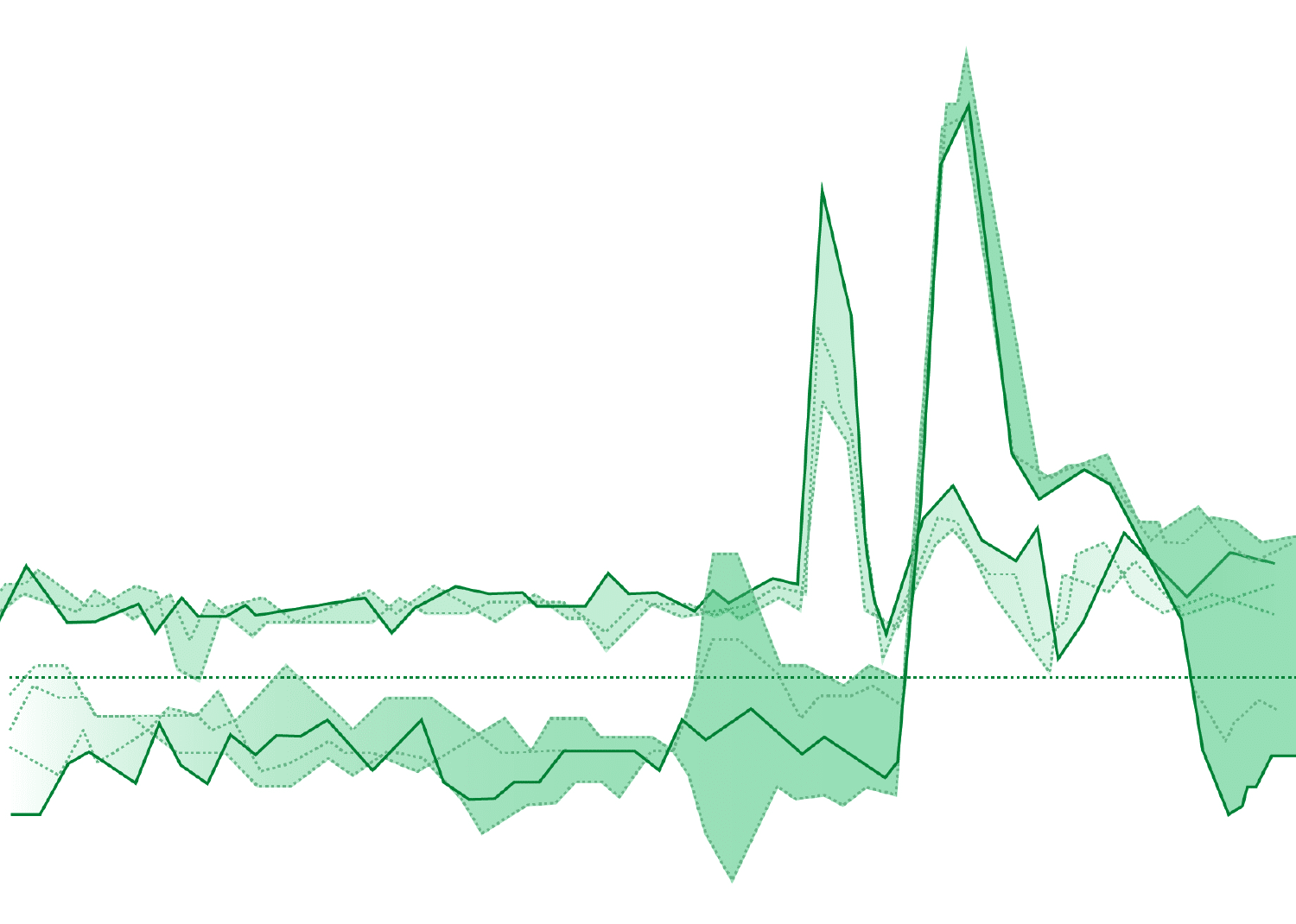
Interpreting raw data against working processes historically has required collaboration between process experts and data scientists. This can be a costly, time-consuming process. With self-service analytics, process experts are empowered to visualize the data themselves and quickly determine the root cause of process anomalies.
In addition to detecting anomalies in the process, process engineers themselves can help optimize production and reduce energy and costs by analyzing historical data to ensuring processes are operating as expected. Leveraging time-series sustainable data analytics to the max, chemical companies can reduce CO2 emissions and use raw materials more efficiently.
Eliminating Emissions With Sustainable Data Analytics
Estimates indicate that improving the energy efficiency in a chemical plant can save emissions by up to 20%. Still, chemical plants use many processes that are energy-intensive and difficult to manage.
Conserving energy is a quintessential benefit of TrendMiner. Process experts can visualize energy consumption across processes. Using the time-series data, they can determine what triggers a rise in energy costs. This allows them to adjust for optimal energy performance.
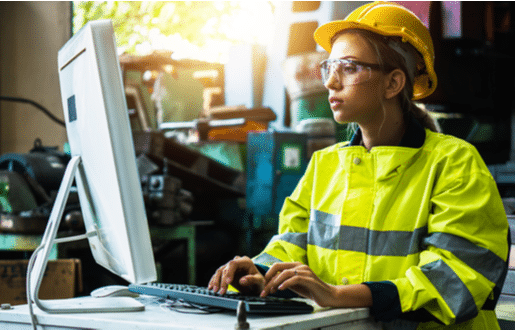
Process experts can set monitors to pick up on process anomalies that can lead to an increase in energy consumption or a loss of emissions. Optionally, they can make necessary adjustments to the process to ensure it is running as expected.
With TrendMiner, the process experts can analyze retrofitting and other process changes involving more sustainable technologies. They easily can evaluate the effectiveness of the investment, monitor the current performance, and identify root causes of possible production losses.
Another benefit is that self-service analytics for time-series data can be used to improve waste management. Process experts can optimize utilities consumption, such as water, air, gas, energy, and steam (WAGES).
The software enables fast and efficient communication within a company. It improves knowledge exchange between different teams and stakeholders, which ultimately contributes to operational improvements.
Use Case #1: Reducing CO2 Using Sustainable Data Analytics
LANXESS, a leading chemical company in Europe, significantly lowered its CO2 emissions at one of its phosphorous plants using TrendMiner. In addition to diminishing the effect of emissions on the environment, the software was able to help the chemical company optimize its productivity with sustainable data analytics.
Thanks to digitalization and the use of TrendMiner, LANXESS’ phosphorous plant has saved around 600 kilograms of steam an hour and slashed about 4,000 metric tons from its annual greenhouse gas emissions. Meanwhile, the company saved EUR 80,000 to 100,000 a year. LANXESS also said it expects savings to grow because the plant had not been running under full capacity during the COVID-19 pandemic.
Use Case #2: Recovering Sulfur With Sustainable Data Analytics
TrendMiner also has been used in the Oil & Gas Industry to optimize a sulfur recovery unit, which is a process used to capture sulfur to avoid it being released in the environment. Sulfur also is used in other manufacturing processes and can be sold as a commodity.
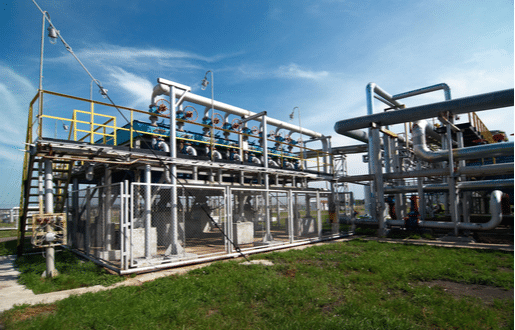
A monitor in the TrendMiner production cockpit at a gas processing plant showed that the non-converted Hydrogen Sulfide (H2S) was higher than expected, which indicated a decrease in recovery rate. The issues were not immediately clear using the tags around the H2S analyzer.
TrendMiner suggested a correlation between the temperature after the first clause unit upstream and the H2S analyzer value. The company was able to correct the issue quickly. Also, fluctuations and steam in the sulfur flow around the first clause unit and the inlet temperature were monitored to stabilize the process.
Sustainable Data Analytics Summary
As environmental regulations continue to grow, industries are finding digitalization and data analytics can help them reach their legal and business goals.
Each part of the production process can be continuously optimized towards net-zero operations. By putting advanced analytics capabilities in the hands of process experts, they can contribute daily to the sustainability goals of the company.